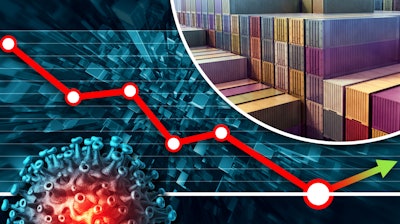
Some of the biggest ongoing stories in the manufacturing sector are led by shortages of various commodities or components. In early April, we covered how America is running out of ketchup packets. Nearly all automotive manufacturers have been hampered by a shortage of semiconductors over the past six months, leading Ford to state April 28 that it could cause the iconic company to cut its production by 50 percent. And no one will forget the infamous toilet paper shortage early in early stages of the COVID-19 pandemic.
We recently spoke with Hank Canitz, vice president of industry solutions for Nulogy — a provider of agile supply chain software solutions — to get his thoughts on the underlying causes of these shortages, and what can be done to prevent similar shortages going forward. Check out our conversation below.
Manufacturing.net: What caused the ketchup packet shortage we’re currently experiencing?
Cahitz
The recent news of the shortage of individual ketchup packets is a direct result of changing consumer habits. When the COVID-19 pandemic hit, in-person dining was quickly put on hold, so restaurants relied on takeout and delivery in its place. However, suppliers weren’t prepared to meet this sudden spike in demand, leaving restaurants scrambling to find solutions outside their typical suppliers and often at higher costs.
Manufacturing.net: What are the underlying issues within the supply chain that contributed to this shortage and others like it? How are organizations working to ensure it doesn’t happen again?
Canitz: For years, the manufacturing industry has been focused on cost cutting and efficiency by implementing just-in-time manufacturing processes and operating with as few outside partners as possible while still meeting demands. The COVID-19 pandemic exposed how brittle global supply chains had become. Low cost and efficient supply chains have a difficult time responding to change and recovering from disruption. Although the effects of the pandemic only represent a small percentage of any global supply chain’s risk, the increase in demand and supply variability caused parts and materials shortages, shipping delays and rising costs. The pandemic was the final straw that broke many global supply chains making it extremely difficult for manufacturers to fulfil orders using the supply chain they currently had.
CPG manufacturers turned to their external partners to help them gain the agility needed to quickly adapt to changing product demand. However, most industry 4.0 investments in supply chain capabilities have been focused on internal operations leaving the external network woefully unprepared for a massive uptick in volumes. To overcome these challenges and ensure they do not have the same issues in the future, manufacturers need to prioritize end-to-end supply chain data visibility and partner collaboration to improve overall agility and resilience. Manufacturers need to increase communication with their partners, have more insight into their operations and make more informed decisions when it comes to orders and capacity planning – critical to operational success.
Manufacturing.net: What parameters should be put in place to ensure a more agile supply chain?
Canitz: Investments in people, processes and technology that can improve end-to-end visibility within the supply chain must be top of mind for organizations looking to successfully navigate the post-COVID-19 world. The current lack of real-time collaboration and data visibility across external partners within the supply chain presents itself as a major risk to manufacturers. If external supply chains continue to grow with low visibility and structure, true agility will be hard to achieve – making it extremely difficult for manufacturers to keep up to rapidly changing customer demands.
Manufacturers should invest in solutions that enhance multi-enterprise process collaboration and data visibility between manufacturers and their contract packaging and manufacturing suppliers. Often, just by implementing solutions that can help automate partner collaboration on things such as order status, quality and material and machine capacity can make a big difference to being able to respond quickly.
Additionally, streamlining the new partner onboarding process makes it easier to add suppliers and respond to changes with agility. Multi-enterprise cloud-based platforms make the onboarding process quick and easy, eliminating the need to install physical software and minimizing system integrations.
Lastly, by extending real-time visibility to the supplier shop floor, manufacturers gain the same access to external manufacturing data as they have with internal plants. Real-time visibility to external partner operational data supercharges a CPG manufacturer’s ability to model and analyze a larger portion of the end-to-end supply chain. This enables available-to-promise and capable-to-promise capabilities for products made in internal and external plants – ensuring you never have to say no to an order due to the lack of visibility.