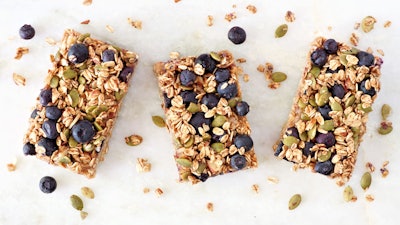
*8 minute read
In its 2019 Global Food and Drink Trends report, analysts Mintel predict that modern takes on sustainability, health and wellness, and convenience will reshape the food industry.
Pierre di Girolamo, Director of industrial metal detector manufacturer Fortress Technology, gives his take on the food safety challenges these trends pose. He also advises how the latest inspection technology can overcome them.
The food industry is evolving at a rapid rate. Whether it’s plant-based cuisine, protein-rich snacks or convenience with class, today’s food manufacturers are having to work harder than ever to please perceptive consumers. Yet whatever the latest trend, the primary aim for producers must always be food safety.
Metal detectors and inspection systems are critical to the food production process. As tastes change, technology must keep pace with evolving food fads if safety standards are to be maintained.
Kitchen Shortcuts
The days of low quality, frozen, bland TV dinners are – thankfully – behind us. Today’s consumers are looking for high-quality meals that will fit into their fast-paced lifestyles, without having to compromise on health or flavor. As a result, convenience food is set to get a major upgrade in 2019.
With Mintel reporting that 27% of US consumers believe it takes too long to prepare healthy food, manufacturers are anticipating a significant rise in so-called shortcut kits. Also known as ‘speed-scratch’ or meal kits, these convenience offerings deliver all the ingredient components required to make a fresh, tasty and nutritious meal at home, without the hassle of weighing, measuring or shopping for each item individually.
According to Pierre, in order to accurately inspect meal kits and ensure they are free from contamination, producers need to ensure their metal detection solution is sophisticated enough to cope with not only different kinds of foodstuffs simultaneously, but also different types of packaging.
Speed scratch meal kits contain lots of ingredients with conductive properties that behave differently during the inspection process.Fortress Technology
Pierre explains, “Each type of food – protein, salad, vegetable, carbohydrate, etc. – has different conductive properties and therefore behaves differently in a metal detector. For example, some proteins are easier to inspect cooked than raw; and salad and vegetables will be easier to inspect than protein. The same principal applies to packaging; metalized foil is more problematic than plastic, for example. And if each item is individually wrapped before being placed into the final box, then the overall packaging will be thicker and sensitivity might be affected.”
Fortunately, there are detectors available that can cope with such challenges. “A metal detector that can run multiple frequencies simultaneously, such as the Fortress Interceptor, is ideal for these kind of elevated convenience products, as it can accurately inspect a variety of conductivities at the same time,” explains Pierre. “Moreover, this kind of detector is an intelligent inspection solution; it will quickly ‘learn’ to recognize the different phases of a complex product and be able to accurately inspect it for signs of contamination, ensuring the final product reaches the consumer exactly as the producer intended.”
Evergreen Consumption
Sustainability has been climbing up the consumer agenda for a number of years, and is set to really take off in 2019, moving towards a 360-degree approach spanning the entire product lifecycle. With plastic pollution hitting the headlines, there is now a drive towards sustainable packaging alternatives in the food industry.
“Bioplastics made from materials such as cellulose pose no problem to metal detectors, as they look and behave just like regular plastic,” explains Pierre. “However, food producers need to be aware of the issues they could encounter with recycled cardboard. Cardboard is shredded during the recycling process, exposing the aluminum that is often found inside it. In fact, the highest contaminant in recycled cardboard is aluminum – this is a conductor of electricity and will trigger an alert on an inspection system.”
“While it is possible to calibrate or reduce the sensitivity on the detector to bypass the alert caused by aluminum, this will also decrease sensitivity on the product,” adds Pierre.
“No producer wants to risk metal contamination. In order to ensure a safe product yet avoid false readings interrupting the production process, we advise our customers to only purchase recycled cardboard from a supplier that has a metal detection system on site; thereby ensuring their packaging is free from aluminum contamination before it enters their factory,” advises Pierre.
Protein Power
Rather than relying on supplements, consumers are moving towards fortified foods that contain elevated levels of supplements such as Omega-3, calcium or iron, or that are rich in turmeric, ginger or garlic; ingredients renowned for their anti-ageing and wellness properties. Also in the shopping baskets of those seeking a healthier lifestyle are products packed with protein. But with the move towards a more plant-based diet showing no sign of decreasing, this doesn’t necessarily mean meat.
The North American protein bar market is expected to grow by 6.25% between 2018-2023.
According to Mordor Intelligence, the North American protein bar market is expected to grow by 6.25% between 2018-2023. However, low-profile foods such as snack bars can cause problems for inspection machines, explains Pierre.
“Just like confectionery bars or cookies, the ingredients used to make protein bars are dropped into a drum before being pressed into the required shape. If a contaminant such as a piece of metal falls into the drum rollers, it will get flattened and crushed, running the risk of it being incorporated into the final product. As these ultra-thin contaminants can be especially difficult to detect, we have developed the Interceptor DF. Using a simultaneous multi-frequency operation, it is the world’s first metal detector to use multiple field directions and greatly improves detection of ultra-thin contaminants, making it ideal for use in low-profile applications.”
A Bright Future
As food trends evolve, inspection machine manufacturers such as Fortress will continue to work closely with food producers to develop solutions that ensure they can keep pace with current trends while maintaining product safety. “The use of mason jars has exploded in recent years, which initially posed a challenge for inspection, as the underside of the lid is metallic,” states Pierre. “But by working with our customers and inspecting the product before it is sealed, or switching to a plastic cap, we are able to ensure the integrity of the contents.”
“Metalized film has also proved challenging,” continues Pierre. “Bread and cookie companies often use it to preserve their products and increase its aesthetic appeal, but its metal content causes a signal on the detector. Fortunately, our Interceptor model can phase this out while increasing sensitivity, thanks to its simultaneous multi-frequency properties.”
In fact, today’s flexible metal detectors are capable of overcoming almost any challenge as Pierre concludes, “I’m confident that whatever food trend is on the horizon, we will be able to develop a solution with the client to successfully inspect it.”
Pierre di Girolamo, Director, Fortress Technology discusses how metal detectors are keeping pace with new food concepts.Fortress Technology