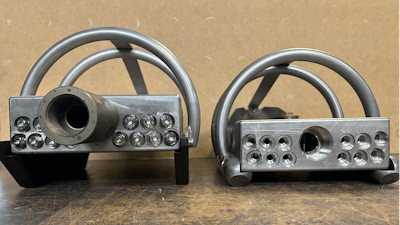
With increasing federal mandates on stormwater system monitoring and maintenance, municipal departments encounter significant budget and workforce challenges. In this context, the utilization of floor cleaner devices becomes imperative. These devices are crucial for eliminating sand, mud, sludge and heavy debris from storm lines, sanitary lines and culverts by directing powerful streams of water to clean pipelines effectively.
The challenge becomes more demanding in large-diameter stormwater pipes as they face issues with the accumulation of oversized debris like bricks, concrete chunks, wood pieces, corrugated metal and the occasional manhole cover. Furthermore, offset joints resulting from pipe dislocations may act as barriers hindering the floor cleaner's advancement. These obstructions can hamper effective floor cleaning, obstruct the device's path and potentially lead to its overturning—necessitating labor-intensive manual intervention and retrieval by the maintenance team.
Municipalities and contractors often rely on floor cleaners, also called bottom nozzles, to clean debris from the storm water pipes.KEG Technologies
“As storm water flows through the lines, sand, sediment and debris settles, builds up and then must be cleaned out using powerful, high-pressure water. Municipalities and contractors often rely on floor cleaners, also called bottom nozzles, to clean out this debris from the storm water pipes,” said Dan Story, an experienced trainer and Operations Manager at KEG Technologies, a manufacturer of sewer and storm line products including floor cleaners, Tier 1 to Tier 3 nozzles, chain cutters and camera nozzle systems. The Spartanburg, SC-based company is a member of NASSCO, the National Association of Sewer Service Companies.
“The problem is that you need to get the floor cleaner nozzle to come back, but it can keep getting caught on debris or pipe joints, which can be time-consuming and labor intensive to resolve,” added Story.
Innovation Clears Away Floor Cleaning Obstacles
Although floor cleaners are well established in the industry, some nozzle manufacturers have substantially improved the fluid mechanics of the jets to remove even heavy sediment and debris from pipes. As an example, KEG offers a complete floor cleaner family with 5 to 14 jets using patented fluid mechanics that provides superior cleaning efficiency in large diameter pipes, typically from 6” to 72”.
Due to advanced design fluid mechanics, the flow from the high-pressure water hose is converted to maximum cleaning power in each jet of the floor cleaner. The resulting flow from the various jets, as well as the jet angle design, make these floor cleaners ideal for removing sand, sludge, mud and compacted materials as well as heavy debris like rocks, bricks and broken concrete.
“The Twins” give the sewer cleaning crew the ability to clean very large, big bore round pipe, arch pipe and even large box culverts.KEG Technologies
“The amount of power due to the fluid mechanics is absolutely unbelievable,” said Story. “We’ve had sewer contractors call us and say that they were cleaning and washed part of a manhole lid back.”
Despite the power of the nozzles, however, the floor cleaners must still be designed to climb over, or avoid, significant obstacles. To resolve some of these issues, manufacturers of sewer jet nozzles design floor cleaners equipped with stabilizing skids. Nevertheless, conventional floor cleaner configurations prove inadequate in navigating the numerous obstacles present in large-bore pipes. The skids can often get hung up on offset joints within pipe, according to Story.
To enhance pipe floor cleaning efficiency, Story drew on an unlikely source of inspiration: the roll cages installed on four-wheel drive trucks and off-road vehicles.
“With a roll cage, if the floor cleaner hits something that causes it to roll over, it continues to roll over until it lands back on its skids,” said Story.
The skids are elevated by an inch to provide increased clearance over obstacles within the pipe, thereby preventing potential obstructions.KEG Technologies
The skids were also elevated by an inch to provide increased clearance over obstacles within the pipe, thereby preventing potential obstructions.
“4WD trucks take a similar approach in raising their profile so they can run over obstacles; it’s the same idea but on a much smaller scale. This allows the floor cleaner to run over cracks and even offset joints in pipe without getting stuck and having to be retrieved,” said Story.
According to Story, the new skids with higher clearance can be used with any existing KEG floor cleaners.
The sewer and storm line product manufacturer has also tackled another persistent industry problem – floor cleaning very large diameter pipe with heavy debris – in an innovative way. The company designed a Y-connector that allows two floor cleaners to be used together at the same time. “The Twins” give the sewer cleaning crew the ability to clean very large, big bore round pipe, arch pipe and even large box culverts. Typically, this approach is used to clean pipes with diameters 48” or larger.
“We’ve run the Twins to clear out debris through 13’6” bore pipe,” said Story.
New skids with higher clearance allow the floor cleaner to run over cracks and even offset joints in pipe without getting stuck and having to be retrieved.KEG Technologies
He explains that if the municipality or contractor already has a pair of matched floor cleaner nozzles, all they need is a Y-Connector and related minor accessories to enable working in tandem.
When unusual floor cleaning challenges occur in the field, KEG strives to be part of the solution, according to Story. He relates a recent example where a sewer contractor called with a unique challenge after purchasing the Twins for use in extremely big bore pipe.
“He said, ‘We’ve got hills in this pipe that are nine-and-a-half-feet tall and every time we go into it, the hill collapses on top of the nozzle [requiring it to be retrieved],’ recounted Story.
After meeting with the contractor, Story offered a customized solution.
“We built a small set of skis – similar to water skis – and bolted them to the front of the nozzle so when the floor cleaner reaches the hill, it can climb over it,” said Story.
Although the industry has used floor cleaners for decades, some of its longstanding problems are only now being comprehensively addressed. Municipalities and contractors that adopt these industry best practices can dramatically improve their pipe floor cleaning efficiency to effectively meet maintenance requirements.