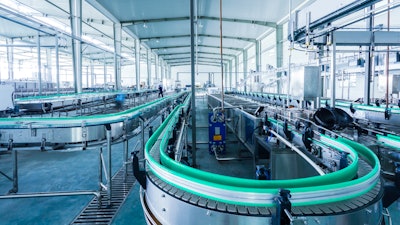
Todayβs manufacturing operations, with a high mix of products or product variations, face a number of challenges when trying to achieve flow, because of their different cycle times, process steps, and materials.
But flow can still be created β the solution is to apply advanced lean techniques to design a future state that supports mixed model production at the pull of the customer.
Mixed model production is the practice of assembling several distinct models of a product on the same assembly line without changeovers, and then sequencing those models in a way that smooths the demand for upstream components
The method used to create mixed model flow includes a five-step process:
- Identify product families, which are groups of products that have similar process flow and similar work content.
- Map the current state for each value stream. The current state map identifies βwhat we do and how we do itβ and is done by walking the shop floor and recording what is observed.
- Ask 10 questions for mixed model flow of the current state map (see below).
- Build the future state based on answers to the 10 questions. The future state describes how the operation will perform once the guidelines have been implemented.
- Create an implementation plan for the future state by breaking the future state down into implementation loops and establishing measurable goals.
Step three (the 10 questions) is very important in operations with many custom product variations. These questions are designed to help you create mixed model value streams:
1. Do you have the right product families?
Establishing product families by grouping products together is not about looking for similarities in sales categories or across customers. Instead, operations strictly look at similar processing steps and work content.
2. What is the takt time at the pacemaker?
To calculate takt time, or the rate at which the pacemaker (the single point where a production process is scheduled) must produce a part to keep pace with customer demand for the product family, use the following equation: the effective working time per time period divided by the customer demand per time period.
3. Can the equipment support takt time?
Determine if existing machine capacity is enough to support the product family within the takt time.
To do this, an organization needs to know:
- Effective working hours
- The cycle time of each product at the machine
- The demand for each product.
To determine the equipment required, divide the sum of the cycle times multiplied by their respective demand by the effective working time.
4. What is the interval?
Calculate how often the pacemaker will produce all the parts in the product family. For example, if it takes one week to produce all the parts in a given product family, then the interval would be one week. Lowering the interval as much as possible is critical to successful mixed model implementations.
5. What are the balance charts for the products?
Create continuous flow through the pacemaker by balancing work content, per operator, to takt time.
6. How will you balance flow for the mix?
Determine how to handle variation within the product family at the pacemaker, either by adjusting labor, scheduling, or work balancing.
7. How will you create standard work for the mix?
Establish the one best way to do a task, and then have everyone follow that method.
8. How will you create pitch at the pacemaker?
Establish how often you will release and take away work from the pacemaker. Pitch is a visual management timeframe that lets you know if you are on time to customer demand.
9. How will you schedule the mix at the pacemaker?
Schedule the pacemaker to handle variation within the product family, and determine the mix the pacemaker can support.
10. How do you deal with changes in customer demand?
Customer demand will vary, and you need to have a Plan B pre-established for when it does, such as pulling product from a supermarket or rebalancing the pacemaker.
By following this approach for mixed model flow, the end result is an operation capable of flowing a mix of parts with varying cycle times and levels of customer demand through the same value stream, all at the pull of the customer.
Kevin Duggan is the founder of the Institute for Operational Excellence and President of Duggan Associates. He will be presenting on November 16 from 1:30-3:30 in the Lean Tools: Flow and Pull session on the topic "Creating Flow in High-Variety Environments," at Fabtech 2016 in Las Vegas.
Specifically, he will address how to apply advanced lean principles to create a value stream of multiple product flows at the pull of the customer with a step-by-step process.