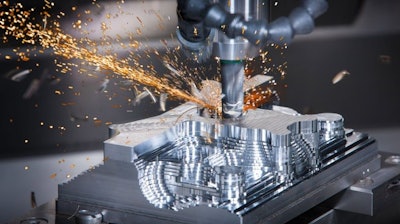
Despite the array of manufacturing equipment available, CNC continues to stay relevant, and if the incorporation of CNC machines in manufacturing was a notable innovation, the introduction of automation through CNC is nothing less than revolutionary. If you are out of the loop, then this post will be particularly handy in getting you up to speed. Here are some key benefits of using CNC automation in modern manufacturing:
1.Higher Speed
CNC machines collate multiple manufacturing steps into a single computer, which actuates its execution in a logical progression. As such, the use of CNC devices implicitly reduces the processing time. However, the use of automation augments these efforts and increases the turnover rate even further. Achieving higher speeds of operation is one of the most notable advantages of CNC automation. This advantage is particularly impactful in the manufacturing sector, where time is of the essence.
2. Greater Precision
CNC machines integrate with computerized technologies, such as CAD/CAM, to maintain accuracy after every iteration. As a result, they ensure high-degree precision in the manufacturing process. Furthermore, since automated CNC machines do not require human intervention and can operate autonomously, they can run 24/7 without affecting the quality of the products. As such, they deliver higher efficiency than their human-operated counterparts.
3. Improved Capacity
Automated CNC machines can cater to high-volume manufacturing lines without compromising on quality and accuracy. They can continuously, identically, and repeatedly produce the same item over and over again with zero user error. The combination of high speed, greater accuracy, and 24/7 operation allows automated CNC machines to increase capacity.
4. Design Consistency
As stated previously, CNC machines can produce the same item by following an identical set of steps repeatedly. At the same time, they can deliver accuracy that is within 1/1000th. Hence, the end design remains consistent regardless of whether it is the first product or the thousandth. And as a result, CNC introduces design fidelity throughout the manufacturing process. Moreover, even when a project is complete or temporarily suspended, manufacturers can retain the design in the software and prototype. When the unit restarts manufacturing the part, the automated CNC machine can refer to these data sets and resume the process in no time!
5. Reduced Waste Generation
Given the fact that CNC machines consistently produce highly accurate parts, they cut down on waste generation. The efficient use of resources and precision cuts limit the waste generated per piece, reducing the overall cost of production.
6. Design Intricacy and Complexities
Once you take care of the programming aspect, an automated CNC machine can follow the instructions down to the T. By honoring even the most intimate details, CNC machines can create highly accurate designs regardless of the design complexities involved. In fact, these products are better versions of the manual ones as the computer accounts for the minutest of details.
7. Simplicity of Operation
In regular conditions, CNC machines are easier to operate. However, when one adds automation to the mix, the management of these machines becomes all the more simple. A single operator can easily supervise, manage, and operate multiple CNC machines simultaneously. As a result, manufacturing organizations can cut down on labor costs.
8. Improved Safety
Automatic CNC machines do not require constant human supervision. Hence, they make the manufacturing unit a safe workplace. The operator simply needs to program the instructions into the CNC, and the machine will take care of the rest. Such devices can be a boon to manufacturing units that work with toxic or highly corrosive/abrasive substances or require adverse conditions, like high temperatures. They make the task of an operator easier and safer.
9. Reduced Downtime
Mobile CNC machines can mitigate the effect of planned machine downtime as they can be used as a supportive power tool. One can move them to the desired region during routine maintenance activities and continue their operation. As a result, it brings down the load or backlog when the traditional machining equipment is down.
10. Granular Control
Enterprises often outsource the manufacturing process to smaller workshops. However, automated CNC machines make the process more cost-effective and less labor-intensive, making in-house manufacturing economically viable. The greater control that comes with in-house manufacturing is a fringe benefit that complements the production.
CNC automation offers high speed and high precision cutting, milling, and drilling operations that no human being can achieve. These devices also bring about an element of versatility as one can program them to perform a gamut of operations without changing the equipment. As a result, they can streamline the manufacturing process while offering unlimited scalability.
Most interestingly, CNC machines continue to assimilate changes and evolve accordingly. And as CNC machining turns more accessible, the equipment can be an asset to any manufacturing entity regardless of its domain or size!
Peter Jacobs is the Senior Director of Marketing at CNC Masters.