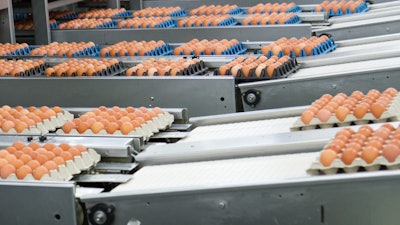
The U.S. food processing industry consists of approximately 21,000 companies and $750 billion in annual revenue. This industry makes extensive use of automation, which requires the seamless operation of many moving parts. Sealed ball bearings, including those mounted in housings, are the unassuming - but vital - component at the heart of this automation. These bearings are often exposed to extremely harsh environments and operating conditions. Meat processing equipment, for example, is subject to routine high-pressure wash-downs, often with bleach and other harsh chemicals. Equipment reliability can be greatly improved when designers make the right decisions in specifying bearings.
Mounted bearing units are typically used to support shafts, align conveyor tracks, or maintain conveyor belt tension. These components are assemblies made of a housing and a retained bearing. There are multiple housing variations available, with the pillow block and two-bolt flange styles the most common in food processing equipment. These units are good for low torque, lightly loaded applications. Another housing configuration is the take-up unit, ideal for use in conveyor applications. In the meat and poultry sectors, high strength housings called plummer blocks are often required to transfer ample power and support heavy loads.
Examples of different sizes of pillow blocks (rear) and insert bearings with eccentric locking collars (front).AST Bearings
Material
When selecting a housing, the type of material is an important consideration. Cast iron or ductile steel are the most common materials used. These housings are painted to provide a minimal amount of surface protection. For food processing equipment subject to wash-down environments, stainless steel is more suitable. Other corrosion resistant housing options include nickel-plated cast iron and thermoplastic. While lacking the strength of iron and steel, thermoplastic housings are highly resistant to moisture, including a wide variety of wash-down chemicals. All housings, regardless of material type, should have smooth surfaces with flat mounting bases and be free from recessed areas. This design allows for effective cleaning and eliminates the possibility of food by-products or debris getting caught in the housing, which can lead to bacterial growth and unsanitary conditions.
The bearings mounted in housings are often referred to as insert bearings. Selection of these bearings is based on shaft size, loading conditions, and rotational speed. Insert bearings are typically manufactured from 52100 chrome steel, which is suitable for most applications. In corrosive or wash-down environments, however, 440C stainless steel is highly recommended. The inner ring on an insert bearing is commonly extended on one side. This design allows for the use of set screws or locking collars to secure the rotating shaft of the equipment to the inner ring of the bearing. The most common and economical method for securing the shaft in place incorporates two set screws set 90⁰ apart. Eccentric locking collars can be used instead of screws when a stronger connection is needed to prevent slippage or fretting between the bearing bore and the shaft. Both methods have a disadvantage of shifting the shaft centerline off the centerline of rotation of the bearing. This condition can introduce vibration, which is undesirable and can reduce bearing life. Concentric locking collars should be selected when this is of concern. These collars have the added benefit of improving the strength of the connection between the shaft and the bearing bore, as well as increasing the push-off force required to remove the bearing.
Sealing
Contamination is a leading cause of premature bearing failure. Sealed bearings should always be used in food processing applications to ensure trouble-free equipment operation. The typical bearing seal configuration consists of nitrile rubber, bonded to a steel insert, with a flexible lip that contacts the circumference of the inner ring. A stamped steel shield is often affixed to the outer side of the seal which protects the rubber from damage. While these contact seals increase rotational torque, they are very effective at preventing the ingress of foreign debris and retaining lubricant in the bearing. Specially designed double and triple lip seals are also available. While these styles of seals increase torque significantly, this disadvantage is seen as a design trade-off to improve bearing life in severely contaminated environments.
Four-bolt flange mounted bearing units shown in three different materials (L-R): thermoplastic, stainless steel, and cast iron.AST Bearings
Lubrication
Lubricant selection is critical to bearing life and performance, yet it is often overlooked by designers and engineers. Bearing life depends on “proper” lubrication, meaning both type and amount. Operating temperature is the primary consideration when selecting a lubricant. Temperature directly affects the viscosity of the lubricant base oil, which in turn impacts the lubricant’s ability to support application loads. Food processing applications are often subjected to temperature extremes and caustic wash-downs, which can degrade the quality of a lubricant significantly. Manufacturers of food processing equipment are often required to use a special class of lubricants, referred to as food-grade lubricants. These lubricants are classified into three categories, based on the probability of contact with food products. While currently under the purview of the NSF, the USDA created the original food-grade designations H1, H2 and H3, which are still used today. These designations are defined as follows:
- H1 lubricants are those used in food processing equipment and on machine parts where there is a possibility of incidental food contact.
- H2 lubricants are those used in food processing equipment and on machine parts where there is no possibility of food contact.
- H3 lubricants, also known as soluble or edible oil, are those used to clean and prevent rust on hooks, trolleys, and similar equipment.
H2 lubricants are the most often selected grease for mounted bearings used in food processing environments, but each application must be examined closely. Bearings subjected to wash-down should use a lubricant that has water wash-out resistance. Calcium, lithium, and aluminum complex greases, as well as polyurea types, are all excellent choices. PFPE greases can operate at high temperatures and have excellent resistance to a variety of chemicals but are more expensive. Synthetic lubricants in general perform better than mineral based lubricants and protect against the growth of microorganisms. Lubricant additive packages, such as anti-wear and anti-corrosion, are also available. Grease lubrication in an insert bearing can break down and degrade over time, particularly when operating at elevated temperatures. Mounted bearing units are commonly supplied with a grease fitting that allows for the re-lubrication of the insert bearing. Proper lubrication is essential to equipment performance. Maintenance technicians should define a procedure and schedule for re-lubrication of mounted bearing units, based on duty cycles and operating conditions.
The future of the food processing industry will continue to focus on automation design, including the increasing use of robotics and the development of energy-saving, sustainable facilities and equipment. Bearings will continue to play a crucial role in the efficiency, sanitation, and safety of food processing equipment. Proper bearing selection can prevent contamination, reduce required maintenance, and improve overall production quality. Designers and engineers should always consult with a qualified bearing specialist when selecting mounted units to ensure reliable equipment performance and compliance to stringent industry regulations.
Mark Manegold, AST Bearings