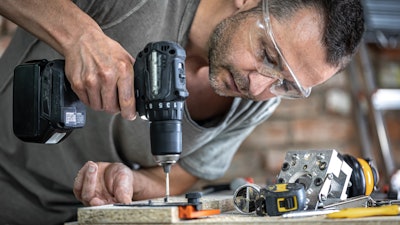
The power tool market is growing, with a compound annual growth rate of more than 6%. The fastest-growing product sector is cordless power tools, representing about half of all power tool shipments. The market growth is spurring the introduction of new technology into the products.
The cordless power tool industry is transitioning to lithium-ion batteries to obtain the advantages of higher power density and longer discharge cycles. Furthermore, the industry is taking advantage of improved reliability, greater longevity, smaller size and improved output performance from brushless DC motors.
While lithium-based batteries provide more power in a smaller package and longer battery life, these batteries challenge designers to ensure battery safety. Brushless DC motors challenge designers to drive the motor more efficiently.
This article provides recommendations to assist cordless power tool designers make their product designs more robust and efficient. The article includes recommended components for protecting the power tool's battery pack, the power tool itself, and its battery charger. In addition, designers will receive recommendations for improving the efficiency of the power tool and the battery charger.
Ensuring a robust cordless tool battery pack
A cordless tool battery pack includes the battery pack, battery management circuitry, and protection circuitry to ensure safe operation. Figure 1 illustrates an example battery pack. Surrounding the battery pack are the function blocks performed by the battery pack and the recommended protection components for each function.
Figure 1. A battery pack and its function blocks.Littlefuse
Figure 2 shows a block diagram of the battery pack circuitry. The adjacent table lists the protection and sensing components recommended for each circuit. The recommended components include protection from both temperature and electrical hazards.
Figure 2. Battery pack circuit block diagram.Littlefuse
Li-Ion Cells Thermal Protection Circuit [1]
Lithium batteries, while providing high energy density capacity, can overheat if damaged. Left unchecked, an overheated Lithium battery can erupt in flames. To prevent this failure mode, use a temperature sensor-based monitoring circuit and a temperature-controlled switch to disconnect the battery from the load.
A thermistor, a negative temperature coefficient sensor, can quickly detect a temperature rise with a thermal response of 10 s. With nominal room temperature resistances from 100 Ξ© to 100 kΞ©, the sensor can adapt to a wide range of detection circuit designs. Look for minimal-sized thermistors, such as those with diameters under 0.1 inch, to enable fast thermal response. Also, look for an epoxy coating for high reliability.
Consider a device that directly disconnects the cell from the power tool circuitry to protect individual battery cells. Use a thermal cut-off device, such as one that contains a parallel combination of a bimetal switch with a polymeric positive temperature coefficient (PPTC) device.
Secondary Protection Circuit [2]
In the Secondary Protection circuit, a backup for the Primary Protection circuit, a three-terminal Lithium-ion battery protector (see Figure 4), can provide both battery overcharge and overcurrent protection. The three-terminal component includes a distributed embedded fuse and heater elements. The fuse element interrupts an overcurrent condition; additionally, if the monitoring circuitry detects lithium-ion battery parameters outside the designated range, the heater element will cause the fuse to blow.
As a simpler alternative, a high-current fuse provides overcurrent protection. Save space with a surface mount fuse model and simplify compliance requirements with a UL/CSA-recognized component.
Battery Management, Cell Balancing Circuit [3]
Protect the Battery Management, Cell Balancing Unit from overcurrent and electrostatic discharge (ESD). This circuit ensures that all cells individually supply an equal portion of the load current. Protect this circuit from a current overload with either an inrush withstand fuse or a polymer positive temperature coefficient (PPTC) resettable fuse. Either component is available in surface mount packaging for PC board (PCB) space-saving.
A transient voltage suppressor (TVS) diode is an excellent component for ESD protection of semiconductor components such as those in the Battery Management circuit. Versions of TVS diodes can safely absorb ESD strikes as high as 30 kV from direct contact or through the air with sub-nanosecond response times.
Primary Protection Circuit [4]
The Primary Protection circuit interfaces directly with the battery pack and protects the battery pack from overvoltage, under-voltage, overcurrent, under-temperature, and overtemperature. A problem with the charging process can cause these conditions. A TVS diode can prevent damage to the semiconductors in this circuit. As well as providing ESD protection to 30 kV, TVS diodes can safely absorb 200 W of a transient pulse. A surface mount model can save PCB space. Figure 5 shows bidirectional and uni-directional models of TVS diodes.
Figure 5. Schematic diagrams of two types of TVS diodes .Littlefuse
ID Pin
The ID Pin circuit ensures that the power tool battery pack can only connect to the proper charger for safe charging of the battery pack. Consider a PPTC resettable fuse to protect the circuit from a current overload and a TVS diode for ESD protection. Look for a TVS diode with two diodes in an anode-to-anode series connection (Figure 6) for bipolar protection.
Figure 6. TVS diode array with diodes connected anode-to-anode.Littlefuse
Switch Circuit [5]
The Switch circuit helps to indicate the status of the charge on the battery. Consider a sealed switch with at least an IP67 rating against moisture and dust ingress. Microminiature switches are available to conserve PCB space. Look for a long life, with a minimum of 100,000 operating cycles. Also, look for a switch with repeatable haptic performance and a short activation distance. All these characteristics enable a reliable switch.
The components presented in the individual circuits will provide protection from hazardous thermal and electrical states. One major element of a cordless power tool, the battery pack, is now more robust and reliable.
Designing a More Robust a Cordless Power Tool with Optimum Efficiency
To design a reliable power tool, designers must provide protection mechanisms from electrical hazards and ensure maximum battery life so that the portable power tool can operate through a work shift. Figure 7 illustrates a professional-grade cordless power tool and lists the components needed to protect the tool from current overloads, transient overvoltage, and overtemperature. Furthermore, the power drive circuit has opportunities to optimize the design for efficiency.
Figure 7. Example cordless power drill.Littlefuse
Figure 8 shows a block diagram of brushless DC motor circuitry in a cordless electric drill. The brushless DC motor drives the drill bit. The table on the right lists recommended protection, sensing, and high-efficiency control components for use in specific circuits.
Figure 8. Brushless DC motor circuit block diagram.Littlefuse
DC Input Protection and Battery Communication Circuit [1]
The DC Input Protection and Battery Communication circuit provides overcurrent and overvoltage protection for the brushless DC motor circuitry. The circuit also energizes and de-energizes the motor. Provide overcurrent protection with a fuse. Consider using a:
- A fast-acting fuse
- A fuse that can operate at temperatures up to 150Β° C
- A surface mount fuse package to minimize PCB space.
For overvoltage protection, use a TVS diode. Consider a TVS diode that can absorb as much as 400 W of peak power.
Power Bridge Protection Circuit [2]
The Power Bridge Protection circuit block monitors the health of the motor drive circuit. Use an NTC thermistor, such as the one recommended for monitoring battery temperature, to monitor the temperature of the MOSFET driving the motor.
Consider a safety disconnect to reduce the MOSFETβs current drive if its temperature rises too high. Littelfuse has a unique component, the setPβ’, whose resistance increases by six decades when a temperature threshold is exceeded. Figure 9 shows the characteristic of a setP digital temperature indicator. The high resistance change can trigger a control circuit to remove power from the MOSFET, preventing MOSFET thermal runaway. The setP device is integrated into a signal line.
Figure 9. The resistance vs. temperature characteristic of a setP temperature indicator.Littlefuse
NTC Temperature Measurement Sensor 4]
Monitoring the motor is essential for ensuring a reliable power tool. Use an NTC thermistor to monitor motor temperature and avoid excessive motor temperature due to an internal short or stalled motor. Surface mount NTC thermistors can mount on the motor using wire bonding, epoxy, or solder.
With the cordless tool protected from overcurrent, overvoltage, and overtemperature, the designer can concentrate on maximizing the tool's efficiency. Two circuit blocks offer opportunities to minimize energy consumption.
DC Input Protection Circuit [1]
Use a reed switch to detect the state of the battery connection to ensure that the battery can energize the power tool circuitry. Look for a small reed switch with low contact resistance under 120 mΞ© for minimum energy consumption. Select a robust switch that can switch up to 0.5 A at up to 10 W of power.
Power Bridge and Gate Driver Circuit [3]
The Power Bridge and Gate Driver circuit uses a high-power MOSFET in the DC-DC converter circuit to allow high-power switching for maximum efficiency and minimum energy consumption. MOSFETs can supply current up to 600 A with RDS(On) values well under 100 mΞ©. Low gate-source capacitance below 100 nC and switching times in the 10βs of nanoseconds enable high efficiency, high-frequency DC-DC converter operation.
Two significant cordless power tool design elements are now more robust and efficient. The third major element, the power tool charger, requires design consideration for circuit protection and high efficiency.
Protection and efficient design for the Power Tool Charger
Figure 10 illustrates a power tool battery charger. The function blocks list components that make the circuitry robust to electrical and thermal hazards and optimize the circuitry for efficient operation. Figure 11 details the block diagram and indicates the recommended components for each circuit.
Figure 10. Example power tool charger.Littlefuse
Figure 11. Power tool charger block diagram.Littlefuse
AC Input Primary Protection Circuit [1]
The AC Input Primary Protection circuit interfaces with the AC line and is subject to high current capacity in the event of an overcurrent condition and voltage transients induced in the power line from environmental conditions such as lightning and large motors turning on and off. Use a fast-acting fuse for overcurrent protection. Ensure the fuse has an interrupting capacity of at least a kiloamp level at 125 VAC. Safely absorb overvoltage transients with a metal oxide varistor (MOV). MOVs can safely absorb a current surge from a voltage transient of at least 6 kA with power levels up to 480 J. Select UL and IEC-certified fuse and MOV components to make the product approval process an easier task.
Rectification, High-Frequency Converter, PFC Circuit [2]
Protect the Rectification, High-Frequency DC-DC Converter, and PFC Circuit from portions of transient waveforms that get through the AC Input Primary Protection circuit with a TVS diode. Consider using a TVS diode that can absorb as much as 600 W of pulse power. In addition, verify that the diode provides 30 kV of ESD protection.
Output DC Protection Circuit [4]
Use a TVS diode for transient and ESD protection on the Output DC Protection circuit. Ensure that the TVS diode used can protect against ESD strikes of at least 8 kV.
Rectification, High-Frequency Converter, PFC [2] and
Secondary-Side Rectification and Filter Circuits [3]
Enable The Rectification, High-Frequency DC-DC Converter, and PFC Circuit to generate the DC voltage and to charge the battery pack efficiently. Use MOSFETs which allow the switch-mode circuit to operate at a high frequency. Look for MOSFETs with Low gate charges, low RDS(On), and fast switching times. MOSFETs are available with gate charges as low as 14 nC, RDS(On) under 150 mΞ©, and switching times of 50 V/ns.
For efficient operation, consider low forward voltage drop Schottky rectifiers on the Secondary-Side Rectification and Filter circuit. Schottky diodes can operate at the high frequency of the switch-mode DC-DC converter.
A small number of components yield robust, efficient performance
The judicious selection of components can provide high protection to the battery pack, power tool, and battery charger. In addition, effective component selection can maximize the power tool's and its charger's efficiency. If designers would like assistance in selecting circuit protection and efficiency components, they can take advantage of a component manufacturer's expertise to save development time and get help with the following:
- Cost-effective component selection
- Compliance with applicable safety standards
- Pre-compliance testing (offered by some manufacturers) to minimize the cost of product certification by a national testing lab.
The result will be a safer, more reliable, and more efficient cordless power tool.