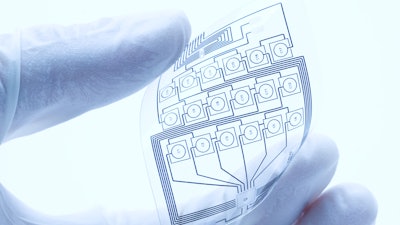
A smartphone touchscreen is an impressive piece of technology. It displays information and responds to a user’s touch. But as many people know, it’s easy to break key elements of the transparent, electrically conductive layers that make up even the sturdiest rigid touchscreen.
If flexible smartphones, e-paper and a new generation of smart watches are to succeed, they can’t use existing touchscreen technology.
We’ll need to invent something new – something flexible and durable, in addition to being clear, lightweight, electrically responsive and inexpensive. Many researchers are pursuing potential options. As a graduate researcher at the University of California, Riverside, I’m part of a research group working to solve this challenge by weaving mesh layers out of microscopic strands of metal – building what we call metal nanowire networks.
These could form key components of new display systems; they could also make existing smartphones’ touchscreens even faster and easier to use.
Problem with Indium Tin Oxide
A standard smartphone touchscreen has glass on the outside, on top of two layers of conductive material called indium tin oxide. These layers are very thin, transparent to light and conduct small amounts of electrical current. The display lies underneath.
When a person touches the screen, the pressure of their finger bends the glass very slightly, pushing the two layers of indium tin oxide closer together. In resistive touchscreens, that changes the electrical resistance of the layers; in capacitive touchscreens, the pressure creates an electrical circuit.
Indium tin oxide is very conductive, making touchscreens respond to a user’s touch with lightning fast speeds. But it’s also very brittle, making it unsuitable for more flexible displays. In addition, there isn’t enough indium, largely produced by refining zinc and lead ore, to meet ever-increasing demand.
Potential Replacements
Any replacement for indium tin oxide must be transparent – otherwise, there would be no point to using it for a screen. It must also conduct electricity well. Some potential replacements for this indium tin oxide layer include carbon nanotubes, graphene and conductive polymers
But each of them has its problems. Carbon nanotubes usually have high electrical resistance when contacted to one another so they do not function well as meshes.
Graphene would be excellent – it is highly conductive, flexible and transparent. However, there is not yet an industrial-scale process for producing enough graphene to meet the demand. Conductive polymers are easily molded into different shapes and conductive enough to be used in some photovoltaics and LED-based devices, but their tendency to absorb light means they’re not yet good enough to be used as a fully competitive replacement for indium tin oxide.
Exploring Metal Nanowire Networks
A promising replacement for indium tin oxide could be metal nanowire networks. They are made up of individual silver or copper wires, tens to hundreds of nanometers in diameter, woven together in an interconnected mesh. It’s transparent in the same way that a screen door is – the individual strands of the mesh are so small they don’t obscure the overall view.
Silver nanowires can be prepared in solution by a chemical reaction between silver nitrate and ethylene glycol at high temperature. When the solution is spread across the back of a touchscreen (made of an insulating material like glass or flexible plastic), the liquid dries and the nanowires form junctions with each other, creating the mesh.
Producing devices with silver nanowires has several advantages over the current standard, indium tin oxide. Silver is 50 times more conductive and can be used in a wider variety of devices. Making silver nanowire devices is also projected to be cheaper.
Other benefits are obvious when comparing fabrication methods. Indium tin oxide is applied to a touchscreen surface in an industrial process called “sputtering,” which involves effectively vaporizing the indium tin oxide, some of which lands on the touchscreen. But up to 70 percent of the material ends up on the walls of the sputtering chamber and must be removed before it can be reused. And indium tin oxide can’t be applied directly to flexible plastic surfaces, because sputtering involves lots of heat, which will warp the plastic.
By contrast, metal nanowires are made in a solution in the open air and can then be sprayed onto sheets of flexible material with a process called roll to roll coating. This process has been used since the 1980s to make components for solar panels.
Remaining Challenges
No one is quite ready to bring metal nanowire networks into the smartphone market. Silver and copper corrode when they’re exposed to air; researchers including my lab group and many others are trying to find ways to coat them with conductive polymers or even other metals, to protect them from the air without sacrificing transparency or conductivity.
And another challenge that remains is how to embed metal nanowires in between flexible plastic sheets. But one day, perhaps not long from now, we will be able to marshal all this research into creating fully working devices using metal nanowire networks.
This article was originally published on The Conversation. Read the original article here: https://theconversation.com/making-flexible-electronics-with-nanowire-networks-76260.