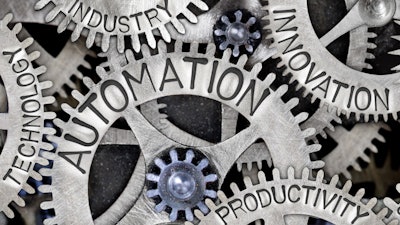
The Internet of Things (IoT) represents a golden opportunity for industrial organizations. Increasingly, IoT is being used to reduce costs and create new revenue opportunities, but it is not a technology that can simply be ‘implemented’.
IoT and other transformational technologies require some degree of introspection and must be used to solve a specific problem or take business operations to a clearly defined future state. This of course brings with it change and disruption not just from a technological standpoint, but in underlying business models. So just how ready are North American industrial companies to embrace disruption?
IoT Sophistication – Double-Digit Growth
A recent IFS research study among 200 North American executives reveals substantial year-over-year gains in IoT usage in industrial companies, and highlights several interesting trendlines over the 12-month period.
It shows a 17 percent increase in companies collecting IoT data on entire work cells or production lines rather than individual machine components or individual machines, a 30 percent increase in use of IoT to support asset performance management, and a 10 percent rise in the use of IoT to monitor customer equipment. These figures all signal transformational approaches toward field service management.
While IoT use cases are becoming more sophisticated, a substantial gap remains between connected devices and transactional software used to run the business—most notably enterprise resource planning (ERP). The study shows the percentage of respondents who have integrated IoT data streams with their ERP software has stayed the same—year-over-year it hovers at 16 percent. This represents a barrier to IoT delivering new business and revenue opportunities which come from connected devices triggering business processes in the transactional system used to run the organization.
A Common Language for IoT and ERP
There are logistical and technical barriers to getting IoT and ERP to talk to each other. IoT tends to create data in a continuous stream, where a sensor may send a record of equipment condition to a plant historian or supervisory control and data acquisition (SCADA) system as often as several times a second.
ERP systems, on the other hand, require data that describes a defined business event. Project teams must define what data the ERP system should collect, and must then determine how an IoT discovery tool can convert the ‘stream-of-consciousness’ style of IoT data into something that tells the ERP system that a piece of equipment needs to be serviced, a technician should be dispatched to a customer site or that a production line should be slowed down to prevent quality issues.
This is one of the main challenges enterprise software will increasingly need to solve—and when it does, it can unlock transformation like never before. IFS Chief Product Officer Christian Pedersen, explains, “Think of the potential for IoT constantly streaming into ERP systems and artificial intelligence (AI) applications constantly learning and applying that knowledge by creating new business logic. That is when AI will see the real breakthrough—and when ERP systems will dramatically transform, changing the way we think about them.”
While companies grapple with IoT-ERP integration, they are progressing much more rapidly when it comes to the sophistication of how they deploy sensors on their equipment. The study asked respondents whether they sensor single components in a piece of equipment, entire pieces of equipment, work cell or production line performance, or networked fleets of vehicles.
One of the most remarkable findings is that in a single year, the number of respondents who reported not using sensors on any equipment dropped by a factor of three—from 15 percent to just under five percent. Another interesting finding is that 17 percent more of our respondents are monitoring entire work cells or production lines.
One to Watch: Asset Performance Management
The IFS research confirmed other study data on the importance of asset performance management (APM), which in part focuses on visibility of assets throughout an enterprise, in driving industrial IoT deployments more rapidly than other use cases. The importance of asset performance management was echoed in a study performed by Market Research Future (MRFR):
“Asset Performance Management (APM) has led to a shift in focus, which is improving reliability, decreasing downtime and reducing unplanned maintenance. MRFR sees the time period from 2016 to 2022 when the focus will be on optimizing the profitability from an equipment. Hence, machine learning and improved big data analytics will allow businesses to decide the best operating profile for the plant based on the order backlog and reliability issues. All these factors will be highly instrumental in augmenting the growth of the market in the foreseeable future.”
Drawing on insights from the IFS study, industrial organizations can make informed decisions, gauge how disruptive technologies such as IoT and AI may fit into their specific business environments and unlock new opportunities for growth. “IoT helps companies transform their businesses, making them more efficient, enabling them to explore new revenue sources and fundamentally change business processes”, says Antony Bourne, President of IFS Industries.
“Experienced partners both in enterprise software and technology platforms can help identify a proven way forward. If industrial companies do not embrace digital transformation, chances are that their business will be the one that’s disrupted by more agile competitors,” he warns.
Charles Rathmann is a Global Senior Marketing Content Strategist at IFS.