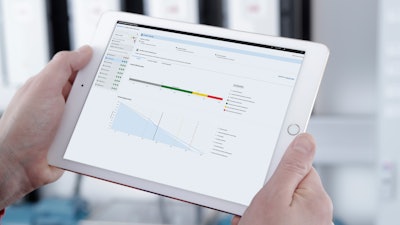
Tight margins, shorter production schedules, aging equipment and growing consumer demand are putting food and beverage manufacturers under more pressure than ever before. To thrive and grow they need to know that they can rely on the availability and cost-efficiency of their manufacturing plant. A potential enabler is digitalization, based on the integration of data and real-time optimization of processes across the value chain. And at the heart of digitalization is a new generation of wireless smart sensors and drive-based digital services.
The Digital Journey Begins with some Simple Steps
The various sectors in the food and beverage industry, such as dairy, meat, brewing and sugar all have their own specific requirements and challenges. One size certainly does not fit all when it comes to finding a digital solution. Intensifying these challenges is the fact that the average plant may be 30 to 50 years old with only isolated pockets of automation limited to programmable logic controllers (PLCs), and supervisory control and data acquisition (SCADA) systems. Another challenge is that solutions from different vendors often use different communication protocols, making it hard to bring them together to provide a seamless overview of how the plant is performing.
Cost is of course a major factor. Not just the cost of the digital technology but also the cost of implementing it and training staff in using it effectively. Therefore, any digital solution must be easy to accomplish and show clear benefits under the tight scrutiny given to prospective large capital expenditure (Capex) projects.
One way to do this is to adopt an incremental approach, working with existing automation systems and seeking to reduce the number of isolated islands of control. Ideally, all pockets of automation would be brought together under a single over-arching system. The adoption of open communication protocols will also avoid being locked into proprietary standards that might limit future expansion and upgrading options.
Smart Sensors – a New Development for Digitalization
A key development in plant digitalization is the arrival of a new generation of wireless smart sensors that utilize the industrial internet of things (IIoT) in the form of cloud computing, data analytics, and mobile data transmission. With no hard wiring requirements, these smart sensors enable permanent monitoring at a fraction of the cost of traditional condition monitoring systems.
Smart sensors can convert traditional motors, mounted bearings, gearing, and pumps into smart, wirelessly connected devices. The sensor picks up data on vibration, temperature, and other asset-specific parameters to provide an overall health check of the equipment. Smart sensors can even identify energy-saving opportunities to optimize energy consumption and lower costs.
Scalable Digital Services for Drives
Variable speed drives (VSDs) are now supported by a range of scalable digital services that allow plant operators to assess, manage and optimize their drives and operations without having to be physically on-site. These digital services make it possible for maintenance teams to monitor, benchmark, back up, predict needed service, and fix drives in a food and beverage production facility from a safe and comfortable distance — across the factory or across the world.
Adopting digital services for drives can deliver many tangible advantages and benefits, the most important being improved safety and efficiency of the production and people. And, if problems arise, drive experts can establish a remote presence to analyze the situation rapidly and make fast recommendations to solve the issues.
Condition Monitoring for Powertrains
The next step in digitalization is to group individual components with sensors, along with variable speed drives, into a digital powertrain. Implementing condition monitoring for powertrains gives plant operators the opportunity to check the health and performance of one unified system. By gaining full visibility, operators can take action to optimize performance, prevent downtime and extend equipment life.
Traditionally, plant maintenance in the food and beverage industry is on a time-based preventative basis. This is like changing the oil in a motor vehicle every six months – whether the change is needed or not. The fixed schedule doesn’t account for actual operating conditions. That means some lightly used equipment is being maintained or replaced more often than needed. While at the same time, some critical heavily-used equipment is being serviced less often than needed. This creates the potential risk of unplanned downtime that can cause lost production and consequently, major financial losses.
With condition monitoring for powertrains, all its components send vital condition and performance data to the cloud. This data is then analyzed and made visible to the plant operator on a simple dashboard that shows availability, environmental conditions, operational variables, and fault events. This real-time health information ensures that maintenance is only carried out when needed.
Powertrain assets that are functioning correctly show up as green; yellow indicates there's something that needs to be checked, while red means that there is something wrong. This increases process reliability as operators can detect any potential equipment issues before they happen – shifting maintenance from reactive to predictive. The ability to monitor remotely also keeps employees safe by limiting exposure to potentially dangerous process equipment such as mixers, grinders, and cutting machines.
Digitalization in Action at Absolut Vodka
A unique aspect of the iconic alcoholic beverage brand Absolut Vodka is that it has a single production line serving the entire world. Process reliability is, therefore, critically important to the company’s very existence.
After researching various methods to implement condition-based monitoring and maintenance, ABB recommended the distillery install its ABB Ability Smart Sensors as the basis for a cost-effective and easy to use condition monitoring solution. The sensors, each about the size of a mobile phone, were installed on motors in the mash preparation process – a continuous function critical to the overall distillery operations.
Soon after the sensors were fitted to the motor housings, an abnormal vibration curve was detected on an agitator motor, indicating possible bearing failure. In-depth analysis confirmed that there was indeed a faulty bearing. Early detection allowed Absolut to fix the problem during a planned shutdown, avoiding lost productivity caused by unexpected downtime.
At the same time, the sensors uncovered a second possible problem – significant vibration in one of the pumps, also on the mash preparation line. At first, engineers thought it might also be a bearing issue, but it turned out to be a valve that had shifted accidentally, resulting in pump cavitation. These two events illustrate how smart sensors can prevent expensive downtime.
Ultimately, all food and beverage plants will need to adopt digitalization to some extent simply to keep pace with the changing nature of the industry. Early adopters in the industry are reaping the rewards and, after taking advantage of low-hanging fruit and establishing a long-term digital strategy, they stand the best chance of success in the future.