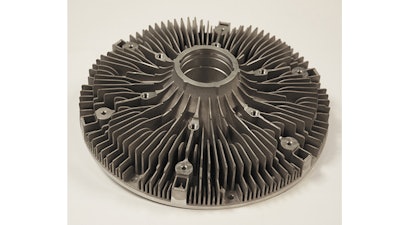
CAD models and prints don't always provide a complete picture of how the part will be used and how it is expected to perform. For example, a prototype print can be complete with all the detailed specifications for the part yet fail to communicate a very critical piece of information—information that can spell the difference between success and failure.
In one particular case, a part slated for eventual die-casting was to be used in a manner in which its heat transfer characteristics were crucial. While the end product performed well in prototype testing, the production part was overheating in the field. A root cause analysis showed that the prototype parts were cast in an aluminum alloy whose heat transfer was 1.5 times greater than the production alloy. Had the prototype supplier questioned the buyer/designer regarding the anticipated use of this component up front, they may have advised that some things be done differently. The diligence would have ensured a more accurate simulation of the production process.
Prepare for a full briefing with the prototype supplier way ahead of time by compiling a list of issues critical to a successful outcome. That list, of course, will include your CAD files, prints and a list of topics to cover. As a seasoned designer, you will have developed the list over time while still working out the design of the part in question. From experience, you know to cover the basics:
- How much time should you schedule for the production of the prototype, allowing for changes in design and retesting?
- What secondary operations may be required?
- How much will changes cost both in time and dollars?
- How will the part be used in the final assembly?
- What critical information does the prototype supplier need that is not spelled out in the prints?
- What kind of tests will need to be run on the part?
- How many prototype castings will be required?
- What is the part's release date?
- What is the product launch date?
- Will the production tooling be ready on time, or will you need some interim castings?
- Who else should be involved in the initial meeting with the prototype supplier?
Make sure to contact the supplier ahead of time to coordinate schedules and invite the prototype supplier to add their expertise to ensure a successful outcome.
Double-check to ensure you have selected the best prototyping process for your part, and finally, contact your chosen supplier if you finish your design and have lingering questions.
---
Robert Kowalczyk is a prototype casting engineer with more than forty years of experience in prototype and low-volume casting production. In his writings and speeches to industry groups, he has continually focused on the overall prototyping processes for cast metal parts and how best to produce cast prototypes that most accurately simulate the eventual production die casting. Kowalczyk is president of Aluma Cast Foundry in Appleton, Wisconsin, which serves manufacturers in various industries. He can be reached via email or phone at 920-596-1988.