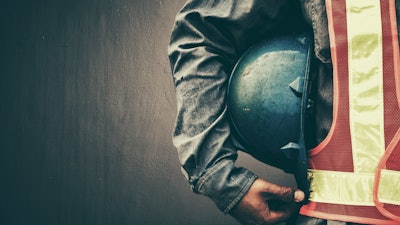
Maintaining workplace safety is one of the most important things you can do as a facility manager. But from time to time accidents do happen.
In some cases, the cause is obvious and plans can be put in place to prevent future accidents.
In other cases, the cause isn’t as apparent. What if we change our thinking and instead of using all of our resources reacting to an accident, we direct those resources to preventing accidents?
We may not be able to predict when accidents are going to happen, but we can certainly start by putting into place prevention programs that will keep people and facilities safe. Here are four ways we can prevent injuries at facilities.
1. Standard Operating Procedures
Each maintenance activity should have its own standing operating procedure (SOP). There should be a clear way for each technician to perform the tasks at hand. Leaving it up to each person to decide how to perform the task creates room for error.
Start by developing a SOP and associating each with a specific asset or task. This step along will improve safety at your facility.
A safety program ensures that every work order issued by a Computerized Maintenance Management System (CMMS) describes the necessary safety precautions that workers must take.
Clearly stated operating procedures also help to increase productivity because they minimize uncertainty and create better workflow.
2. Create a Preventive Maintenance Calendar
Rather than allowing machines to break down and increasing the chance of an accident, create a preventative maintenance calendar to schedule basic equipment maintenance tasks, such as checking belts, checking and changing fluids and oiling bearings.
Use trial and error to determine the tasks that should be added to the calendar. For example, if a piece of equipment fails, the diagnosis may show that a simple preventive maintenance task performed at regular intervals is required to prevent the failure from occurring again.
Routine maintenance extends the life of equipment. By developing a detailed list of preventive maintenance program procedures, you can standardize the operation and maintenance of equipment across your organization and cut costs.
Standardizing the processes used to inspect, repair and maintain equipment is crucial to ensuring a low risk of injury and uniform maintenance work, regardless of who completes the task.
3. Prioritize Maintenance Work with EAM/CMMS Software
Use priority codes in your CMMS to prioritize work and alert maintenance technicians about health and safety concerns related to equipment. Maintenance software allows you to flag assets based on their criticality from a safety perspective.
You can also use your CMMS to identify equipment maintenance jobs that are risky. Safety priority codes give maintenance technicians full knowledge of the safety risks associated with various maintenance tasks.
Making safety a priority in your maintenance department can go a long way toward promoting productivity and mitigating the risk of injury. Empower your workforce with the tools they need to efficiently maintain equipment in the field with EAM/CMMS software.
Effective equipment maintenance with the help of maintenance software will keep your assets running optimally, reduce maintenance costs, streamline processes and protect employees.
4. Detailed Record Keeping
By keeping detailed records, companies protect themselves in the event of random inspections by regulatory agencies. For example, the Occupational Safety and Health Administration (OSHA) enforces standards to ensure safe and healthy working conditions.
OSHA professionals perform site visits and audits, random at times and may request specific documentation on assets. Maintenance management software helps companies meet OSHA requirements.
If OSHA auditors pay an unexpected visit, maintenance managers can generate timely reports sorted by maintenance technician, asset, safety standard, etc.
CMMS software provides the backup documentation required to prove to an OSHA auditor that a safety task was performed on schedule and any incidents that may have occurred were not due to negligence.
A CMMS program also gives users quick access to incident data logs and generates reports showing which safety-related tasks were completed over time and what steps have been taken to prevent future injuries.
CMMS/EAM software demonstrates compliance and helps reduce the risk of any potential penalties and fines.
---
Alex Williams is the Director of Sales and Professional Services at DPSI, an industry-leading provider of computerized maintenance management systems (CMMS) and enterprise asset management (EAM) software.