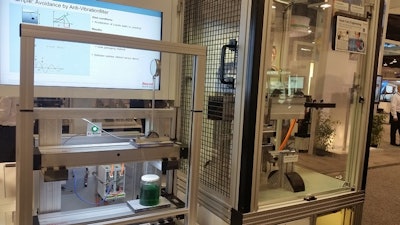
This week, UBM Americas held its six annual co-located shows at the Anaheim Convention center in Anaheim, CA.
For full disclosure, and the simple fact that it was one of few photos I somehow conjured into full focus, I technically attended West Pack, Medical Design & Manufacturing West, PLASTEC West, Design & Manufacturing Pacific, Electronics West, and ATX Automation Technology West over the span of two days (though I should have stayed for a third).
Because the internet, however seemingly infinite, will one day run out of capacity, I’ll spare it a few characters with every post from the show, which I will simply refer to as UBM West 2016 – after all, it was the hashtag of choice for those following the many industry musings on Twitter.
My first of many appointments proved to be the most extensive as I met with Kevin Gingerich, the manager of communications and e-business with the Rexroth Bosch Group, who provided a tour of the booth. Rexroth should be credited with its economical and efficient use of well-positioned space that had a deceivingly large amount of demos per square foot.
Gingerich walked me and IEN Associate Publisher Christina Bear through many of the company’s new tech demos and, while some were familiar from the previous year, many included interesting new motion control-enabling technologies. To view the photos, click through the gallery at the top.
Positioning Flexibility Improves Productivity
The first display was the official U.S. launch of the Bosch ActiveMover, the newest product the company has to offer in conveying technology. With a linear motor base, the transfer system offers more positioning flexibility as well as the ability to quickly cover short distances.
According to the company, the ActiveMover was under development for nearly 15 years, and has the ability to increase process quality and improve productivity, particularly in automotive assembly, medical, and pharmaceutical processing applications.
The most impressive aspect of the demonstration was the ActiveMover’s speed and acceleration, which could lead to shorter production cycles, all while remaining capable of moving up to 10 kg per platform, even in harsh, dusty environments. According to Gingerich, the ability to freely program each individual carrier not only increases flexibility and efficiency, but also improves maintenance and reliability.
Open Mechatronics
The next stop on the tour was Rexroth’s new Open Mechatronics demo that also debuted at Anaheim in 2016.
What exactly is open mechatronics? According to Gingerich, it is technology that allows access to the core programming environment that allows users to develop programs to run machines without any PLC code. Essentially, it gives machine builders flexibility in designing user interactions with the machine.
The demo was built off of Rexroth’s Open Core Engineering (OCE) solution on an L25 controller in conjunction with an Excel spreadsheet to program the motion. According to Gingerich, the motion demonstrates the position of a two-axis Cartesian system with a CKR X axis, an EMC Gen2 and IMS Ball Rail for the Z axis.
During the demo, which admittedly was still working out some bugs on the first day of the show, the runner block is attached to the end of the Z axis, and the program was supposed to showcase its precision by lifting the weight of the larger runner block on and off of a size 65 Ball Rail. Hopefully, the staff was able to get the demo up and running after working out the kinks.
Open Core Interface
To further show off its OCE framework for PLC automation, Rexroth demonstrated how its Open Core Interface allows for high-level programming with enhanced access to the core of the control system, which enables machine builders to create individual functions without the need for additional hardware.
As part of this open mechatronics movement, standard control platforms IndraLogic XLC (PLC), IndraMotion MLC (motion logic), and IndraMotion MTX (CNC) support the direct implementation of individual language programs into the control system.
According to the company, the programs have direct access to the firmware, which allows machine manufacturers to independently create control algorithms for complex functions and kinematics. The programmers do not require any PLC skills and can use standard high-level languages such as C/C++ instead.
Adaptive Systems Technology
Among the more eye-catching displays was an example of Rexroth’s Adaptive Systems technology, which alleviates unwanted movements, such as oscillations, vibrations, sloshing, and sway.
This demo, in particular, focused on controlling vibration and sloshing.
Less vibration reduces dimensional variation and product damage, and it also permits shorter stabilization and transient times to increase machine throughput, according to the company. It also reduces mechanical stress, which can extend machine life.
The Adaptive System handles high-speed inputs and deterministic events with closed-loop response times. According to the company, current closure can be accomplished in 62.5 microseconds, speed loop closure in 125 microseconds, and position closure in 250 microseconds.
The technology uses the IndraMotion MLD drive-based motion logic controller with IndraDrive intelligent servo drives that include sensors to monitor the status of axis mechanics. The company’s Productivity Agent software uses the drive as an intelligent sensor to monitor, analyze, and reduce vibrations in real time.
As for sloshing, the company managed to illustrate its capabilities by firing mysterious green goo back and forth without any spillage, which is encouraging, as it looked like something out of one of the many Joker origin stories in the DC Legend’s mythology. Still, the prospect really caught my attention and, had it not been for the glass barrier and keen awareness of the Rexroth associates outnumbering us three to two, I may have attempted to throw it off-balance.
According to Rexroth, the Adaptive Systems tech is also ideal for controlling slosh. Because the green goo was being controlled by servo drives, the adaptive tech minimized slosh and reduced the requirement for empty reserve space in the container.
Greater stability in the fluid meniscus also allows the use of optical level sensors to provide feedback to further optimize motion control. It also shortens stabilization times and cuts down on the transient time for contents to settle, which means faster filling, sealing, and machine cycle times.
Order Directly through New App
Finally, Gingerich capped off the tour with an update to Rexroth’s GoTo Products App Version 4.5, which now allows users to order directly through the app.
Now, the app is a little tricky as users still have to register and create an account with the company’s eShop, but the new version is pretty seamlessly integrated into the checkout function, which does make it easier for users to sort through new product information, identify favorites, purchase, and schedule delivery.
Thus far, the company has had more than 20,000 app downloads since its launch in 2012, however, Gingerich anticipates an uptick in adoption now that users have the ability to order directly through the app.
Interestingly enough, the Android version of the app is more popular in Europe, and the U.S. leads in Apple-based downloads. What I found most peculiar was that iPad use “slowed considerably,” according to Gingerich. The slowdown may come as a result of increasingly larger screens on smartphones, but as an avid Android supporter, I’m still struck by the fact that Apple leads the U.S.
For more coverage from the eight co-located shows that I will collectively refer to as UBM West, please visit IEN.com, follow @IEN_Now on Twitter, or like us on Facebook, where I encourage you to share photos from the show.