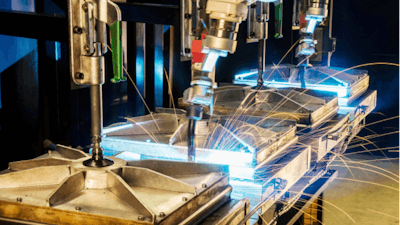
Nearly all manufacturing equipment today comes equipped with sensors and control systems that track use and status, such as the number of cycles or parts produced, operating temperature and power consumption. Most of these monitoring and control systems focus on single-asset use, and may even require a plant manager to physically observe the condition of each machine by walking around and checking displays.
While these existing systems do improve insight into a machine’s state, they are unable to incorporate additional sources of information to provide context. Furthermore, they lack the ability to recognize patterns that indicate changes in the machine’s health before a breakdown occurs. As a result, machines are still prone to unforeseen failures that can shut down production and the associated revenue.
The Industrial Internet of Things (IIoT) can help. An IIoT system can give manufacturers operational insights to avoid expensive unplanned downtime by aggregating real-time data from all similar equipment and adding context from other sources such as repair histories, environmental conditions, and machine specifications.
IIoT’s predictive analytics capabilities can alert manufacturers of changes in a machine’s state that indicate an impending problem, so they can take steps to correct the issue before it escalates. Machine operation can even be automatically slowed to allow production to proceed while plant managers arrange for repairs to take place at a time that’s the least disruptive to production.
Similarly, the system can monitor equipment conditions and employ rules dictating which conditions are within acceptable limits, and which are outside those limits. For example, applying rules for the heat limit on a cutting blade means that when the temperature rises above that threshold, the system can deduce that the blade is nearing the end of its useful life and alert the plant manager to change the blade before a failure stops production.
Often, maintenance and repair needs aren’t the result of a single issue or change in condition, but more likely the outcome of a combination of factors that may not all occur at the same time.
So rather than performing maintenance on a set schedule, the system can track multiple complex variables and look for patterns over a period of time that point to the need for maintenance. This condition-based maintenance is more cost-effective – since equipment is serviced only when it really needs it – and can drastically lower the incidence of unplanned downtime. It can also extend the equipment’s useful life.
Some of this same logic can enable other beneficial operational capabilities, such as real-time equipment optimization. By comparing one machine’s performance to others like it, and utilizing the optimal configurations from the best-performing machine, the system can automatically adjust settings or configurations to bring the lower-performing equipment up to par. The result is improved productivity, efficiency, and quality.
Today’s manufacturing equipment can be very complicated, with multiple systems and subsystems that work together. IIoT uses complex logic to gain insight into these intricate machines, accessing multiple different data points and external systems in an automated fashion, reasoning over them, and determining patterns. And by building up a library of all those data points and patterns, the system is able to scale across the enterprise.
Often, manufacturers begin with a small IIoT proof-of-concept that focuses on a single machine or narrowly focused business outcome. Generally, these deployments run into trouble when they attempt to scale out across an entire production line or multiple locations.
Incorporating the right subject matter expertise and input is crucial during the system design process and for defining and refining rules, but successful expansion requires much broader cooperation and coordination. Likewise, the technical demands of monitoring 10 devices differ greatly from monitoring 100,000, so the proper technology – as well as the corresponding implementation and management expertise – are key to avoiding performance bottlenecks as an IIoT system grows.
That’s why it is important to look at IIoT as a maturity progression that starts with connected equipment, and gradually develops to include numerous aspects of the business – not just a few machines or production lines. Trusted partners, IT, and operations personnel must all work closely together, with support from management, to undertake the changes required for IIoT success.
New methods of performing analytics, creating digital models of equipment, and machine learning are enabling the extraction of valuable insights from the massive storehouses of data available throughout the manufacturing enterprise. The resulting operational benefits – previously only attainable through the work of legions of data scientists or large capital investments – are now within the reach of nearly every company.
Dave McCarthy is a leading authority on industrial IoT. As senior director of products at Bsquare Corporation, he advises Fortune 1000 customers on how to integrate device and sensor data with their enterprise systems to improve business outcomes.