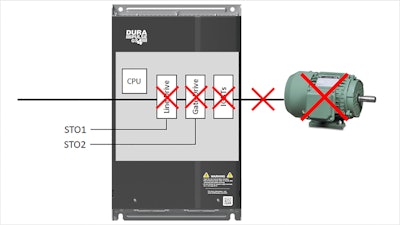
Electric motor-driven equipment must be provided with the proper safety provisions to protect operators. This is commonly performed by creating an emergency stop (e-stop) electrical interlock which activates if an unsafe condition is sensed or an operator triggers an e-stop device to put the electrical equipment into a safe state—usually ‘off’.
For machinery motors operated by variable frequency drives (VFDs), safety designers can achieve this functionality in a few different ways. This article looks at the pros and cons of traditional approaches and then discusses why a newer option called safe torque off (STO) is often the best way to deliver improved VFD motor safety.
Classic VFD E-Stop Options
Traditional e-stop options disable the power going into or out of a VFD upon an e-stop event to stop the associated motor.
A contactor installed upstream of the VFD power input can be opened if the e-stop circuit is tripped, removing power from the input side of the VFD and causing the motor to eventually coast to a stop. However, VFDs do not immediately power down when input power is removed. This vital action can take several seconds, or even longer depending upon how long it takes the DC bus capacitors to discharge completely. A lot could go wrong during this time, so this approach is not considered fail-safe but it is better than nothing.
Alternately, an e-stop contactor can be installed downstream of the VFD power output to positively disconnect the motor from any power. This method does remove torque from the motor immediately and provides a coast-to-stop motor action, but there are issues. For some VFDs, opening the output power circuit while running under load can cause permanent damage to the VFD. While effective and fail-safe for protecting personnel, replacing a VFD after an e-stop is not practical.
As a third option, designers can arrange the e-stop circuit to interlock with the VFD control wiring, removing the run signal or opening the normally closed stop signal. This allows for a controlled stop of the VFD, but it is not fault-tolerant as the stopping action relies on the software of the VFD to be operational and not corrupted.
Modern VFD STO E-Stop
Newer and higher quality VFDs today incorporate an integrated safety feature known as safe torque off (STO). Choosing a VFD with an STO function tested and certified by a nationally recognized test lab, such as TÜV Rheinland, can make it easier to design safety systems.
STO is implemented in the VFD’s hardware to ensure fault tolerance, and it turns off output power, preventing the motor from producing torque. Therefore, STO is considered a fail-safe method to remove output torque and cause VFD-controlled motors to coast to a stop.
VFDs use incoming power to charge a DC bus, which in turn supplies insulated-gate bipolar transistors (IGBTs), and the VFD logic commands the IGBTs to control power from the bus to the output motor connections. The STO feature is directly connected to the driver circuits upstream of the IGBT gate, so it works by prohibiting the IGBT output circuits from sending current to the motor (see Figure 1 above).
Since the power device cannot turn on there is no current to the motor, so no torque is produced by the motor. In fact, the STO function, if present on a VFD, cannot be disabled by the VFD’s software. If the VFD is installed in an application where it is desired to not use the STO function then terminal block jumpers must be installed as a hardware bypass.
However, it is important to note the VFD output circuit is comprised of solid-state components, so the circuit will not physically open, and voltage may still be present at the output terminals. Still, this is considered fail-safe since the STO circuit is accomplished with and through the hardware design, with software not involved.
STO Details
VFD STO reliability is improved by a degree of redundancy because the typical circuit is triggered by two separate inputs expecting normally closed circuits. The typical STO dual-channel input circuit has tight tolerances for when these two individual circuits close. A safety relay with a dual-channel output is recommended to activate these inputs, as opposed to a general-purpose relay.
Figure 2: Typical STO circuits are implemented as dual-channel inputs operated by a safety relay, to provide improved reliability through redundancy.
If one or both channels opens, then STO is activated. After STO has been activated the VFD will be prohibited from restarting until the STO circuit has been reset (both channels closed) and a reset/restart sequence occurs. This can be a reset command from the operator or control system, or the start signal can be removed and reapplied.
STO is often the best choice to e-stop VFD-controlled motors where a coast-to-stop condition will not endanger personnel. However, designers must consider that a coast-to-stop method is not safe for personnel in some installations. There may be certain cases where designers must plan to execute a controlled stop before triggering STO, and designers must always take into account what could happen if any external circuitry fails. They may also consider the addition of motor braking for some applications.
Because the risk of shock or electrocution still exists even when STO is active, STO should not be used when performing maintenance on a motor connected to a VFD. A proper lock-out-tag-out procedure using a local disconnect and/or powering down the VFD completely is recommended.
Driving Safety with STO
Designers must understand and follow all applicable codes and standards when designing for safe operation and maintenance practices. Performing a risk assessment will determine what SIL, PL ratings, and Category are required to minimize risk to personnel, and establish the minimum ratings needed for VFD selection.
STO is a significant safety feature found on new variable frequency drives. It helps designers, OEMs, and end users achieve better equipment safety performance while requiring less hardware and lower overall complexity than traditional methods.
Kevin Kakascik is a Technical Marketing Engineer at AutomationDirect. Over his 20-year career he has held controls engineering positions for machine OEM’s, entertainment industry systems integrators, and material handling systems integrators where he estimated, designed, commissioned and started up systems. Kevin has worked at AutomationDirect since 2013 in technical and marketing roles. He holds a bachelor’s degree in Computer Science and Engineering Technology and an associate’s degree in Electrical Engineering Technology.