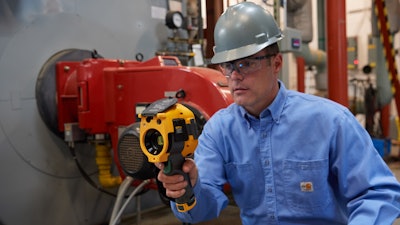
In today's competitive manufacturing landscape, achieving high levels of availability, performance, and quality is crucial for plant success. Manufacturing facilities heavily invest in their equipment and infrastructure, which are designed to meet specific capacity requirements based on demand. Therefore, effectively maintaining capacity is essential for maintaining competitiveness and driving profitability.
One key performance indicator (KPI) that manufacturers use to gauge their performance is the Overall Equipment Effectiveness (OEE) score. A simple way to think of OEE is the ratio of fully productive time to planned production time. A ratio of 1 or score of 100% would mean that the facility is running at ideal cycle time with no stops and all parts are good. A more useful way to score OEE which also provides information about the underlying cause of lost productivity is by using an OEE score derived from three fundamental factors:
Availability: This measures the operating real-time (ORT) in relation to the planned time (PT).
Calculation: ORT Ă· PT
Areas of Loss: Unplanned stops and planned stops
Performance: This evaluates the real speed (RS) compared to the planned speed (PS).
Calculation: RS Ă· PS
Areas of Loss: Small stops and reduced speed
Quality: This assesses the ratio of valid pieces (VP) to the total pieces (TP) produced.
Calculation: VP Ă· TP
Areas of Loss: Production rejects and startup rejects
Although the term OEE uses the term efficiency of “equipment” The OEE score is obtained by multiplying the availability, performance, and quality percentages together: Availability (%) x Performance (%) x Quality (%) = OEE (%)
While aiming for a perfect OEE score of 100% may be unrealistic, an OEE score of around 85% is considered good. To improve the OEE score, it is essential to establish a baseline by collecting plant data over a month and then assess the performance based on the three categories mentioned above.
Let's take an example of a manufacturer running continuously for 30 days, with a designed capacity of 50 products per hour:
- Availability: Expected hours of uptime: 720 Actual hours of uptime: 688 Availability score: 95.55%
- Performance: Expected number of products processed: 36,000 Actual number of products processed: 30,960 Performance score: 86.00%
- Quality: Number of products produced: 30,960 Number of products accepted: 26,935 Quality score: 86.99%
The OEE score for this manufacturer would be calculated as: Availability (95.55%) x Performance (86.00%) x Quality (86.99%) = OEE (71.48%)
In this example, the losses are primarily seen in performance and quality so improvements in those areas are vital to achieving a good score of 85%. Therefore, to maximize the system capacity, it is necessary to enhance performance and quality by about 8-9% each. By knowing the areas to focus on, reviewing the data, and observing the process, plants can determine what the root cause of the degradation is and take action to remedy it. Although the term OEE refers to equipment effectiveness, the resolution of issues affecting OEE has a human element and is dependent on workers having the tools and data they need to resolve issues efficiently.
Starting with a Strategy
Regardless of the product being manufactured, all plants face the challenge of degradation over time. Although not all issues are equipment related, it is crucial to maintain the reliability of machines and equipment because poorly maintained equipment will negatively impact all three factors.
Two essential groups of machines and equipment should be top of mind for every plant manager:
Revenue Critical: These assets directly impact the company's ability to win and generate incremental revenue. Continuous assessment is necessary, regardless of their condition, to ensure they operate at peak performance.
Production Critical: These assets must be operational for the company to generate revenue. Uptime is the key performance indicator, and the ability to predict failures is highly valuable.
It is important to note that criticality is not determined by the complexity or size of the equipment but rather by its impact on revenue generation.
Key Performance Parameters
There are many factors which can cause performance losses. Things like raw materials and process control can affect these but often the health of the machines are a major factor. Maintaining machines to a high standard is essential for reduced scrap and rework, and improved part consistency and quality. Since most manufacturing plants operate at or near maximum capacity, it is crucial for every piece of equipment to perform as expected to maintain uptime and consistent quality.
When considering revenue critical machines and equipment, it is vital to understand their Key Performance Parameters (KPP). KPPs are measurable values that equipment must maintain throughout their operational life. By ensuring equipment meets its KPPs, its lifespan is extended, unplanned downtime is reduced, and production quality remains consistent.
Performing a one-time audit to gather KPP data for critical equipment is necessary before developing a maintenance planning approach. This audit should be performed at initial install and updated as new equipment is added and retired.
Maintenance and Reliability Planning
Four common maintenance approaches in manufacturing plants include reactive (after-the-fact), preventive, predictive, and automated/self-maintaining. A reliable maintenance strategy usually incorporates a combination of reactive, preventive, and predictive approaches, with the latter two being more proactive in nature.
Preventive maintenance is the act of performing regularly scheduled maintenance activities to prevent unexpected failures. It often involves manual activities using test and measurement tools to collect real-time data and information about equipment. Predictive maintenance includes condition monitoring, data collection, and the use of computerized maintenance management systems to reduce the chance of failures.
To build a strong and effective maintenance program, various elements, tools, and resources need to be brought together. Here are examples of how to approach each OEE category, along with recommended tactics and tools for each:
Availability
Objective: Ensure uptime by eliminating unplanned equipment failures and minimizing planned stops.
Approach: Utilize wireless data collection and hands-on maintenance techniques to maximize equipment uptime.
Tactic 1: Implement computerized maintenance management system (CMMS) software to eliminate data gaps, enable data-driven decisions about asset health and maintenance priorities, and integrate maintenance and condition monitoring tools and software solutions.
Tactic 2: Establish a regular maintenance schedule for each machine to reduce failures and extend equipment life. Use preventive maintenance test and measurement tools like clamp meters, thermal imagers and insulation multimeters.
Performance
Objective: Maximize equipment speed by eliminating small stops and issues that reduce speed.
Approach: Focus on optimizing power sources, including power quality, compressed air systems, motors, and battery systems.
Tactic 1: Monitor power quality and conduct power quality studies to identify sources of poor power quality and energy waste, as well as protect equipment from future damage.
Tactic 2: Address compressed air and gas leaks, as they can significantly impact equipment performance. Use an acoustic imager to detect, locate and quantify the costs of compressed air/gas system leaks.
Tactic 3: Identify potential hot spots that could cause equipment failures or reduced capacity by using a thermal imager to capture thermography data and trend it over time.
Tactic 4: Test individual stationary batteries and battery banks to ensure measurement thresholds and tolerance ranges are maximized. Utilize a battery analyzer that provides predefined thresholds for quick notifications.
Tactic 5: Ensure automation industrial communications are not disrupted by electromagnetic interference (EMI) or other environmental factors. Use network traffic tools to identify high-loss network nodes and a cable analyzer to find susceptible network cables.
Quality
Objective: Maximize the number of valid pieces manufactured by reducing production and startup rejects.
Approach: Utilize vibration and alignment testing, along with calibration, to ensure precision and accuracy in equipment and machinery.
Tactic 1: Test equipment for excessive vibration and bearing condition using vibration analysis tools that measure acceleration, velocity, and displacement.
Tactic 2: Perform precision shaft alignments on rotating machinery to prevent early bearing and seal failures and reduce energy waste.
Tactic 3: Calibrate equipment back to factory standards to eliminate excess wear and ensure consistent performance.
Achieving Manufacturing Excellence
To become a highly successful manufacturing plant, availability, performance, and quality must be prioritized. By leveraging the right data, resources, and tools, a well-designed maintenance plan can elevate a manufacturer from average to a top competitor. The maintenance culture should be focused on continuous improvement, best practices, and continuous learning to drive success.
Remember:
- Increased efficiency in production leads to more products at lower costs and higher profit margins.
- Criticality is not solely determined by equipment complexity but by its impact on revenue generation.
- Having KPP data for critical equipment provides a competitive edge for maintenance teams.
By implementing effective measurement strategies, maintenance planning, and reliability practices, manufacturing plants can strive for excellence and optimize their OEE scores, leading to increased productivity, reduced downtime, and improved overall performance.