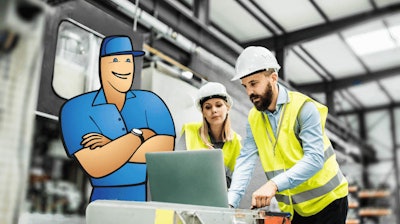
The Master Production Schedule (MPS) is a production planning tool that outlines which products need to be manufactured, in which quantity, and when. A master production schedule does not go into detail regarding the production operations, sequencing, employees assigned to tasks, etc. Rather, it is like a contract between the sales department and the manufacturing department that balances supply and demand by defining the necessary quantities to produce within specific timeframes.
A standard master production schedule is a long-term plan made for each product separately. It is done with a planning horizon of a few months to several years, with a minimum time bucket (smallest timeframe specified) of 1 week.
Benefits of a Master Production Schedule
There’s an array of benefits to introducing an MPS to a manufacturing business:
- Provides a solid base for building, improving, and tracking the sales forecast.
- Helps determine and achieve the desired inventory levels, thereby avoiding shortages and overstocking.
- Enables companies to calculate the quantities of parts, subcomponents, or raw materials to purchase or produce, as part of Material Requirements Planning.
- Enables the calculation of the required amount of labor and shifts many months in advance.
- Allows for capacity optimization and balancing the load of the plant in advance, enabling companies to avoid bottlenecks.
- MPS can be used to estimate production and maintenance costs associated with the work centers.
- It can help derive expected revenues and expenses and generate a cash flow forecast.
- MPS can be used to anticipate labor requirements.
- Accurate MPS planning and execution can significantly improve customer satisfaction by ensuring the timely fulfillment of orders.
- The MPS defines visible, clear, and measurable objectives and a plan to achieve them.
Inputs of a Master Production Schedule
The basic inputs you need to create a viable master production schedule are:
1. Starting inventory. How many units of the SKU are already available in stock?
2. Sales forecast / demand plan. How many orders are expected for the period?
3. Current order portfolio. How many orders are already planned?
4. Quantity to produce. How many units need to be produced to balance supply and demand?
Download a free master production schedule template.
6 Tips for Managing a Master Production Schedule
Mastering the Master Production Schedule is vital for efficient production planning and optimized manufacturing processes. Here are six key tips to help manage an MPS effectively:
1. Balance demand and supply. An effective MPS balances customer demand with production capacity. While it's crucial to meet customer orders on time, overloading your production line can lead to increased costs and inefficiencies. On the other hand, underutilizing capacity can lead to lost sales and reduced profitability.
2. Align MPS with business goals. Your MPS should align with your overall business objectives. If your goal is to reduce inventory holding costs, for instance, your MPS should be designed to produce just in time to meet demand. If your goal is high service levels, your MPS might need to include safety stock or be geared towards fast response times.
3. Regularly review and update. In the ever-changing landscape of supply and demand, a static MPS can quickly become outdated. Regularly review and adjust your MPS based on real-time sales data, customer orders, inventory levels, and supply chain conditions to ensure its accuracy and effectiveness.
4. Collaborate across departments. An MPS impacts multiple departments in a company, from production to sales to procurement. Ensure that all relevant parties are involved in its creation and review. This collaborative approach can improve forecast accuracy, resource allocation, and overall effectiveness of the MPS.
5. Use appropriate technology. Utilize a manufacturing ERP system, such as MRPeasy, that can automate much of the MPS and manufacturing planning process. These systems can provide real-time data, helping to streamline the process, reduce errors, and improve responsiveness to changes in demand or supply.
6. Track metrics and improve continuously. There are many KPIs you can keep an eye on to assess the accuracy and usefulness of an MPS. These include schedule adherence and attainment, inventory levels, capacity utilization rate, OTIF, etc. Measuring your MPS performance and comparing against historical data allows you to understand when some aspect of the planning process needs to be improved.
Read the full Master Production Schedule Guide at https://www.mrpeasy.com/blog/what-is-master-production-schedule/