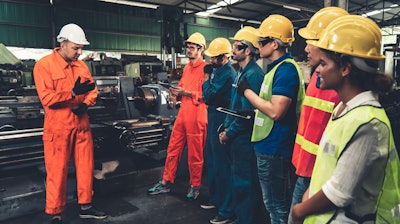
It never ceases to amaze me how people in factories relate to their equipment. Through over three decades of leading and transforming operations, making material and information flow, it is striking the relationships that people can form with an inanimate object.
Here are some observations I have made over the years:
- People become attached to their equipment as though it is their own personal property. This makes it particularly difficult to move people between and among operations when productivity numbers or criticality of certain job orders dictate such changes.
- They find ways to fix equipment with MacGyver-like ingenuity. I have literally seen this done with duct tape and cardboard more times than I care to remember.
- This leads to trusting their equipment or their ability to operate said equipment and look for ways to override or not use safeguards that have been put in place to ensure the people go home in one piece with all of their digits.
- People finesse the machine settings often without documenting them nor sharing with others on different shifts what works best which causes different levels of performance from seemingly identical jobs.
- They do not enjoy shutting their machines down to do routine maintenance which can cause longer than necessary downtime when the machine has not been planned for properly.
- Operators do not enjoy shutting their equipment down for changeovers. Oftentimes, they overproduce parts which uses up critical material needed for more urgent jobs.
- On many occasions, I have called an engineer to come and fix a piece of equipment. However, they fix the equipment without explaining to the person who spends the most time with it what may have caused the issue or how they fixed it.
We must consider the possibility that if we help foster the human element of the relationship between an operator and his or her piece of equipment, we might get better outcomes.
Additionally, we must truly embraced people’s need to find autonomy and meaning in their daily lives. If they primarily run equipment, we need to find a way to foster healthy interactions with those pieces of equipment that comprise the majority of their days.
We can use storytelling to help inspire our team members to not be risky with the safety features of their equipment and share incidents when others were not so lucky with the risks they took.
Schedule time to do routine maintenance and make the goals set around those times such that there was no decision that had to be made on the part of the operator that risked consequences of not meeting his/her numbers.
Give a team a set of equipment with goals/instructions/standard work and measure the team’s performance.
Provide visual controls so that when something goes wrong with that equipment, the proper resources were there to help fix the situation and support the operator.
Ask the operators for their ideas of what would make changeovers easier for them or what was the best sequence to perform them in.
Challenge one another as operational leaders to consider both members of the man/machine relationship so that both can perform optimally.
---
Shannon Karels and Kathy Miller are co-founder of OpSisters, a training, consulting and coaching organization in 2020. They work with companies, teams and individuals interested in improving business performance results through proven lean principles and inclusive cultures. They are also co-authors of STEEL TOES AND STILETTOS: A True Story of Women Manufacturing Leaders and Lean Transformation Success (Routledge/Productivity Press, 2021).