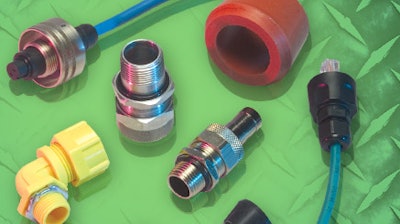
Failure of a single electrical connector can stop production in a split second.
Repair time depends mainly on the type of connection that is used, and the right connector can make repair time a matter of minutes, versus several hours of hardwiring.
The right cord grip, cable gland or connector can also help to prevent failure in the first place.
Once the right technical foundations, such as AWG and OD, are selected, look at the application itself. Ruggedized connectors withstand the environment better, with stronger protection against the elements that are often the point of failure.
Technical Foundations
These first 4 points are critical to choosing the right electrical connector for industrial-strength reliability. You must consider all 4 together. Never ignore or estimate any single factor to ensure connections won’t be compromised over time.
- Wire Gauge (AWG): Ensure the wire gauge is within the allowed range of the connector contacts. Typically, crimped contacts will allow a smaller range, and threaded contacts will accommodate a larger range of wire gauges.
- Cable Outside Diameter (OD): Specify the correct OD to ensure proper connectivity and ease of installation. If the OD is too small compared to the housing, it won’t seat properly. If the OD is too big, it may not install at all.
- Number of Contacts: The number of contacts in the connector should always match, or exceed the number in the cable. Don’t forget to include the ground in your calculations.
- Maximum Voltage and Current: Guarantee safety by specifying a connector that is rated for the application’s voltage and current ranges.
The Applications
Once the foundations have been defined, assess the environment in which the connector will be used. Industrial applications require much more than standard connectors in many cases.
Dry, indoor environments where there is no threat of corrosion, abrasion or cable strain are well suited for standard aluminum connectors.
Harsh environments and applications require a stronger, ruggedized connector for long-term reliability.
- Bending, Flexing & Vibration: Straight, 45- and 90-degree standard cord grips will provide the flexibility needed when connections need to move with machinery. Couple them with wire mesh grips for added stability and pull-out protection.
- Wet & Submerged Applications: For basic corrosion resistance, anodized or nickel-plating can hold up to humidity and light condensation. Add a drain fitting to release condensation within the enclosure. To withstand a large amount of water, or even submersion, Stainless Steel or non-metallic cable glands should be specified. Nylon and Valox™ offer a level of corrosion resistance you won’t find in metallic versions.
- Extreme Temperatures: Silicone and Stainless Steel connectors are ideal for these applications. For extreme heat, consider Valox or Nickel-Plated Aluminum. For extreme cold, consider Viton or Neoprene.
- Vertical Runs: Use strain relief grips for heavy-duty applications, or wire mesh support grips with a single eye, double eye or locking bale for lighter-duty.
- EMC: Get the best EMC shielding from cable glands that integrate the gland into the connector housing. This type of design not only shields the connection, but also eliminates a potential leak between the housing and strain relief.
- Chemical Contact: Upgrade connector materials to Stainless Steel, or non-metallic connectors such as PVC, Valox, Silicone or Viton.
Scalability
A final point to consider when selecting the right connector is its scalability to future changes. A great example of this is the quickly-expanding industry of computer server data centers.
As data centers add servers and equipment, they also need to guarantee 100% uptime for the increased bandwidth needed to fuel the speed of the internet.
Many data centers are now specifying 2” standard aluminum cord grips, instead of hardwiring. This allows them to handle increased demand, and replace connectors easily, long before they become a problem.
Cord grips coupled with wire mesh grips further strengthen the connection and ensure that connectivity remains, even during an earthquake.
Remke has been manufacturing electrical connectors in Chicago for over 50 years. For more information, visit www.remke.com.