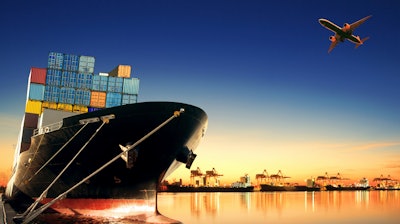
When they operate smoothly, supply chains are the invisible plumbing that makes global commerce tick. For millennia, economies have depended on the flow of goods and materials around the world by sea and land, with air having been introduced to the mix about 100 years ago. And yet, with all of the technological advancements of recent generations, one key issue that continues to plague supply chain management is the relative invisibility of in-transit shipping containers.
Without continuous modes of communication, which can be taxing on resources and prohibitively disruptive to air traffic data flow, companies rely on checking in on their shipments at predetermined intervals to track progress and ensure safe conditions.
The problem is that these intervals cannot account for unexpected damages occurring. This approach to tracking is out of touch with the modern realities of the supply chain.
The statistics don't make for pretty reading. The early months of 2021 witnessed more shipping containers lost at sea than all of 2020. Between 2008 and 2019, an average of 1,382 containers were lost at sea every year. Visibility allows companies to mitigate product losses, increase bottom lines, and ensure product integrity on delivery.
However, improving visibility is easier said than done.
Obstacles Preventing Visibility
Supply chain industry experts have been promoting data analytics as a magic bullet solution to improve in-transit container tracking. Analytics packages have the potential to spot potential issues before they occur. However, they rely on data, and this is where obstacles arise.
Traditional tracking technology relies on Radio Frequency Identification (RFID) tags. These tags can be unreliable in areas where radio waves tend to get knocked around. A container ship at sea isn't the best place for radio waves, and therefore, companies struggle to collect relevant data.
In addition to unreliability, there's also the ease of use to consider. RFID requires dedicated infrastructure in the form of tag readers and software to collect data. It's an expensive system to install, and employees need training to use tag readers. As a result, the number of people equipped to capture data is low, and companies have to invest significant resources into what should be a relatively simple task.
There are other solutions, such as USB tag readers and Bluetooth sensors. However, USB readers require special software and can get knocked out in rough conditions. Bluetooth is viable only within a certain range. As a result, it's impractical for long-distance shipment tracking.
Currently, RFID is the least-worst solution that companies have opted for, and they've learned to live with its limitations. However, several exciting new solutions promise to change the way manufacturers and other supply chain companies can track their in-transit goods.
New Solutions
These days, consumers insist on knowing the source of the products they buy. RFID, with its relative inaccessibility, cannot create a transparent supply chain. Finnish logistics solutions provider Logmore has developed a product that eliminates this issue.
Logmore designs sensors that monitor the condition of the goods they're attached to, whether it's temperature, vibration, shock, or light. These data are encoded onto a dynamic QR code displayed on an e-ink screen attached to the shipment or container.
Thereby, logistics employees can scan these codes using their smartphones and transmit data to an analytics platform on the cloud via Logmore's app. The solution meets the latest GDP and CFR data privacy requirements and offers companies a simple and cost-effective way to monitor their goods in transit.
Crucially, it establishes a clear audit trail that can be shared with consumers easily. Teams can define condition-related thresholds on their software and instantly receive alerts if they're violated. Thus, risk mitigation becomes simpler.
While Logmore's system attaches itself to any scale of shipments, down to the individual package, Traxens adopts a macro approach by transforming the shipping container itself into a data monitoring hub. Using their smart container, shippers can receive complete door-to-door visibility and keep track of every condition affecting their shipments.
Sensors attached to the container monitor GPS positions, door openings, shocks, container positions, and light. The containers are durable and can withstand the rigors of international shipping easily. Like Logmore, Traxens offers its clients access to an analytics platform where they can specify condition-related thresholds and receive alerts upon violation.
While tracking a shipment is of the utmost importance to manufacturers and shippers, traceability and sustainability are a close second. Tracing the origin of products has been an issue in the past due to a lack of integration between delivery systems.
Supply chains are complex, and many companies have a hand in shipping a product from one part of the globe to another. Therefore, data is siloed into different systems. The result is that manufacturers have to vet their suppliers carefully and hope none of them violate sourcing guidelines.
This problem is quickly disappearing thanks to the blockchain. OriginTrail is a blockchain-based protocol that seeks to bring disparate supply chain systems together onto a single platform. Thanks to the blockchain's immutability, data is always secure and validated.
“By performing consensus checks in each step of the supply chain we are effectively creating a single version of truth and supply chains with integrity,” says Tomaz Levak, Founder and Managing Director of OriginTrail. “Such end-to-end visibility can, in turn, be used to overcome not only data fragmentation but can support various other use cases.”
The result is a transparent audit trail that lets manufacturers and consumers know where their products have come from and how they were produced. Consumers can scan a tag or code on the product and instantly receive a supply chain history.
An Exciting Future
Supply chains face bigger problems than in-transit container visibility, but this is a problem that shouldn't exist these days. The technologies and companies profiled are eliminating this issue and bringing greater sustainability and visibility to the supply chain.
The result is happier consumers and better bottom lines for all parties in the supply chain.