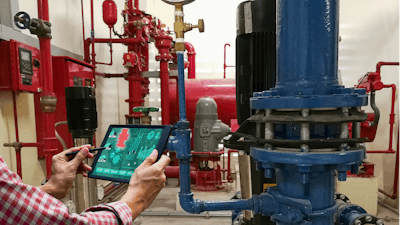
Although most manufacturing facilities had preventative maintenance plans in place before the pandemic, and solidly adhered to them, returning to a post-crisis facility may reveal a much more regimented and driven atmosphere. While many of the staff were able to perform their jobs from home, critical workers on the production lines, as well as maintenance staff, were not.
The most proactive of facilities used the time where manufacturing needs weren’t quite as high to ready themselves for the return to normal.
While You Were Out …
The production facilities that weren’t making front line items had some slack in their production schedule - possibly for the first time since the facility opened its doors. As any production manager knows, there is no such thing as downtime. There is simply a small window where the orders haven’t come in yet. Manufacturing facilities around the world planned for the times to come by making ready their facilities as though they would open their doors the next day to conduct business as usual.
Essential staff in every production facility typically includes an engineer, a mechanic, and several of the production management staff. In Emergency Contingency Plans, they are known as the “Point Of Contact” - in an emergency, they will be the staff staying behind to turn off the machines and make sure no open flames are left on to burn the facility down while the facility is being evacuated. During the pandemic, you could find the contingency team looking around the production floor and devising a plan as to how to prepare themselves for the influx of orders when they were given the approval to operate as usual.
Some of the facilities that were left without any orders to fill took advantage of the downtime, and their maintenance staff was able to address their production machines. The result is a facility that is able to operate at full speed with all machines running on spec. And producing a quality product that is rolling out with nearly zero maintenance-related downtime affecting production.
How To Use This Model Post Crisis
If you are in an industry that is still feeling the sting of unplanned downtime, the best use of your labor dollars could be overhauling your equipment. Machinery that has been properly maintained will need zero downtime for unplanned maintenance.
The great thing about machines that have been overhauled is that their output is as the product was designed. You’ll see nearly no recall material because the machine isn’t overcompensating for worn or broken parts. Simply stated, your machine isn’t walking the product out of spec to over-correct itself. A machine producing quality output is not stopping for adjustments. It isn’t having a product held up waiting on the lab to clear the sample, and it isn’t being reworked or, even worse, scrapped.
If your industry is back to business as usual, get out ahead of the busy season. Allow your maintenance team to perform annual preventative maintenance on all equipment. Prepare as much of your equipment as realistically possible to run around the clock without the need to perform minute repairs that cost your facility valuable production hours.
Don’t Forget The Safety Standpoint
It is a fact that machinery that is properly maintained on a regular basis is safer to operate. You won’t have leaking fluids from blown seals creating slip and fall hazards for operators. You won’t see operators climbing into cages making fixes to keep the product from sliding off the line where a conveyor belt is snagging. The fact is, when machines aren’t running the way they were intended to and both the machine and the operator are overcompensating for that fact, employees can get hurt.
There are many manufacturing facilities that will face much more scrutiny from inspectors and government agencies post-crisis. That is the nature of a recovering public; they don’t want to risk infection again. Those in many branches of manufacturing may be exposed to increased testing, as well as more in-depth, and frequent inspections. And any one of the possible agencies may be their new oversight team. With this new microscope viewing your facility, why take any extra risks? Properly maintained machines keep people safe, and that keeps liability minimized.
Don’t Spend Where You Don’t Have To
Everyone is watching their bottom dollar during the post-crisis return to normal operations. The most frustrating thing to see in production and manufacturing facilities is money being thrown into band-aid parts. You can toss seals and bearings at a machine until you’re blue in the face, but if you need to replace a hydraulic pump and its lines are all on their last leg, you'll need to stop and think about the real cost of applying band-aid solutions.
Maintenance costs are decreased 5-10 percent when a preventative maintenance program is in place, with maintenance time repairing machinery decreased by 20-50 percent in those facilities. And if you sign a mechanic's paycheck, you know what that percentage equates to in overtime dollars. Don’t spend your money as we’re all watching the economy behavior very closely. Use your maintenance team to assist you in getting your business back to its production and financial goal points. Preventative maintenance and facility overhauls, when feasible, are advisable ways to make that happen.
Talmage Wagstaff is the Co-Founder and CEO of Redlist. He has degrees and extensive experience in civil, mechanical and industrial engineering.