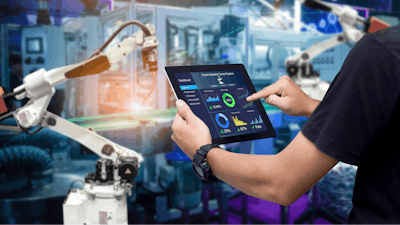
Manufacturing has undergone a seismic transformation in the last decade, driven by technology advancements that are reshaping the landscape. Pillars like Enterprise Resource Planning (ERP) and Customer Relationship Management (CRM) systems are now table stakes, but they only lay the groundwork for what's to come. Todayโs manufacturers are on the edge of a new industrial revolution driven by the collaboration between humans and machines to increase the focus on resilience and sustainability.
While the industry is only starting to reach widespread adoption of Industry 4.0 concepts (machine connectivity, efficiency monitoring, process standardization, etc.), many early implementors of these technologically-advanced systems experienced limitations when faced with situations requiring rapid adaptability and creative engineering. The result is an emerging Industry 5.0 concept that isnโt replacing 4.0, but rather building on it with a human-centric approach to overcome these challenges. To successfully implement Industry 5.0, manufacturers must focus on technology investments, long-term people strategies, and upskilling.
Business System Interconnectivity
Picture this: Itโs the end of a quarter, and youโre preparing a briefing for your investors that outlines company health and future growth potential. To do so, you must compile metrics from a myriad of systems that each measure a different facet of your operation. It takes your team nearly a month to gather, interpret, and visualize the data; meanwhile, your investors are growing impatient with the delays.
Now imagine if all of your internal systems were connected and your data was updated and charted in real-time on dashboards that were visible to your entire management staff. Each department head could then export their own pre-formatted reports and data visualizations for inclusion in the investor summary. Additionally, with AI tools, your leadership could easily and quickly drill down for ad-hoc analysis and testing different โwhat-ifโ scenarios.
This capability is possible today, but as a first step, organizations need to integrate CRM, ERP, project management, and inventory systems. This connectivity empowers manufacturers to operate more efficiently, make data-driven decisions, reduce costs, enhance customer satisfaction, and adapt to evolving market conditions. There are three primary approaches to system integration, and choosing the right one depends on your company's goals and long-term growth strategy.
- The first is leveraging existing connectivity tools and APIs inherent in most modern software platforms. This is usually the most economical integration option, but it requires regular maintenance and monitoring to ensure continuous operation.
- The second way is to combine your current systems into one platform that meets the end-to-end needs of your business. While this can be costly upfront, the immediate efficiency gains and cost savings through platform reduction result in a faster ROI.
- The third is a hybrid approach involving investments in some new technologies in conjunction with system integrations. For example, you may want a new CRM platform but donโt need a full ERP refresh. This hybrid option is a great way to weed out platforms that no longer meet your needs while maintaining continuity in your operations.
Task & Process Automation
As workforce shortages continue to grow throughout the industrial sector, manufacturers and distributors alike are finding new ways to combat the challenge. For many, investing in robotic process automation (RPA) is the go-to solution for any rule-based task or activity. In its broadest sense, RPA uses a pre-programmed robot or โbotโ to complete process workflows, including reconciling invoices, monitoring inventory levels, tracking shipments, and even making data-driven decisions to optimize procurement.
The concept of smart manufacturing leverages AI in conjunction with RPA to create data-driven production environments. By integrating IoT technologies with AI, manufacturers can monitor every aspect of the production process in real-time and use machine learning to prevent downtime and improve product quality. Industry 5.0 takes this idea one step further by engaging the human element to engineer rapid production adjustments and create logic-based plans for research and development initiatives.
Developing a Tech-Based People Strategy
Integrating technology with your people strategy requires alignment of your organization's technological capabilities with your workforce goals to improve efficiency, productivity, and employee satisfaction. Conducting a thorough stakeholder analysis and implementing RACI (Responsible, Accountable, Consulted, and Informed) adjustments becomes essential in recognizing the diverse impacts on various departments, from the shop floor to finance.
Be sure to identify obstacles and assess the stakeholders impacted by impending changes. This process may necessitate an organizational redesign and retraining, or upskilling of employees, especially as they shift from operating heavy machinery to managing robots.
The Urgency of Upskilling
To ensure a successful transition into Industry 5.0, you will need to establish an effective upskilling program. Upskilling involves a two-fold approach encompassing capabilities and skills:
- Develop programs that prepare your workforce for immediate performance needs and long-term objectives.
- Strive for synergy between people and technology. When they work together harmoniously, organizations avoid margin pressure caused by employees circumventing technology. The workforce should view technology as an ally rather than a hindrance.
Manufacturers must adapt not only to remain competitive, but also to attract and retain talent. The incoming workforce is accustomed to advanced technology in their personal lives and work lives. AI and automation can play vital roles in filling knowledge gaps, enhancing workforce capabilities, and making manufacturing jobs more desirable to the next generation of the workforce.
Change is a universal challenge when implementing new systems, technologies, and processes, especially in organizations where employees have relied on established processes for decades. Change management strategies, including training, transparency, and consultation, are essential to mitigate disruption and ensure a successful transition.
Manufacturers who see technology and people strategies as cohesive allies stand to benefit from enhanced resource management, streamlined production processes, and improved customer relations. The future of manufacturing lies in the hands of those who harness the power of technology to drive innovation. As Industry 5.0 continues to evolve, the manufacturing sector is poised for a future marked by greater growth and productivity.