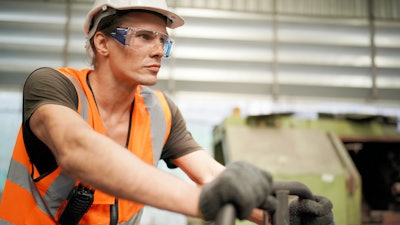
Productivity, the rate at which your employees produce per hour worked, is a major key performance indicator which can determine whether a business delivers a profit or a loss to the shareholders. Proactive business leaders know that a productivity boost can help offset the typical 3% annual inflation rate, but inflation has currently reached a 40-year high of 9.1% with seemingly no end in sight. Add to that a global labor shortage resulting in the biggest supply chain crisis in a generation, and it’s easy to see that manufacturing companies are facing critical challenges with fewer resources than ever.
Is it possible to ramp-up productivity significantly enough and quickly enough for companies to overcome these obstacles?
Significant productivity gains are attainable if the leaders strike the right balance between long-term strategic planning and near-term sprints. Far too often leaders underestimate what their teams can do right now to drive big leaps in productivity.
Double digit productivity gains within a short 90-days are possible but it requires a strategic alignment from the senior leaders, and is dependent on interdepartmental workflows, training, and maintenance practices. Because many productivity initiatives are siloed within the CI, Operations or Engineering teams, goals are often missed, resulting in a frustrated management team and a disengaged frontline workforce. Very frequently this creates a ‘flavor of the day’ feeling on the shop floor.
The problem with a siloed approach to productivity is that, without the urgency and agency to act, meaningful productivity gains are tough to realize. Frontline workers go without the tools they need to keep up maintenance, spearhead unexpected fixes, or switch gears for a new production run. These challenges require immediate, small-scale action — not slow-to-implement systematic changes.
Emphasizing Immediate Productivity Paves the Way to Profit by Addressing Challenges as they Arise
Employers can harness immediate gains by empowering the connected worker. By recognizing that challenges are opportunities to develop resources and skills, management can empower their employees to rise to each occasion and — in the process — boost productivity.
When employers provide access to training tools, real-time productivity stats, and feedback for employees to continually improve their performance, their employees experience less stress and burnout, take fewer sick days, are more engaged at work, and have an overall enhanced satisfaction in their work and personal lives.
What Can Manufacturing Leaders Do to Emphasize Immediate productivity?
There are multiple ways in which a plant can improve productivity while managing strain on workers. Here are four primary focus areas:
Invest in new technology.
Factory machinery can only produce a limited number of units in a set amount of time. Leaders can improve the rate by updating their machinery and using existing machines at their fullest capacity. minimizing downtime, honing maintenance schedules, and developing workflows which can switch between runs in record time. Downtime alone can cost manufacturers $50 billionLance OlmstedRedzone
Hire, train, and retain a workforce that wants to continually improve.
Trained, competent workers who solve problems quickly are essential. Improving immediate employee productivity starts with hiring but includes retention and training since workers get more productive the longer they stay. Further, high turnover is a costly input with little payoff. Retaining stellar employees is also beneficial: the top 5% of employees currently produce 26% of a company’s output.
It doesn’t have to be that way. Everyone can be a star employee, and plant managers can work to develop all employees to top productivity levels and then retain them for years. Emphasizing immediate productivity helps to cultivate an environment where your already valuable employees can grow with the training and tools they need to continually improve.
Practice strategic and supportive management strategies.
Managers who review performance indicators and recognize employees based on achievement grow faster while increasing productivity. Management practices alone account for around 20% of the variation in productivity between firms.
A connected workforce solution goes beyond knowing those performance indicators. Managers can make sure their employees have real-time information about how the team is doing, too. That way, employees can make productivity gains on their own. It’s about empowering the frontline to drive their own success.
Use effective communication to implement process changes fast.
Are there redundancies in workers’ tasks? How is specialized knowledge transferred through the organization, codified, and taught? Leaders should structure the workplace to promote efficient use of employees’ time and make the best of their talents. Poor organizational processes are responsible for squandering 20% of an average company’s potential productivity, but good processes are capable of bringing it back.
Those processes don’t have to take months to identify and implement. Make communication simple between departments so employees can access specialized knowledge throughout the plant. Make sure that just-in-time information is available to all. That way, employees can act on it as soon as they see a bottleneck.
The Benefits of Emphasizing Immediate Productivity
Employee wellbeing is a side-effect of empowerment, which also contributes to productivity, for an amplified positive effect on plants. Businesses get ahead when they give employees the power to see performance metrics and make improvements. Here are some advantages they gain:
Corporate return on investment
Productivity lowers operating costs while raising output. Business leaders can use those higher returns for many things, including new technology or new hires to further grow their businesses. It can be leveraged to raise capital to fuel future growth. And it’s heavily reliant on productivity, since a 5% productivity increase is associated with an 11.9% stock appreciation.
Widespread economic success
Productivity gains have an enormous impact on the financial success of companies, and in turn, entire economies and communities. The U.S. business sector increased its production of goods and services by nine times since 1947 due to productivity increases. Immediate productivity increases output with no extra labor — increasing supply, lowering prices, and raising standards of living for all.
Improved customer satisfaction
Being more productive means goods are made and delivered faster for happier customers. Lead times shorten. Production quality is high. It’s a combination that makes it easy for customers to order again. That’s good news for manufacturers faced with the reality that 82% of business buyers find technology has made it easy for them to turn to a new manufacturing partner.
Lower prices and more sales
Customers will also appreciate that high productivity leads to lower prices. Higher production with fewer resources means prices fall, making goods more affordable. That’s another win for customer satisfaction while also increasing profits. While producer prices have risen more than 4% in the last year, ongoing advances in productivity offset these costs and allowed factories to produce more goods for less.
Attract better talent and reduce turnover
Increased productivity returns can be used to raise wages and offer higher starting salaries to attract more employees. That helps keep great workers on the job, lets factories offer better growth opportunities, and makes the plant an attractive option for career-seekers in the community. Whether it’s the fear of losing a well-paying position or the morale-boost from earning a higher wage, increasing employee pay by $1 increases productivity by more than a dollar.
Reshaping the Future of Manufacturing today
Factories are drowning in rising costs from inflation, labor shortages slowing the lines, and sluggish supply chains. Instead of focusing on long-term plans that are slow to implement, companies can take a proactive approach to realize immediate gains.
Emphasizing immediate productivity empowers companies to develop creative solutions within an employee-friendly framework. With the right tools and processes in place, everyone can see what needs to happen to “win the shift.”
Redzone knows that empowering workers and factories is critical to drive success in uncertain times, ultimately, providing workers with better ways to do their jobs just makes sense.
Read more about other strategies manufacturing companies can implement to offset market challenges in our new guide: 5 Strategies for Breaking Through the Manufacturing Labor Shortage and Scoring a Big Win
About the Author
Lance Olmsted leads Redzone’s Enterprise and EMEA teams. Lance has a strong background in organizational leadership, refined through his tenure in the United States Marine Corps and within the manufacturing industry with a focus on factory operations. At Redzone, he ensures the company’s product and coaching model fit hand-in-glove to deliver productivity uplifts and a culture change for manufacturers – the hallmarks of Redzone.