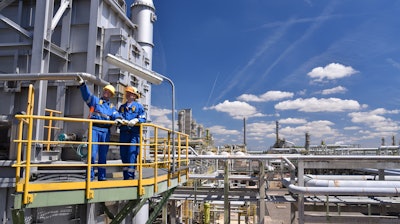
With the regulatory complexities and sustainability goals increasing over the years, environment, health and safety (EHS) teams are recognizing the importance of getting on board with digital transformation for accurate environmental compliance. As one of the earliest adopters of digital technology in EHS, the manufacturing industry, 95% of leaders believe it's essential to their company's future success. But for many manufacturers, where does EHS and environmental compliance fit into their digital transformation equation?
Using digital tools to provide structure and ensure success for complex regulatory problems isn't a luxury but a necessity. Automation and efficient digital tools help businesses establish a single source of truth for compliance data, making it more visible and easier to track across the entire operations. By making processes automated and accurate, it helps avoid non-compliance risks such as fines and public scrutiny. It's become equally important for EHS leaders to consider how digital strategy positively impacts environmental compliance processes and outcomes.
The more pressing question — “How do we start?” — often lacks a clear-cut answer. The process tends to be easier if an organization already has an existing digital foundation for other business functions, although integrating digital technologies for EHS and compliance operations can be a puzzle.
Here are five steps to environmental digital transformation EHS professionals can adapt to give structure and lead to success.
1. Establish a compliance foundation
The first step toward environmental digital transformation is to establish a strong foundation for compliance data, since centralizing data significantly improves how compliance information is managed and accessed. EHS operations can build foundations for specific compliance program areas, such as hazardous chemicals (storage and use), or hazardous waste (disposal).
Organizations should have a single point of control and visibility for corporate, facility and personnel information required for compliance reporting. Consolidating this information via cloud-based software and creating a solid foundation for compliance data decreases the risk of reporting errors, such as inaccuracies and incompleteness, and creates a single source of truth to:
- Maintain corporate information
- Build out facility profiles
- Track and update facility contacts
Because an organization controls this information centrally, they’re able to push it to all relevant regulatory databases at the state or federal level for compliance reporting. The digitized system serves as the compliance foundation for any particular program area.
2. Establish a continuous data collection process
Once an organization creates a strong foundation for environmental compliance data, it should set up data pipelines. These pipelines may take a few forms:
- Direct data uploads
- Digital questionnaires for compliance stakeholders
- Available integrations to existing data systems
Establishing a continuous data monitoring and collection process facilitates the systematic collection of all relevant compliance data for each program area. The result is greater data visibility and control as data is gathered and validated. When data collection functions are automated, they’re conducted with less effort and fewer errors. More than 60% of operations professionals cite automation as key in reducing data errors.
Compliance programs are also more successful when they track and manage data continuously across all four reporting lifecycle stages: collection, validation, input, and submissions. Companies and their EHS operations should set up daily, weekly or monthly cadences as appropriate for maximum benefit.
3. Automate updates and notifications
Outdated or incorrect facility contact information is among the most common errors in environmental compliance reporting. Actions such as changing corporate mailing information, exceeding regulatory thresholds based on site data, and updating when (or if) EPA regulations apply to specific sites often trigger notifications. Once an organization builds a strong data foundation and ensures continuous data collection, the next step is to automate updates and notifications to keep facilities compliant.
Facility information constantly changes from a corporate, personnel or regulatory perspective — like outdated emergency contacts at the facility level. Suppose an emergency contact for a regulated facility leaves an organization. An automated process could trigger an alert that an update is needed in a timely manner, reducing the number of propagated errors for compliance reporting. Automation also frees employees from taking multiple steps to update information and reduces the possibility of human error.
4. Automate compliance reporting
As they near the end of their reporting cycle, organizations must track multiple deadlines for report compilation tasks and final submissions. The next and most crucial step toward environmental digital transformation is filing compliance reports. Automating report submissions enables EHS and compliance professionals to transmit compliance information accurately to the right agencies, in the right format, at the right time.
Finding, reporting, documenting and correcting errors drains time and resources. Using a cloud-based platform to automate the process expedites mitigation, helps EHS teams catch errors before they escalate, and frees employees to focus on more critical tasks to drive operational efficiency.
5. Unify compliance programs
The ultimate goal of a digital transformation is to unify an organization’s operations and processes as a whole. As an early adopter of digital transformation technologies and practices, the manufacturing sector has been a leading example of this. Environmental digital transformation follows the same path toward unifying the organization’s compliance program areas.
After implementing environmental digital transformation for a specific program area, a company can expand into other program areas to lay those foundations. This approach empowers enterprises and compliance teams to transform their environmental compliance program across different areas into an auditable and continuous process. More importantly, this method ensures accuracy and mitigates non-compliance risk throughout the entire compliance data management process.
Unifying program areas is an incremental approach to a full environmental digital transformation. Over time, EHS and compliance operations begin to consistently use digital tools such as automation to complete a majority of their work. Processes for managing data and reporting can effectively be standardized, made repeatable, and fine-tuned with consistent usage.
Efficiency, trust, and much lower non-compliance risk
Through this transformation, corporate leaders and EHS teams alike can have faith in knowing processes and protocols are operating as needed to maintain compliance. EHS professionals also have more time to focus on other critical initiatives, like reducing their carbon footprint and ESG.
As something many organizations in the manufacturing industry already know quite well, rolling out a digital transformation requires thoughtful, deliberate planning. Extending this same kind of planning to EHS and compliance operations is now their next step — for several reasons.
When an organization's aim is to ensure environmental compliance, spending hundreds of hours tracking down compliance data in siloed and disorganized systems is an inefficient use of environmental professionals’ time. Nor should a business ever have to guess if or when compliance reports are required for specific facilities. And corporate leaders should never have to question if their business is in compliance or at risk of being penalized for non-compliance violations.
Taking five well-thought steps to environmental digital transformation creates more efficient, accurate processes for achieving consistent environmental compliance.