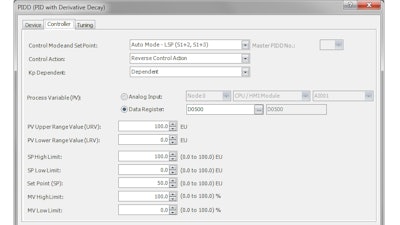
Continuous processes of all types commonly require closed-loop regulatory control of pressure, flow, temperature, level and other analog parameters. Classic proportional-integral-derivative (PID) control has been the go-to method to accomplish this task for decades, but there are some shortcomings. Accurate PID control is obtainable but requires careful tuning to handle disturbances, along with careful implementation to maintain performance.
Perhaps the greatest challenge has been tuning, with estimates indicating about half the PID loops in service are not optimally tuned. Poor tuning makes for inefficient controls, energy waste and equipment wear. Fortunately, several features are now available to make PID tuning and use more user-friendly.
Making PID Configuration Efficient and Easier
Each control system manufacturer has their own specific PID implementation details, calculation methods and settings. But in all cases, PID loops are designed to monitor a process variable (PV) such as a heat exchanger temperature, and then command a manipulated variable (MV) such as a steam valve position to keep the PV as close to the setpoint (SP) as possible. The PID needs to respond quickly and smoothly to process variations, disturbances or SP changes without overshooting or hunting.
Even though basic PID control is commonplace, many times the control systems integration effort leaves a few rough edges, making it more difficult to use for operators and support personnel. These issues can be addressed when the PID configuration software and hardware offer these types of features:
- Bumpless transfer
- Anti-reset windup
- Inhibit
- Floating point accuracy
- Cascade modes
- Derivative decay
- Auto tuning
Bumpless transfer means that when the PID mode is shifted between automatic and manual the MV reacts smoothly without “bumping”. This is simple to implement when going from auto to manual because the auto MV can be constantly copied to the manual MV whenever the loop is in auto, so that upon entering manual there is no bump.
It is more complicated when going from manual to auto because the control algorithm must constantly adjust internal calculations to achieve a smooth transfer. Anti-reset windup is also required so the auto calculation does not get out of hand while the loop is in manual. Both of these features should be built-in to any implementation and not require extra effort to enable.
An inhibit feature is often desired so the user program can keep a PID loop in automatic, but programmatically force it to a fixed position (often 0% MV). Just as with bumpless transfer, upon releasing the inhibit the PID loop should smoothly ramp back to auto control.
Older PLCs tended to offer PID loops using lower-resolution positive-only integer math. For better results, PLCs should instead offer floating-point math to deliver improved accuracy and accommodate bidirectional (negative and positive) scaling.
Some applications require cascaded loops, which is when one PID is nested inside another. This can be tricky to configure since the inside secondary loop must calculate many times faster than the external master/primary loop. A native cascade mode feature makes this option easier for end users to implement without adding custom code.
Derivative decay is a specific addition to the PID algorithm and impacts the PID output after the initial derivative response happens in order to prevent an abrupt disturbance and provide stability to the system. Derivative decay often contributes to smoothing the PID output and avoiding potential spikes during a transitional state, resulting in an improved response and more efficient process control.
Perhaps the PID feature most sought-after by end users is automatic tuning. This often requires users to manually manipulate the PID parameters to some extent, but then allows the PLC to monitor the process response and suggest optimal tuning values. With judicious use, automatic tuning provides optimal control.
Plug-and-Play PID
Many of the preceding PID concepts have been available before or could be implemented with careful coding. The real development here occurs when a modern PLC builds these features right into the native functionality, so they are immediately available to end users, often through simple enablement with controller programming software checkboxes (Figure 1). This requires PLCs and accompanying programming software to offer:
- Plug-and-play for many applications
- Minimal required setting changes, with configuration dialog boxes for any required adjustments
- Interactive monitoring dialog with visual controls and tuning
Figure 1. IDEC’s FC6A Plus and the FC6A All-in-one PLCs are both programmed using their WindLDR software, which simplifies PID controller configuration with drop-down selection for key features.
Once the project is deployed and started up, an interactive monitoring dialog feature within the controller programming software is crucial for users to observe all interactions within the loop and apply tuning adjustments (Figure 2). This allows users to fine tune the PID parameters to obtain optimal performance based on changes made in real-time, with results clearly shown on the screen.Figure 2. PID loops are easily observed and tuned when using IDEC’s WindLDR programming software with its interactive dialog box.
PID is a mainstay for closed-loop process control, but each loop must be tuned correctly to obtain best performance. Features provided with IDEC’s FC6A Plus and FC6A All-in-one PLCs, along with the WindLDR programming software, greatly simplify PID tuning and implementation, allowing users to quickly and easily optimize the performance of each PID loop.
Don Pham has more than fifteen years of detailed experience with industrial automation products including PLCs, HMI touchscreens, machine safety and sensors. He is responsible for product positioning and marketing strategies for these products and works with a research and development team to identify and add features that customers and OEMs are looking for. For more information, visit us.idec.com.