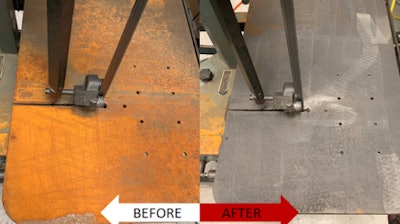
The Los Angeles Times reported about the problem our Navy is having with rust and corrosion. The article mentions the severity of the problem and details how cleaning rust off metal surfaces can be expensive or even dangerous. The article underscores how rust is a billion-dollar problem but fails to highlight that there is an affordable and seamless solution to dealing with it.
The scope of this problem has long been recognized, as countless industries have come to understand the wrath of rust and corrosion. Rust can quickly become a critical concern to seamless operations but solutions to deal with it have been limited. Over the past few decades, the three most commonly used methods to clean metal have been sandblasting, abrasive blasting or chemicals.
However, waste disposal is a headache with all of these methods. Dealing with the remnants of abrasive materials and hazardous, contaminated chemicals can quickly add more costs, equipment, “gray matter”, and processing time. Rust removal and maintenance can become a project in and of itself that needs to be properly managed.
Laser Photonics
These issues are pervasive across industries, as metal fabricators that have painting and powder coating lines must deal with the headaches of large pretreatment systems that require intense oversight to ensure the chemicals create a surface to which the paint or powder can properly adhere. Others in the industry might have to worry about preparing metal surfaces for welding, which requires the right power tool, abrasive, and a lot of elbow grease.
Some might have to degrease metal or remove anodized surfaces prior to further processing. All of these industries know that resources and expertise are required to obtain a surface clean enough for the next step in the fabrication process, for maintenance, or for a re-finishing stage.
Laser Cleaning is a material processing method that uses light to remove contaminants such as rust, paint, grease, oxide, coating, and much more from the surface of most materials while contained in long-lasting, “press and play” machinery.
Materials most commonly receptive of this process are made of steel, aluminum, plastic, and glass. In general, laser cleaning is a modern technology that aims to solve material processing challenges encountered when a unique quality of a surface is required.
Laser Photonics
Laser cleaning systems remove coatings, contaminants, and residues with the use of high-energy fiber laser sources, the same type of power source found in the laser cutting and marking systems. The actual power source of the laser is dependent on the application, but for those looking to achieve speed with ease, powers are available up to the 5 kilowatt range if necessary.
The process is meant to replace the use of chemicals and abrasives to clean these metal surfaces. The operator has the option to place parts in a Class 1 enclosure or manually operate the cleaning process through a Class 4 handheld. The equipment operator can choose to use a preinstalled cleaning pattern or develop a custom pattern to meet a certain surface specification or throughput requirement.
To add even more functionality and convenience, the operator can also adjust a program to include multiple passes using different values for power, frequency, and speed on each laser pass. These capabilities allow for diverse and multi-application usages which can eliminate the need for extra equipment.
Laser Photonics
A significant benefit of using laser technology to achieve cleaning of corrosion and rust off a variety of metals, such as steel, aluminum, stainless steel, galvanized and even reflective metals, like brass and copper, is that the base material (or substrate) experiences no damages.
This laser cleaning technology is available in machinery that can be stationary, portable, or incorporated into assembly lines and structures. Laser cleaning makes the process faster, safer and without the added subsequent costs of waste disposal and materials. Industrial quality laser cleaning equipment can have life spans of up to 10 years or surpassing an MTBF of 100,000 working hours before the need of equipment maintenance.
Rust is a billion-dollar problem, but it doesn’t require a billion-dollar solution.
For more information, visit the industry’s top brand of industrial-grade laser cleaning machines.