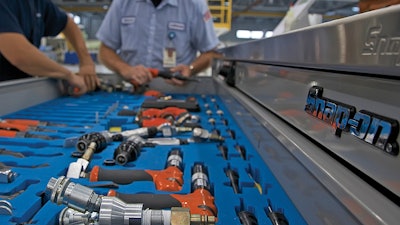
Essential tools go missing from facilities and job sites every day. Many are inadvertently lost or misplaced, but some unfortunately are stolen, in certain cases swiped right from tool boxes without anyone knowing – until that tool is needed again.
While the cost of replacing one missing tool may not seem like a big deal, the expense quickly adds up when multiple tools go missing over the course of a year, not to mention the lost productivity and delays in completing jobs. That’s why more companies today are looking to develop tool management programs as a way to better manage their assets, reduce their number of missing tools, and ultimately save money in the long run. Effective tool control programs range from simple foam cutouts that allow technicians to see if a tool hasn’t been replaced, to more advanced smart boxes the track and record tool usage in real time.
Getting Started with Tool Control
Any credible tool control system should meet five criteria: organization, visibility, access control, asset management and automation. These factors, when added together, give technicians and companies the means to fully control their tooling systems.
Questions to ask when designing a tool control program include:
- What is the goal of a tool control program for your organization?
- How extensive will the program be?
- What tools and equipment will be monitored?
- Who can perform a general inspection of the area?
- What is your budget for your tool control program?
Answering these questions will help organizations craft a tool control program that best fits their needs. Tooling suppliers can assist in evaluating tool control needs and recommend options that can meet an organization’s goals and expectations. The more reputable suppliers have proven tool control options available, such optical imaging and RFID technologies, visual tool control, keyless entry tool boxes and custom foam cutouts that, when working together, provide a tool control program that’s safe and effective.
Optical Imaging Technology
Optical imaging technology represents the highest level of tool control, and is a system adopted by many industries where tracking tools is critical to their operations. The system uses optical imaging to scan each drawer as it opens, comparing real-time images with the original image of the full drawer. To get started, technicians scan their employee badge, unlocking the box to gain entry. Each badge is granted access by management so that only specific privileged individuals can then access the box, and all tool withdrawals and returns are recorded to that user. A monitor affixed to the top of the toolbox visually shows the technician each drawer, and what tool has been taken. These transactions are also recorded by the administration software allowing management to have full visibility (via PC or laptop) to activity related to the toolbox. This also provides the opportunity to have the tool storage unit and the admin software in two different locations, cities or even countries!
As the box is accessed to remove or return tools, the system scans each tool in the drawer to determine its status. An audio system also announces tool issue and return. If tool status is questionable, the system can display the disputed tool transaction on the LCD screen or it can be identified in the audit image at the administrator’s PC. User log data and time-date information is available for every transaction.
RFID Technology
Hand tools that fit nicely in their foam cutouts are perfect candidates for accountability using optical imaging, but what about larger items, such as extension cords, tools kitted in fabric carrying cases, or personal protective equipment? These items still need to be tracked, but are too bulky for a traditional tool box. Enter RFID.
Lockers can be outfitted with RFID technology to track these larger items by simply placing a RFID tag on each one. And like optical imaging, some of these lockers offer badge security and audio systems to alert the technician of which items have been removed and then returned.
Using these technologies, items are automatically accounted as they are removed for use. When the job is complete, items can be placed anywhere within the locker to be tracked as returned. The intelligent tagging system allows it to operate at the speed of work in real time; the system verifies everything the technician checked out is accounted.
Visual Tool Control
While optical imaging and RFID rely on technology for tool control, a technician’s own eyes can be an effective method as well. Some tooling suppliers are now designing boxes with visual tool control, which give technicians a full view of their tools for instant accountability and asset management. These mobile, single-layer, glass-covered toolboxes can hold approximately 100 tools, and are ideal for point-of-use on specific job taskings.
Keyless Entry Tool Boxes; Foam Cutouts
Other methods of controlling tools include keyless entry and foam cutouts. Keyless entry, which allows technicians to use proximity badges and/or keypad entry to gain access into their toolboxes, improves productivity by eliminating the need to replace toolbox locks when keys get lost, or having to cut new keys when originals are misplaced. Accountability is achieved by allowing only authorized technicians to unlock the tool box.
All tool boxes should have foam cutouts or clearly marked designated spots for tools. This allows a technician to quickly scan a drawer and see if anything is missing. And, all items need to have a specific place. The practice of leaving one drawer in a tool box as a “catch all” for those miscellaneous tools and supplies needs to be abandoned. Again, how can a technician know if something is missing if there’s not a designated place for everything?
Companies can run a leaner operation by getting a better handle on their tools and equipment. To get started, select a reputable tool supplier, as they can work with you to evaluate your needs and recommend a course of action. When technicians know where their tools are, they’re more efficient…and that keeps your operation running efficiently.
John Ficcadenti is the product manager for the Level 5 Tool Control, as well as other tool control systems at Snap-on Industrial. He can be reached at 262.656.7901; [email protected]; https://b2b.snapon.com/.