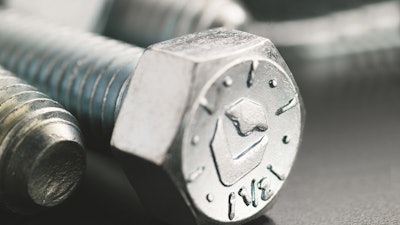
For most manufacturers, downtime is the largest source of lost production time. With the primary goal of equipment utilization, nothing is more frustrating for manufacturing, production and maintenance managers than watching equipment sit idle. Whether a plant is producing injection-molded parts, castings, stamped parts or finished assemblies, the manufacturer isn’t making money if machines are down.
Maintenance and repair of a wide variety of machines is a daunting task. Preventive, predictive and proactive maintenance are essential to equipment reliability, ensuring availability and performance. However, this task can be simplified by instant access to the components and products necessary to repair and maintain equipment. The key to maximizing equipment and time utilization is two-fold: optimized inventory management and highly engineered products made for maintenance mechanics.
Never Out, Never Over, Just Right
Optimized inventory management is an approach to insuring part availability at the instant the part is needed, without the loss of production unavoidable with next day parts delivery. While this sounds a lot like vendor managed inventory (VMI), a standard service offered by many small-parts distributors, there’s a key difference. Optimized inventory management not only takes immediate part availability into account, it equally acknowledges the need to never be overstocked with too much inventory. It minimizes inventory costs associated with just-in-case inventory by monitoring consumption of consumable MRO such as fasteners, electrical connectors and components, hydraulic fittings, chemicals and abrasives on a weekly or bi-weekly basis. This simultaneously ensures the minimum “on-hand” inventory without risk of running out.
In addition, consultation on the right product for the application at hand is gained with true optimized inventory management service. For example, for large hole drilling, is it more efficient to use a drill versus a drill reamer combination? Or, in applications with high vibration, is it best to use a split lock washer, self-locking washer or thread-locking adhesive? These are only two examples of the myriad of technical and application questions that can only be answered through a consistent, hands-on approach.
So, who is responsible for knowing each facility’s usage patterns in order to maintain appropriate inventory levels? How is the consultative product selection process delivered on-site? A sales representative educated and experienced in delivering optimized inventory management should be a problem solver not just for mechanics, but for maintenance, electrical and operations engineers, too.
- Representatives who effectively deliver optimized inventory management:
- Make sure the right product is stocked at the right levels, in the right place, at the right time, simultaneously reducing downtime and capital outlay.
- Design and install the most efficient system of clearly labeled bins and cabinets, minimizing time spent looking for products.
- Continually manage product inventory on-site, eliminating time spent taking inventory and re-ordering small parts.
- Proactively provide consulting and innovations to maintenance and engineering teams.
This approach results in improved asset time utilization and productivity of highly skilled mechanics.
Maintenance Designed Products vs. OEM Products
Maintenance mechanics’ repairs usually involve fixing a point of failure or the weakest link in the system using a wide variety of components and products in small quantities. Unfortunately, design engineers sometimes optimize for component standardization and general performance, perhaps standardizing to a production grade 5 or 8 bolt because the finished product may use thousands of bolts.
Because fastener failure is the number one cause of loss of production, maintenance mechanics may choose to upgrade to a grade 8+ or grade 9 cap screw to prevent a future failure. Given the problems maintenance mechanics experience due to production grade product reliability, including liability issues, it’s not unusual for mechanics to seek out maintenance engineered fastening systems. A maintenance engineered, matched strength system, with durable components, provides better consistency, and greater clamp loads and safety margins than production grade products. In addition, manufacturers will achieve a lower cost overall, due to greater uptime.
The combination of optimized inventory management and maintenance-designed products is often overlooked until it is too late. For example, the construction equipment rental industry consisting of thousands of rental branches is well over a $50 billion industry. Rental equipment branch managers are highly focused on fleet utilization (time utilization or time on rent). A large piece of equipment can rent for several thousand dollars per day and each branch might have several hundred pieces of equipment in the local fleet. A $5.00 hydraulic fitting can prevent the piece of equipment from being rented and waiting until tomorrow will cost $2000, $3000 or $4000/day in lost revenue.
Availability, reliability, maintainability, and capability are components of the effectiveness equation commonly used in manufacturing performance measurement. Unplanned outages leave people and machines idle; products are not being made, which certainly affects a manufacturer’s bottom line.
Lawson Products’ combination of reps educated and experienced in providing optimized inventory management and highly engineered products serves to compress cycle time, maximize the productivity of mechanics, reduce inventory and provide innovation. The net result: maximum machine time utilization and maximum profits.