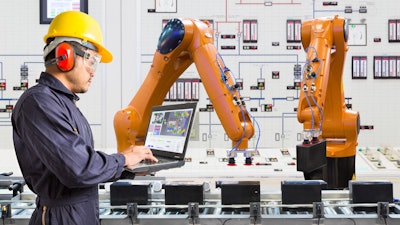
All manufacturing or logistics facilities experience downtime. From accidents and spills to malfunctions or maintenance, downtime is simply a fact of life. It goes without saying that downtime of any sort can cost a fortune - and that amount increases exponentially the longer the downtime.
In fact, recent research by Vanson Bourne and Aberdeen indicates that 82 percent of companies have experienced at least one unplanned period of downtime over the past three years - and that unplanned downtime costs companies $250K/hour, equaling more than $2 million in losses.
As a part of this process, it’s important to understand what causes downtime in the first place. Put simply, there are two types of downtime. The first is planned downtime, which includes shutdowns for maintenance, replacement, replenishment of resources (like paint), software updates, recalibration of machinery, or to bring new technology (such as robots) and equipment online. In many cases, there is little that can be done to prevent this type of downtime, but there are ways to shorten the time it lasts.
The other type of downtime is unplanned downtime. Unplanned downtime is unexpected, by nature, and can be caused by several things - power outages, breakdowns in equipment, human error, software bugs, robot miscues, or a complete disaster that sets off a chain of negative events. While this type of downtime cannot always be predicted or prevented, there are things that your organization can do to improve its preparation for these issues - and to mitigate the downtime when it happens.
Planned downtime is typically less disruptive than unplanned, but both amount to periods of time where your facility - and your business - is unproductive and revenue is being lost. Naturally, it is important for companies to figure out how to avoid, mitigate and prevent all types of downtime (and disasters) to the best of their ability.
Causes of Unplanned Downtime
There are many types of unplanned downtime, some inevitable, some uncontrollable, some random - but at the end of the day, most have a few key root causes. The potential for human error in any operation is well-understood, but understanding what the other common root causes are can help you be better prepared for downtime - and to rebound, recover and restart quicker than before.
- Wear and Tear. Simply put, wear and tear is a normal result of running industrial equipment in a manufacturing or logistics facility. Regular maintenance is required - but even when keeping up a maintenance schedule, machinery wears out and breaks - and doesn’t always do so on a schedule. For example, unplanned stoppages and failures are an inevitable result from the sheer volume of work that robots undertake. Round-the-clock usage causes degradation, which can cause critical parts to fail.
- Inadequate Design. Has your factory floor or assembly line been optimized? Planning out the entire operation, down to each detail, will improve your ability to cut down on everything from collisions to human error. Things that seem to be simple or no-brainers - such as locating goods in a reachable, close location, or making sure the path to bring a package to shipping isn’t obstructed, to making sure that a robot’s path doesn’t intersect with another robot (or a human) - all help in cutting down errors. There are software solutions that can solve collision problems for your operation right away, and proper planning and simulation will enable your team to better identify and respond to issues, such as ensuring that emergency equipment and shutdown buttons are located conveniently.
- Poor Preparation. It’s understood by all that unplanned downtime will happen. The type, length and overall effect of downtime depends on how prepared your team is to deal with it, however. Have you prepared a crisis plan? Have you trained your team on how to handle an immediate shutdown due to machinery failure, or robot collision, or a power outage?
- Technology Calibration. Has all your technology been setup correctly? Are your robots calibrated correctly and your workcells well-defined? Has the software been implemented correctly? Just as important as maintenance is, making sure your robots and the software that runs them has been set up correctly helps eliminate another cause of downtime.
- Technology Limitations. Are you asking your robots, machinery and other automated (or manual) tools to do too much? We’ve all been in situations where employees and managers push a robot or equipment to do “just a bit more.” Continually pushing the limits to try and wring more product and more productivity out of what you’re using inevitably ends badly.
- Lack of Monitoring or Alerting Tools. How are you monitoring the factory floor or assembly line? What do you have in place to notify you if there’s a problem? Does your system only look for confirmed problems - or is there a way to set up alerts when certain criteria are met - criteria that indicate a robot, or machine, or system is starting to fail? Part of mitigating a shutdown is identifying it early and getting to it before it becomes a massive problem and shuts down operations for days.
Once you’ve diagnosed the problem, it’s time to fix it. There are dual approaches, both equally critical to solving your downtime problems - reducing the number of downtime events and reducing the length of each downtime event. Here are some ways to improve your operations so that the ultimate effect that any type of shutdown - unplanned or planned - has on your organization is as minimal as possible and leads to a quick recovery:
- Maintenance. This is a no-brainer, but never skimp on regular maintenance. Robots and heavy machinery are designed to run for a long time, but to keep them running efficiently and to prevent unexpected disasters, set up a regular maintenance schedule in line with the manufacturer recommendations - and keep to it. Never overwork your existing technology.
- Simulation. Utilize software solutions that allow you to simulate downtime and recovery using a digital twin of your factory floor. Test out different reasons for downtime, and different solutions. Optimize as much as possible based on the most effective and efficient simulations - and create a plan-of-attack for every possible scenario. But after doing that, don’t keep them under lock-and-key; train your team so that they leap into action when downtime occurs.
- Training. Train your employees to notice signs of impending doom and to be able to troubleshoot and fix problems along the way; by the same token, also train them to recognize when a problem is too difficult to overcome (or outside their skill set), meaning they should call in the specialists.
- Review Data and Adjust. Track data on uptime, downtime and everything in between. What slows down efficiency? What makes things move faster? How long have delays and unplanned downtime lasted? What caused the disaster that stopped production - and has it happened more than once? Reviewing and learning from this data is invaluable when it comes to improving your processes. Learn from your mistakes - and invest in machine learning and artificial intelligence tools that can automate, assist and improve your readiness.
- Shorten Recovery Time. After downtime, it is critical to get a robot workcell, piece of heavy equipment, or employee-staffed production line running again as fast as possible. This is one area where your efforts can have the greatest positive effect on the length of downtime. In the case of robots, for example, a significant amount of recovery time is wasted moving each robot back to a “home pose” from which it can resume operation.
- Add Additional Automation. Even after all of this, you may find yourself in a situation where you need to drive more efficiency out of your operations and produce more product than before. Manufacturers rely on robot workcells to consistently deliver products in a speedy timeframe. However, there is a limit to your existing production line - and when you’ve reached it, it may be time to consider expanding and adding additional automation.
Getting to the bottom of why your operations experience downtime is key to solving the problem and speeding the time to recovery, but there are efforts that can be taken to reel in the unpredictability and costliness of downtime. Understanding your operations and taking steps to improve them and to be prepared stand to make your overall operations more reliable
Chris Harlow is the Senior Director of Product Development for Realtime Robotics.