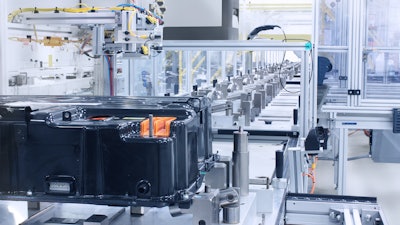
As battery manufacturers strategize for 2024, staying informed about present and anticipated trends is crucial in ensuring developers remain adaptable and ready for the introduction of new materials and methods.
Sustainability will continue to be a major emphasis in the upcoming year, with the integration of new, easily accessible resources and the adoption of energy-efficient processes. The battery industry is rapidly scaling to meet increased automotive demand, and these changes require uniformity throughout sites to maintain consistency as manufacturers adjust to trends.
Dry electrode coating
During battery manufacturing, a coating of active material is added to the top of the metal foil, creating an electrode. Traditionally, this process is done with wet, toxic solvents. The drying process can take up to 24 hours, costing energy and time and requires the hazardous solvents to be recovered and re-distilled.
Battery manufacturers are replacing the complicated coating process with dry electrode coating, eliminating the lengthy drying process and disposal of toxic solvents that can alter the physiochemical properties of coated electrodes. During this process, a powder is mixed to a polymeric binder, acting as a glue. This 'glue' is then applied to the metal foil. Through pressure and temperature changes, the mixture adheres to the foil. The dry coating process dramatically reduces the battery's size and cost, decreasing energy consumption and production cycle time.
Lithium iron phosphate (LFP) chemistry
Expect to see more electric vehicles with LFP batteries as North American automakers transition away from batteries with nickel and cobalt, as the materials are difficult to extract from the earth. Nickel-cobalt chemistries are also prone to thermal runaway, which raises safety concerns.
A key differentiator of LFP batteries is the longer lifespan compared to NMC and NCA batteries. These batteries also retain a higher percentage of charge as they age and show minimal degradation over time. By using a non-flammable electrolyte in the battery's chemistry, these units are also safer, removing the issues of toxic fumes and off-gassing demonstrated by lithium-ion or lead-acid batteries. These attributes also make LFP batteries safer to handle and dispose of.
Cell-to-pack (CTP) design
In the current modular setup, at least two separate thermal interface materials are used to maintain temperature. However, the additional weight and size result in a reduced pack energy density. Electric vehicle manufacturers have begun eliminating modules and the associated hardware and placing cells directly in the battery pack, increasing volume utilization and production efficiency while decreasing the number of necessary parts. This process improves pack energy density and decreases heating or cooling loads by the cooling plate.
The most notable impact of the cell-to-pack design is its positive effect on the vehicle's range. The CTP design weighs less, allowing manufacturers to increase pack volume utilization by 20% to 30%. This is a key differentiator, as 40% of Americans do not live in homes where a car can have a personal charger. Increasing the battery range increases the amount of potential electric vehicle owners.
High precision web tension control and synchronization with Rexroth CtrlX motion control.Bosch Rexroth
Although it may seem counterintuitive for electric vehicle manufacturers to seek ways to reduce energy usage, an EV's production footprint is approximately twice that of a conventional internal combustion engine vehicle. One study found that 46% of EV emissions come from production.
Mining for materials like cobalt and nickel releases toxic fumes into the environment, heavily affecting the area. An additional impact is the environmental cost of transporting these heavy batteries. By decreasing energy consumption and the weight of the battery and finding alternative materials, battery manufacturers are decreasing the overall environmental impact of production, bringing the EV industry closer to zero emissions.
EV sales increased 55% from 2021 to 2022 and are on the pace to rise from 7% of all U.S. car sales in 2023 to 50% by 2030. The heightened demand requires manufacturers to ramp up material production, driving the need for higher-speed automation and material transfer solutions. Connectivity and data availability are keys to increasing the manufacturing of these products while maintaining the expected quality.
Mark Ziencina is the market segment manager responsible for the battery and EV markets in North America. Ziencina has 29 years of factory automation experience, including sales of Rexroth products and capital equipment along with global account strategy formulation and execution experience.