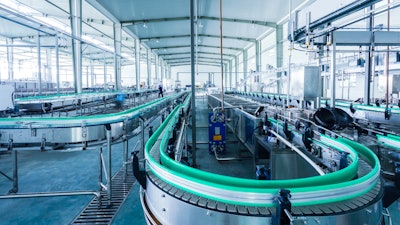
There’s never a good time for a piece of manufacturing equipment to break down. Not only can it mean costly repairs, but downtime also means delays and a loss of productivity. The reality is no value is being produced, yet overhead costs remain.
Findings from a recent survey of 450 field service and IT leaders by Vanson Bourne and Service Max were summarized in a report, entitled After the Fall: Cost and Consequences of Unplanned Downtime. The survey found that:
- 82 percent of companies have experienced at least one unplanned downtime outage over the past three years (average number of outages: two).
- 70 percent of companies lack complete awareness of when equipment assets are due for maintenance or upgrade.
- Zero unplanned downtime is now the No. 1 priority or a high priority for 72 percent of organizations.
- Field Service Management is directly tackling the problem of unplanned downtime using the latest digital capabilities, shifting service, maintenance and downtime from reactive to predictive.
The costs associated with downtime can range significantly depending on the size and complexity of your production process. Large manufacturers estimate losing anywhere from $100,000 to $250,000 per hour during unplanned downtimes. Smaller manufacturers may not lose as much per hour but that doesn’t mean it doesn’t hit their bottom line just as hard.
One way to prevent unplanned downtime is to implement predictive maintenance practices. These practices monitor equipment using a variety of performance metrics. Sensors on the equipment capture key operational data essential for the proper function of that piece of equipment. The data collected is processed and the results provide manufacturers insight into the system’s operations. More importantly, it provides a reliable method for determining when equipment may fail.
Being able to predict when maintenance should be performed is invaluable. Knowing when a part is likely to wear out or fail provides facility managers the ability to schedule and plan for downtime in advance. This planning saves manufacturers valuable time, resources and money by eliminating unplanned downtime that creates disruptions to the workflow. The ability to keep equipment operating at peak performance ensures each item produced meets specified quality standards.
In addition, knowing which parts may fail, and when, allows the opportunity to order replacement parts in advance, instead of waiting days and sometimes weeks for a new part to arrive. This also eliminates the added expense of rush orders for new parts.
However, it’s not just high tech that helps prevent unplanned downtime. Having a strong maintenance team is your first line of defense. At Wisconsin Plastics, Inc. (WPI), we assign machines to individual maintenance techs for a minimum of one year. They take ownership of them, performing daily inspections and general maintenance activities as needed.
By assigning machines, the techs take pride in ensuring their machines are operating efficiently and are well maintained. Plus, the techs develop an intricate understanding of each of their machines and are able to quickly identify when it may not be operating at peak performance. If a situation arises in which a maintenance problem is outside of their skill set, then a maintenance supervisor or manager provides assistance.
This marriage of digital and hands-on approach is highly effective in preventing unscheduled downtime. Another benefit is that by understanding when parts, that naturally wear out over time, need to be replaced, you can plan for those downtimes in your overall production schedule. This allows for the reallocation of employee staffing so that productivity can take place in other locations within your facility while maintenance is taking place on the machine that is down.
Ultimately, eliminating unplanned downtime allows you to meet your production schedule and deliver quality products on time to your customer.