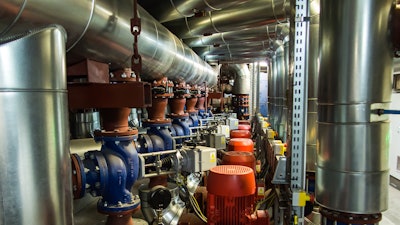
It’s a tough life for centrifugal pumps. Harsh conditions, increased horizontals, and economic realities are pushing intermittent-duty pumps to the furthest limits of their capabilities. Historically, pumps have simply not been built to continuously run at a full rod load. Because of this, they fail. The fundamental question is: why?
Let’s begin with the obvious. Insufficient lubrication is the main reason for pump failure. To understand why, we must consider the purpose.
Feeling the Pressure
Lubrication systems are built for two very important reasons. Firstly, they eliminate metal-on-metal contact. Secondly, they eliminate heat. By manipulating the pressure of the lubrication as well as flow rates, which are inversely proportional values, you can provide pump components with the appropriate lubrication to avoid premature failure.
The problem is that every component—and there are a great many—has unique requirements for pressure and flow. For example, Roller bearings function with high flow rates and low pressure to reduce heat quickly. However, shell bearings require low flow rates and high pressure to get a thicker film into tight spaces, which allows them to withstand the aforementioned diverse operating conditions.
Manufacturers try to aim for the middle, attempting to find the optimal pressure-to-flow ratio making each pump component function. Unfortunately, that magic number simply doesn’t exist. Both flow and pressure are inevitably compromised at each end of the scale, subsequently affecting every moving component.
Pressure isn’t the sole lubrication-related factor that results in pump failure. Lube contaminants have the potential to destroy your bearings and severely decrease the expected life of your pump. This is another reason for lubrication-related pump failure.
Essentially, there’s two main contamination sources: particulates originating within the pump resulting from metal-on-metal contact; and outside debris, like grit, entering the system through exposed covers and ports. It’s important to consider that even soft debris has the potential to cause irreparable damage under pressure. Excessive force on anything other than lubricant can cause an impression or stress riser on a single component. With every moment of operation, you escalate the cycle of damage and increase the chances of failure.
All the Pieces of the Puzzle
Now, let’s discuss components. Our engineers saw that as many as 60 percent of pump failures begin with the roller bearing—so let’s begin there. To understand the problem, you must think about how industrial pumps have evolved. Over the years, manufacturers have continued to increase horsepower to meet increased demands on operating requirements, with particular focus on frame design, whilst paying less attention on components.
This is the resulting problem; when you apply a load and unload, or a particular form of loading to any component, that component will subsequently go through a form of molecular fatigue. There is a specific range of stress, with a limited number of cycles prior, where components reach their breaking point and start to spall or break up, causing a chain reaction of internal pump destruction. If you up the load without altering the parts, you decrease the life cycle.
Structural Rigidity
Now, let’s discuss the lack of structural rigidity, which is engineering talk for a cracked frame - a situation no operator wants. In most cases, workers aren’t given permission to be around the pump during operation, so it’s too late by the time a problem becomes apparent. You’ve got an oil leak, environmental issues, the cost of the clean-up, and the impact of downtime.
Around 80 percent of cracks begin around welding points. It’s vital to bear in mind that any weld is an inherent defect. Think of it as an Achilles heel that’s waiting for the specific conditions to occur. What are these conditions?
One main reason for a frame to crack lies within the pump design itself. A lot of manufacturers forget to include load requirements, considering the frame as just a shell that contains the oil. However, even the smallest misalignment—we’re talking as little as 5 arc-minutes, or a little more than the width of a regular sheet of paper, can shorten bearing life by as much as 35 percent.
Additional factors include lack of welding access as well as failing to meet American Welding Society D1.1 (AWS) code during the design and building process. It’s impossible to make or check a good weld if you’re unable to see it. Knowing how your pumps work is vital to ensuring you get the longest possible life out of your industrial pumps.
The article was submitted by Andrew Morton on behalf of the Weir Group and the quality pumps offered by Gabbioneta.