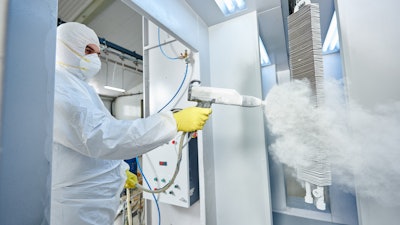
Properly grounding your part is one of the most important steps to take when applying a powder coat. The powder is charged and utilizes an electrical field to attract and adhere to the part before it is baked on. If your part is not properly grounded, then your powder will have a hard time sticking, and may even just fall right off.
According to Coating Equipment Technology (Chesterfield, MI), a grounding rod is one of the best ways to ground your part and should be used over the stock wire and clip that comes with most guns. The difference that it makes is significant. A grounding rod is a 10-12-foot copper rod that you drive into the ground. You leave only a few inches exposed and use that to attach your grounding wire and run it to your hanging rack.
The reasoning for using a grounding rod setup is twofold. First, the grounding rod setup will dramatically reduce, if not almost eliminate, the dreaded “Faraday Cage Areas” that are a nuisance to most powder coaters. These are the recessed areas and tight corners that are shielded by more prominent areas of the part. The powder gets attracted to these larger areas and will not stick to the smaller, more recessed corners and spaces. A grounding rod will minimize these areas. Second, a grounding rod will allow you to spray multiple coats. If you are using the stock grounding wire setup that came with your gun you will have trouble applying multiple coats. This is because the coating itself acts as an electrical insulator, thus subsequent coats of powder will not be attracted to the part after the first coat has been applied. A grounding rod will allow you to apply multiple coats without issue.
Click here for more information on powder coating best practices.