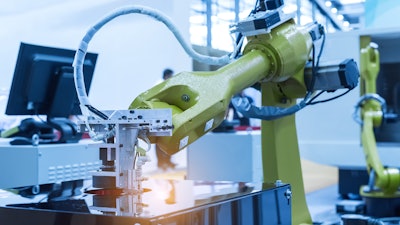
Machine vision is rapidly taking responsibility for inspection, validation and motion control processes. Robots bring the most value to dull, repetitive and mundane tasks like pick-and-place by relieving some of the repetitive strain on the employee. That said, the dexterity and accuracy needed to pick an item out of a bin and place it onto a conveyor cannot be taken for granted — not just any old robot can do this job.
Automating this process becomes challenging when you consider the random assortment of parts in a bin. How can a robot decipher the most logical order to pick these items up in, and what if these items are non-uniform? Bananas and apples are a prime example. CAD data drawings can only go so far in defining a product and in some cases, like pieces of fruit, CAD data simply doesn’t exist.
3D machine vision describes the automatic extraction of information from digital images without the need for CAD data. A typical machine vision environment would be a manufacturing production line where hundreds of products are presented in front of a 3D camera. Using this 3D camera — or several cameras, in some instances — manufacturers can carry out imaging-based automatic analysis and inspection to inform the robot guidance. Essentially, it provides eyes for our traditional robot arm.
Product inspection is a worthwhile application of machine vision systems. By eliminating costly errors in quality, customer satisfaction should rise. Using automation, any deviations and errors in manufacturing are automatically detected and relayed to the proper personnel, so that the necessary actions can take place. This, of course, has huge implications for traceability as each product can be logged as necessary.
One fundamental aspect of traceability in the food industry are Hazard Analysis Critical Control Points (HACCP). By using a vision system to monitor the product quality along the assembly line, preventing food hazards through HACCP is a breeze. The critical limits of each control point can be established and programmed in the vision system. Using this method, any violations such as a stray band aid, can be detected and dealt with automatically.
Machine vision systems come in many different forms to suit the specific application. Let’s take dispensing liquids as another example. Using one or more sensors to take images of the bottles, the position and quality of each bottle is analysed, before the liquid is dispensed accurately and consistently. Some vision systems are even able to use thermal imaging to monitor the temperature of the liquid.
Verification processes can also be delegated to a machine vision system. Consider a bottled water production line as an example. When it comes to capping bottles, there’s a lot that can go wrong. From misaligned lids and broken tamper rings, to missing dust caps. Using machine vision, the camera can instantly detect and recognise these issues as they occur.
The Future of Machine Vision
Machine vision systems are being rapidly adopted across the U.S. The growing market is driven by the rise and popularity of smart cameras, improved ease-of-use and the gradual decline in cost. Human eyes will always have their role in production. Whether they are required to interpret data via a human machine interface (HMI), or assess problems flagged by vision systems.
Jonathan Wilkins is a director at EU Automation, a company that stocks and sells new, used, refurbished and obsolete industrial automation equipment and components.