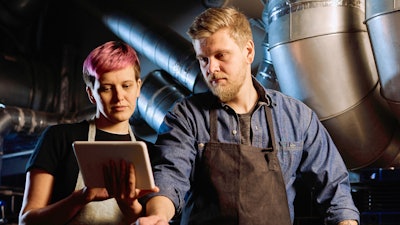
One of the largest causes of lost productivity in manufacturing is unplanned downtime. It creates unnecessary delays, unhappy customers, lost revenue and it costs manufacturers an estimated $50 billion each year, according to a study by PTC.
What can manufacturers do to reduce unplanned downtime and maximize asset utilization?
They’re increasingly relying on predictive and prescriptive maintenance solutions to anticipate issues and then resolve them.
Take for example, material handling equipment which is essential to the efficient packaging of consumer-packaged goods before they leave the manufacturing plant; or a bioreactor used to transform biochemicals into products in pharma manufacturing.
Failure of these vital (and expensive) pieces of equipment to operate as they should not only brings a halt to operations, but in many cases, it can impact quality when the equipment is working just enough below standards that they cause unsealed food items or loss of sterility in chemicals.
Both predictive and prescriptive maintenance, driven by AI and advanced analytics, can help manufacturers avoid these issues. Predictive maintenance alerts manufacturers to the likelihood of a piece of equipment failing, while prescriptive maintenance takes it one step further, telling them what they should do to resolve the issue.
What’s the Difference Between Predictive and Prescriptive Analytics and Why Does it Matter?
Predictive maintenance is an advanced maintenance strategy that utilizes data analytics, condition monitoring sensors and artificial intelligence (AI) to predict equipment failures and recommend specific actions to remediate them. While it can give manufacturers deep insights into asset performance, it measures key metrics in isolation which doesn’t evaluate their overall impact.
This strategy, while effective, comes with significant investments in condition- monitoring techniques and data specialists, and is therefore, most commonly applied to the most critical assets. However, because predictive maintenance is performed only when recommended, it reduces labor and material costs.
Prescriptive maintenance, on the other hand, not only predicts failures; it also makes recommendations on how to avoid them. It requires a cognitive system that can learn, adapt and understand unpredictable information by combining the data analytics from predictive maintenance with AI and machine learning.
As a result, it requires a stronger IT infrastructure. Prescriptive maintenance considers all the available data and prescribes actions to improve the reliability, productivity, quality and safety of equipment and processes.
A prescriptive approach uses historical data from operations, environment and defect factors to identify the causes of elevated defect rates. This information is used to not only analyze previous quality issues but can also be used to run ‘what if’ scenarios to predict likely defect rates going forward and drive recommendations such as modification to inspection patterns or recalibration of machinery.
In the context of an integrated quality management system, these steps occur in real-time to minimize costly operational delays. The two maintenance strategies are powerful tools when strategically employed together. Predictive maintenance collects monitoring data and predicts a potential failure. Predictive tools can detect a misalignment, based on sensor data for instance, well before it causes a system breakdown and automatically create a work order to correct the misalignment and send it to key systems and personnel to address the predicted failure.
Predictive maintenance spots a risk that requires action and human intervention. Prescriptive maintenance provides potential scenarios that can avoid or minimize poor quality issues and valuable downtime. It might suggest an approach to optimizing current machine usage, by adjusting a workflow to provide for more frequent calibration of an asset or reducing the speed of a process to extend the time before action would need to be taken.
It should be noted that not all organizations require the same level of reliability from their assets. Key questions should be asked to determine the best approach to any strategic asset management initiative, including:
- How reliable do our assets and processes need to be? What are our tolerances and risks?
- Do our workers have the right skills, tools and training to perform the required work?
- Do we have the right parts in the right place at the right time?
- Are our processes well-documented and accessible to workers that need to access them?
- Are we capturing and leveraging key data to enable proactive, real-time decision making?
Using Predictive and Prescriptive Maintenance to Boost Environmental Health & Safety
In addition to the quality, productivity and cost ramifications of faulty equipment, are the inherent safety issues. Workplace accidents can often be attributed to faulty equipment – failing equipment could become combustible, or safety mechanisms may fail to operate during manual operations.
A manufacturing plant can be made safer by noticing when a machine is not operating as expected. Leveraging automated maintenance solutions that can be integrated into the quality management system (QMS) can provide a complete picture of quality.
Equipment breakdowns will inevitably occur, putting a halt to the successful output of critical medical devices, food or vehicles that people rely on. Integrating predictive and prescriptive maintenance solutions into your operations can go a long way to keeping them humming along, while preserving costly investments in the equipment that runs your business.
About the Author
Osama Solieman, ETQ’s Chief Customer Officer, has been with ETQ for 16 years in a variety of customer-facing implementation and delivery roles. He has been an integral part of the company’s evolution from a company delivering strictly on-premise solutions to a leading provider of cloud-native quality management solutions.