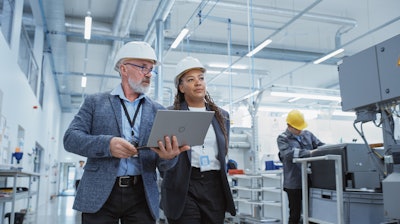
Control Station (Manchester, CT) announced a new turn-key digital lifecycle solution to partner with plants to optimize their control systems.
Their solutions team will work with plant champions to provide services to analyze and create unique plant-specific engineering plans, then proactively monitor, prioritize and resolve control loop issues. Manufacturers implementing this program have gained from reduced variability and increased reliability leading to savings of millions of dollars otherwise lost to lower productivity and wasted resources.
Features:
- Fills knowledge gaps or lack of human resources
- Control loop optimization knowledge/experience and best practices
- Software tools for data collection, analysis, reporting and recommendations
- Built around PlantESP software tool
Once initial optimization is performed, the lifecycle leading to continuous plant performance improvement incorporates the following steps:
- Monitoring performance, identifying negative trends and prioritizing issues based on select business and technical KPIs and operational impact
- Analyzing data collected and documented during monitoring process to identify trends and patterns
- Performing routine audits to assure compliance with standard operating procedures and to address deviations that jeopardize output or quality
- Conducting periodic reviews to assess performance of process control monitoring system, including analysis of collected data, reviews of alarms and notifications and effectiveness of control measures