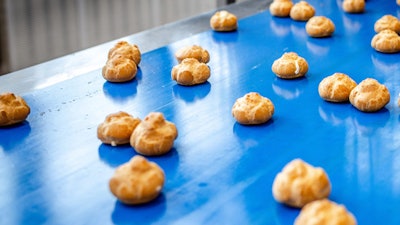
Conveyor belts have been an essential component of the food manufacturing industry for many years, efficiently transporting products from one point to another with minimal human intervention. However, in recent years, the technology behind conveyor belts has advanced significantly, offering a range of new and improved features designed to meet the food industry’s specific needs.
One of the early improvements in conveyor belt technology for the food industry was the development of materials specifically designed for this environment. Traditionally, conveyor belts have been manufactured from materials such as rubber or PVC, which can be prone to cracking or breaking down over time. However, newer materials such as polyurethane and silicone are now being used, which are more durable, resistant to wear and tear, and able to withstand a range of temperatures and chemicals common to this industry.
As technology grew, so did our ability to better fabricate these belt products. We began to slowly move away from using glues and adhesives to hold the ends of the belts together. We also began to eliminate the use of metallic fasteners for splices. Nonmetallic belt splices began to enter the market, providing a safe alternative that avoids food contamination from damaged splice material. Equipment also became more cost-effective, so end users could afford to splice their belt materials in-house. This provided a smooth, homogeneous splice to eliminate the possibility of contamination.
Additional fabrication capabilities that have evolved within the conveyor belt market are high-frequency welded or hot-air welded belt edges—sometimes known as sealed edges. This fabrication safely and securely closes off the fabric reinforcement of the belt edges to reduce the impregnation of moisture and oils into the belt fabric, which could produce bacteria. It also provides a smooth, polyurethane edge to prevent any “stringing” or contamination of the fabric coming off the belt edge and getting into the food being manufactured.
An innovation from food-industry fabric belts was the modular plastic belt. These brick-laid, interlocking products were revolutionary for moving away from tension-driven fabric conveyor belts to positively driven sprocket engagement with the belt. This allows a damaged belt’s small segments to be repaired and eliminates mistracking. These belts become hard to clean and could break off into pieces that enter the manufactured food, but the improvements over fabric were significant.
The most important innovation and evolution came with monolithic belting, blending these two technologies (Figure 1). This polyurethane product either had no fabric reinforcement or completely encapsulated fabric reinforcement safely away from the food conveyed. This material dramatically improves the ability to sanitize the belt. These items come in smooth or textured patterns and are very quickly and efficiently cleaned. They are also positively driven, thus removing the common mistracking issues of fabric belt. This helps to mitigate belt damage and prolongs its life, reducing the cost of ownership for the end user. They are a little more difficult to install because they require an endless splice. This splicing equipment can be expensive, and some training is required for operation. But it’s a minor caveat for the considerably enhanced sanitation and reduced possibility of contamination or food recalls.
Figure 1. With its many benefits resulting from a blend of technologies, monolithic belting is the most important belting innovation and evolution.Image courtesy of Volta
All three of these products were major technological leaps for providing metal-detectable and now even X-ray-detectable materials in their construction. In the event of belt damage or broken-off small pieces, this material can be detected before entering the final packaged food. This is one of the biggest improvements in the last five years of the lightweight belting food-grade market.
Overall, the latest conveyor belt technology for the food industry is driving significant progress in efficiency, productivity, safety and risk from large product recalls. From new materials and designs to metal detectability, these advances are transforming how food is manufactured and distributed worldwide.
About the Author
Seth Stoner is Director of Product Management for Mi Conveyance Solutions. He has had many roles in his 28 years in the conveyor belting industry. For more information, visit MiConveyanceSolutions.com.