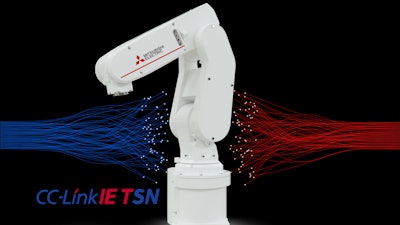
The rate of implementation of robotic solutions is continuing to experience rapid growth, with the number of installations more than doubling since 2015. The American market has shown a strong inclination towards adopting robotic systems in various industrial settings, witnessing the adoption of nearly 35,000 new units across the U.S. in 2021 alone.
Robots have been typically installed as independent, stand-alone automated systems, whose connectivity has been traditionally limited to their controllers and vision systems. Only in a few instances they have been linked to the other components within a designated work cell. However, the evolving landscape of the manufacturing industry has given rise to demands for more ambitious, highly interconnected frameworks in line with Industry 4.0 principles.
To be effective, these advanced automated setups require a high level of integration and data sharing, involving all the automation components and sensors within a robotic cell. Going further, different machines and units, higher-level control system and users should be able to interact with each other. The ability to share data across cells, shop floors and within the entire enterprise is pivotal in supporting digital manufacturing applications, offering a competitive advantage by enhancing decision making, flexibility, reliability and responsiveness.
In order to support digital transformation projects of this nature, it is crucial to establish seamless communications that connect all the relevant elements and enable key insights to be gathered. This, in turn, facilitates the coordination of activities aimed at enhancing overall operational efficiency. The implementation of a robust network infrastructure that supports TSN standards can unlock these benefits as it ensures reliable, deterministic transmission of various types of data traffic.
A network technology with TSN functions, such as CC-Link IE TSN, has the ability to handle time-critical messages related to automated components within the robotic cell, while simultaneously managing less transient TCP/IP packets, including video streams from cameras to support advanced vision systems, for example. As a result, it is possible to integrate robots with other elements within the same machine as well as support inter-unit communications across the manufacturing line.
In addition to improving rapid decision making to create more flexible, reliable and responsive processes, the use of CC-Link IE TSN to create deterministic, convergent networks can improve diagnostics, troubleshooting and even predictive maintenance. In effect, it is possible to analyze a wider range of data to get a more comprehensive insight on what is happening on the shop floor in real-time.
Machine builders and end users interested in developing advanced, data-driven robotized systems can leverage Mitsubishi Electric’s industrial robots equipped with CC-Link IE TSN compatible controllers. By installing these components, they can take advantage of state-of-the-art industrial automation solutions that can drive productivity and competitiveness.