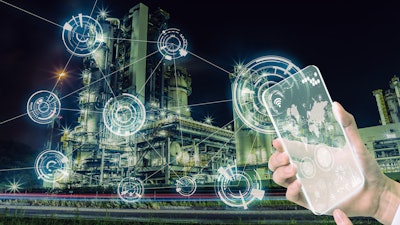
Downtime is a challenge as old as manufacturing itself – and something that industry has long solved with innovation. More than 100 years ago, for example, Henry Ford’s famed moving assembly line proved to be a far more productive alternative to relying on “runners” to deliver parts to autoworkers at a 50,000-square-foot production plant.
Today, innovation abounds in manufacturing. Connected, more data-driven operations combined with disruptive technology like augmented reality (AR) and artificial intelligence (AI) are unleashing unprecedented production insights and new and smarter ways of working.
This digital transformation is often discussed in the context of “smart manufacturing.” But it’s just as relevant to machine maintenance as it is machine operation. And a smarter, more efficient and data-driven approach to maintenance is something industry needs right now as challenges like the global skills shortage and pandemic threaten uptime and productivity.
Three Opportunities
There’s no rulebook that defines what smart maintenance is or how to implement it. Instead, every company must decide what maintenance problems it wants to solve and what technologies can solve those problems while delivering the best ROI. This can seem like a lofty endeavor given the wide range of smart devices and software available on the market. And in some cases, the best approach is to bring in an experienced partner that can bring focus and purpose to a smart maintenance initiative.
However, sometimes all companies need is an understanding of the enabling technologies to spark an idea. With that in mind, here are three key technologies that can help improve maintenance strategies and reduce – or even avoid – unplanned downtime:
1. Smart Devices
A wide range of smart devices provide diagnostic and operational insights to help technicians respond to issues quickly and proactively. Smart sensors, for example, can monitor virtually any parameter of an operation to create a clear picture of what’s happening with an asset, process, or even entire facility. They can also provide insights into their health and communication status to help technicians address issues quickly and possibly before they cause downtime.
Smart safety devices can also reduce downtime. Traditionally, safety devices are hardwired in a series and lack diagnostic data. This can make it difficult to pinpoint device failures. Smart safety devices can provide safety and diagnostic data over EtherNet/IP, which can help technicians quickly identify what specific safety device has an issue.
Smart motor-control devices can also deliver valuable health and performance insights to help protect uptime. Smart electronic overload relays, for example, can offer real-time motor diagnostics and time-to-trip insights to help technicians proactively identify and address issues. And smart servo drives can calculate the remaining lifespan of key components so technicians can replace them before they fail.
2. AR Technology
Technicians can better collaborate with colleagues and partners, and discover entirely new, more efficient ways of working when they use the power of AR technology. Consider how technicians work with remote partners like OEM support engineers today. If a technician is trying to diagnose a machine failure, for instance, they can spend considerable time trying to describe and troubleshoot the problem with a support engineer over the phone. If they can’t resolve the problem this way, the engineer may need to travel on site to fix the issue, extending the downtime from hours to days.
Using AR technology, the support engineer can join the technician in an AR experience. The engineer can see what the technician sees and even make 3D digital notations in the AR environment. This can considerably speed up troubleshooting and repair times – and deliver big savings if the support engineer doesn’t need to travel on site.
Technicians can also access digital work instructions in an AR experience. This instant access to repair or servicing instructions can reduce service times compared to using paper-based maintenance manuals.
3. Cloud-based CMMS
A cloud-based computerized maintenance system (CMMS) can help maintenance teams work more efficiently and catch red flags that they may otherwise miss. For example, repairs and preventative maintenance (PM) aren’t always avoidable. But this work can be done more efficiently to reduce downtime. Using a cloud-based CMMS, production staff can log work requests, create PM triggers, or even leverage sensors to create work orders based on a machine’s real-time condition.
Additionally, when a technician is responding to an issue, they can log into a mobile CMMS app from anywhere instead of needing to talk to a workstation where the CMMS is installed. The technician can also review an asset’s history, location of spare parts and more, to start repairing the asset faster. A cloud-based CMMS can even analyze work orders and identify the ones that are expected to cause serious issues like breakdowns. This can help maintenance teams prioritize – and prevent – problems.
Smart maintenance presents an opportunity to rethink how things are done. Smart devices can remove blind spots in production. AR technology can make collaboration instantaneous, even across time zones. Cloud-based CMMS can turn work orders into a source of insights.
But soon, smart maintenance may not just be an opportunity, it may be a competitive necessity.