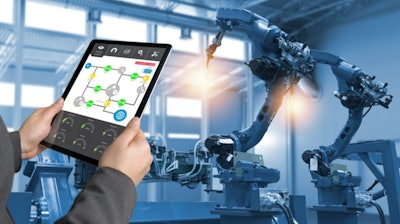
To succeed and stay competitive in today’s global marketplace, manufacturing companies must find ways to continuously improve their productivity. Towards this goal, most manufacturers implement Lean Manufacturing practices and associated Total Productive Maintenance (TPM) programs. Key to the success of these initiatives is standardizing data measurement, as well as establishing a means of evaluating improvements made and tracking their progress over time.
The most commonly used metric for measuring Lean Manufacturing is Overall Equipment Effectiveness (OEE). The three individual components of OEE – Availability, Performance and Quality – have a direct correlation to the TPM Six Big Losses (unplanned and planned downtime, slow cycles and micro-stops, production, and start-up losses) making it a useful framework to identify root causes of inefficiency and to help users prioritize and validate productivity improvement efforts.
While these frameworks for measurement are vital to driving operational improvement, they are only as good as the data supporting them. And this is why many Lean Initiatives stumble right out of the starting gate. Because accurate, consistent and insightful data is often difficult and expensive to gather, streamline and manage.
With the growth of the Industrial Internet of Things (IIoT), however, this is changing. Emerging technology brings with it new possibilities for the automation and standardization of data collection, and a means for data to be organized in a more meaningful manner that empowers OEE measurement and improvement.
The Data Challenge
When first getting started with OEE, manufacturers need to choose between a manual data collection method or an automated data collection method. To best make this decision, it is important to consider what data is required, who intends to use it, and how it will be used. These determinations should then be balanced against what data is readily available versus what data is challenging to obtain.
When measuring OEE, the first part of “what data” is spelled out for you – you’ll need data-related equipment downtime, production throughput and quality rejects. Moreover, you will also need to determine at what level you want to collect and view that data. This is important because if you look at data from too high a level, then it may not be actionable; if you look at data that is too specific, then the results may be too hard to sort through and prioritize.
Manual data capture can be a good way to get started, but this approach is often inaccurate, difficult to standardize, and poorly suited to the purpose if you intend to use the data for any real-time decision making. It is for these reasons that a manual approach to data collection can be a significant barrier to quickly building momentum and long-term success.
Right-Sizing Automation Data Solutions
As the adage goes, you can only improve what you can measure, but without automation, data collection for operational improvement is no easy task. With the development and integration of equipment sensors and OEE/productivity software technology, data collection can be streamlined, far improving data accuracy and consistency. And in time, collected data can generate a storehouse of trusted and meaningful information that can be used across the organization for improvement initiatives. However, there can be a disconnect between intelligent machines that can collect data and the existence of right-sized tools for data management.
With the expansion of Industry 4.0 and Smart Machines, it would seem easier than ever to drive efficiency in your production. However, the change to intelligent machinery and data automation takes time and capital investment, that is unless you can tap into smart equipment already on your line.
Videojet coding and marking equipment, for example, offers built-in intelligence for data collection, and when already integrated into a packaging line, this equipment has a front-row seat to what’s going on in your production. Like many Smart Machines, however, while the equipment can collect the data, it’s the introduction of a new means of managing that data that is going to make a difference for manufacturers.
Up until now, there has been a disconnect between the desire of small to medium-sized manufacturers who want to automate data collection and to do something meaningful with it, and the existence of an affordable, scalable and easy-to- implement solution for doing it.
Navigating the value proposition of an OEE/productivity software solution can be challenging. When evaluating a solution, a thoughtful understanding of your needs, both now and over the long term, is necessary.
Scalability and complexity are big things to consider. Some offerings may be complex to implement and are more robust in functionality than needed (i.e. you may not need a solution that will control the chillers in your production operation). Other offerings may be highly-specialized and geared toward a specific user, perpetuating a data-silo issue. And still others might be overly simplistic, giving you high-level data that leaves you multiple steps away from a root cause of a problem.
With software solutions available at a wide range of prices, you’ll also want to find something you can get up and operating quickly at a cost that fits your budget. Finding a perfect balance of all of these elements can be tricky, so finding a trusted partner with knowledge of your production, as well as your needs and processes, is also important.
While there are OEE/productivity software solutions that can help streamline the data collection process necessary for driving specific operational improvements, due to scalability in size and complexity, they are oftentimes out of reach for operations without the resources to manage them. There is, however, a newer option that provides a lower cost and ease of setup that make the value proposition of an OEE/productivity software more attractive than ever.
Videojet offers their IIoT-enabled productivity solution that gives manufacturers visibility across their packaging lines, with the goal of maximizing production throughput, reducing operating costs and driving process improvements. It not only provides users with a dashboard overview of how their entire operation is running, but it can also show productivity in real time where and when work is being done.
Advances in technology are creating meaningful and tangible opportunities to improve OEE and productivity. Finding a right-sized productivity solution for managing the data collected is as important as identifying a partner who understands your production and processes. Finding a perfect balance of both will ultimately help you drive improvements and profitability.
Bob Neagle is Commercial Director for Productivity Solutions at Videojet Technologies, Inc., where he oversees sales and marketing activities for the Videojet Software as a Service (SAAS) portfolio of products.