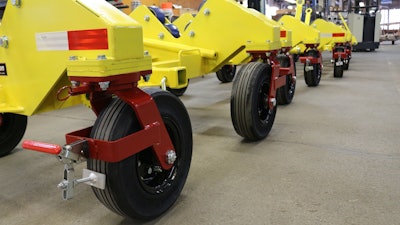
John knew he had to lean hard into the cart to get it moving down the aisle and into position for assembly. Loaded, this industrial cart weighed more than 2,500 lbs. At least once an hour, someone had to push one of these from a parking spot on the main aisle in the plant to a position about 50 feet away on the assembly line. There, operators would remove parts and install onto assemblies as they rolled by. Once empty, it was an easy push back into parking. But loaded, these beauties took either a herculean effort of a big, strong guy like John (6’ 2”, 235 pounds of former high school linebacker) or a couple of other workers. John expected that one day someone would sustain a serious back or shoulder injury moving these loads. He was just hoping it wasn’t him.
Injuries Waiting to Happen
Bureau of Labor and Statistics (BLS) data tells us there were almost 150,000 lost time accidents in the U.S. in 2017 as a result of back injuries. An additional 68,000 workers missed a day or more of work due to shoulder injuries. Many of these were caused by pushing and pulling heavy loads on wheeled devices. We know that a substantial portion could have been avoided by better wheel selection.
While the number of industrial injuries has gradually decreased over the past seven years, today’s average worker is both older and heavier than in previous years. Our national demographics also make it more difficult to find new workers, particularly with a near-record low unemployment rate. These demographics make it more imperative than ever to reduce the physical demands on our workers. Lost time and insurance costs make every injury expensive, but the added cost of finding replacement help and training that help is skyrocketing – if one can even find additional workers. Lost production is lost opportunity, and can lead to disappointed customers and future business challenges. A good working team is a strategic asset. Like any sports team, losing a key player makes a big difference in performance.
Wheels Matter
Data exists to optimize wheel selection and protect our valuable workers. Liberty Mutual has long made available data to predict unsafe situations likely to lead to injuries. This information has been used for decades to develop ergonomic guidelines in workplaces to reduce injuries. Pushing and pulling forces are significant parts of this available data, which every company can use to establish maximum manual pushing and pulling forces and reduce exposure to accidents. Solutions lie largely in wheel selection, which makes a huge difference in forces required to move loads.
Several industrial wheel manufacturers have extensively tested wheels under loads, and have data to guide wheel selection based on pushing and pulling forces for given loads. Distributors can help their customers access this data and thereby make more informed wheel purchasing decisions. For the user, all that is needed is the maximum load to be pushed or pulled and the largest push and pull forces acceptable in the workplace. Safe wheel selections can be made from this information.
Many carts and dollies in the workplace have original wheels or casters that may pose substantial risk to workers pushing them under load. Therefore, simply replacing wheels with new ones that match the originals does nothing to reduce the risk of injury. The most common criterion used in caster and wheel selection is load capacity – how much load can a given wheel or caster carry? It is common to find four casters on carts, so simple math says to divide the total load (including the weight of the empty cart) by four, and use a caster that has at least that much load capacity.
A Question of Ergonomics
Missing from this process is the ergonomic consideration. The “ergonomic load capacity,” or amount of load that can safely be pushed or pulled by a worker, may be significantly less than the rated load capacity. This ergonomic load capacity is not a published number, but one that must be derived by a user. The Liberty Mutual tables can assist in deriving a safe push/pull force, and that number can be used to select optimum wheels by accessing wheel manufacturers’ data.
Generally, ergonomic considerations will lead to selecting a wheel or caster that has substantially more rated load capacity than seems necessary (or “overkill”), but the workers will greatly appreciate the extra investment. Normally this looks like a bigger – and probably more expensive - wheel than the original. The company’s reward will be reduced injury exposure, along with potentially more worker productivity thanks to less fatigue. Larger diameter wheels roll more easily than smaller ones, and wheel materials and tread types also have varying rolling characteristics. Since there are so many different wheel types and sizes available, it may be easiest to work with a reputable distributor or manufacturer to provide a handful of acceptable options and optimize selection.
Investing in our workers is good business. Most employers invest in workplace training and skill development. Yet, more hidden investment opportunities like safer pushing and pulling may be overlooked. Make better ergonomic wheel selection part of your 2019 workplace safety initiative.
For more information, visit www.MotionIndustries.com/IEN
About the Authors:
Jim Komasinski is the Industrial Specialist for the corporate accounts team at Motion Industries. For over 20 years, Komasinski has walked side by side with his customers, providing them with product applications, project management, and identifying ways to better streamline the internal and external supply chain.
Dave Lippert has worked in the caster and wheel business since 1982. With a background in engineering, he has served in roles ranging from shop floor supervision to his current position as President of Hamilton Caster & Mfg. Co.