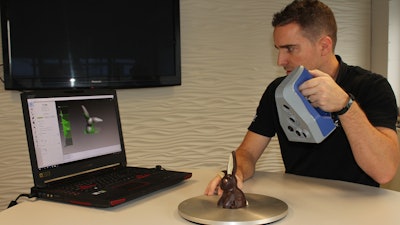
Birthdays, Easter, Christmas – people love their sweets and chocolate, especially when celebrating a special occasion. It's the same for packaging companies that design the wrappings. They know that it’s the most attractive products that fly from the shelves, and now there is an ever-increasing trend for sustainable, custom-made packaging that is easy to create.
To this end, Bachmann Forming AG, part of the Swiss family-owned Bachmann, uses Artec 3D scanners to create the packaging for chocolate rabbits. Just as in the past, the first step is creating a master form, or pilot tool that has an identical shape to the chocolate bunny provided by the manufacturer. Until 10 years ago, most of the original models were handcrafted, manually ground, cast with epoxy resin or milled from wood. The entire process could take up to 20 hours.
In recent years, however, this procedure has changed dramatically with the advent of digitization. Pilot tools are now designed using computer-aided design (CAD) and manufactured from blocks of polyurethane on CNC-controlled milling machines. The block material is easy to process and guarantees a homogeneous surface. Bachmann Forming was looking for a way to digitize hand-made shapes faster and more precisely, which would be especially beneficial for food packaging since food is usually produced without CAD data.
One of the key advantages of Artec’s devices is that, in contrast to other 3D scanners, they do not need adhesive markers to be stuck over the object for the scanner to maintain tracking and to align scans, since the algorithms in the software analyze both the geometry and the color data of the object. By using Artec’s technology to create a CAD model of the original chocolate bunny, Bachmann Forming is now able to take advantage of the expedited process of CNC machining the master form. It also has the added benefit of being less prone to manual error by eliminating hand measurement and machining.
To create the final packaging, Bachmann uses a thermoformal process, during which a plastic film is first heated to soften it. Creating a vacuum, the film is pulled over the master form, which has small holes that help to draw the film in. It sticks to the model and takes on its shape. Then the film is cooled down until it becomes solid - only then can it be peeled off again.
After the manufacturer has delivered the chocolate bunnies, the scanning process begins. This results in several scans from different sides of the object, which are then aligned on the computer. The chocolate's dark color is not a problem when scanning, and manual retouching may be required only for colorless, reflective surfaces.
The data is processed in the Artec Studio software, before being prepared for further reverse engineering in Geomagic Design X. Then the data is exported as a solid (STEP data) or imported directly into the NX (Siemens CAD) via the CAD interface. For visualization, VRML data is created in Artec Studio and then rendered in Cinema 4D (3D graphics software). It took Bachmann one hour to complete this entire process.
Scans are usually processed in the autopilot mode of Artec Studio, which automatically edits the data. The user just has to answer a few simple questions about the characteristics of the scanned object, then Artec Studio deletes any unwanted data, automatically aligns the scans, and chooses the most effective 3D algorithms for the available data. The result is an extremely precise 3D model.
"Before we had Space Spider, this kind of work had to be outsourced, which was very time-consuming and cost-intensive," says Bachmann's Jörg Nussbaum. "The external service provider scanned the chocolate bunny as it was, with all the details, so the 3D model also showed all the bumps that were in the chocolate. Now we can immediately intervene in the data processing stage and delete these parts."
Nussbaum also refers to the time advantage, since scanning at external companies could take up to two weeks. "When we do it ourselves we scan whenever we have time. In the packaging business you have to be fast and innovative. With Artec Space Spider we have found a tool that will help us with many upcoming projects."