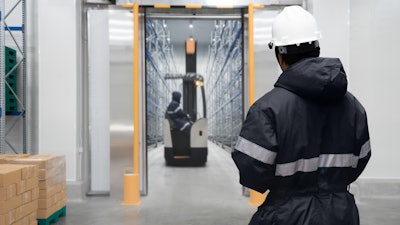
Compared to traditional warehouses and distribution centers (DCs) that are not temperature-sensitive, cold storage facility loading docks face a distinct set of challenges.
At the same time, the demand for cold storage facilities continues to grow due to accelerating e-commerce sales of frozen snacks, meat, and poultry, particularly within the grocery distribution segment. In fact, the online purchasing of refrigerated and frozen foods rose by 58% year over year as of October 2021.
According to the commercial real estate services and investment firm CBRE Group, Inc. (CBRE), e-commerce’s share of total U.S. grocery sales is projected to reach 21.5% by 2025 compared to only 13% in 2021.
In addition, CBRE reported last year that there were more than 3 million square feet of speculative cold storage development underway in the U.S., a significant increase from 300,000 square feet in 2019. The nation’s total cold storage real estate footprint is estimated at approximately 225 million square feet along with 3.7 billion cubic feet of gross refrigerated storage capacity.
Proper Design Requires the Right Equipment
All of that cold storage facility development will eventually result in a vast number of loading docks that require proper design as well as the right equipment to ensure that they keep warm air outside and the right amount of conditioned air inside.
The most critical components of a cold storage facility’s loading dock are the levelers, doors, seals and shelters. Let's examine each of these components in detail and why they're so important.
The Best Style Leveler for Cold Storage Facilities
Compared to traditional loading docks, which use a variety of dock levelers including mechanical, air-powered, and those that operate using hydraulics, the go-to leveler for cold storage facilities since the 1990s is the vertical storage leveler or VSL.
The key benefit of the VSL is that it allows trailer doors to swing open into the cold storage facility after the trailer is docked. At traditional loading docks, trailer doors are typically opened before the trailer backs up to the loading dock position.
For a refrigerated trailer with an inside temperature of 22 degrees that’s loaded with ice cream while the outside temperature is 105 degrees, opening the trailer doors in the yard with a traditional pit leveler set up means rapidly losing the critical cold chain. Preserving the cold chain is paramount regardless of a cold storage facility’s inside temperature. With a VSL setup, opening the trailer doors from inside the building ensures that the refrigerated trailer will only be opened into the refrigerated space.
So from a dock leveler standpoint, the best approach is to use properly sealed VSLs vs. traditional pit-style levelers so that exposure to the outside air temperature is reduced as much as possible.
An additional consideration is that the design and construction process for cold storage facility dock positions is much different than traditional loading docks.
From the proper placement of conduit to the poured concrete shelf for the VSL itself, cold storage facility loading dock design and construction involve careful project execution which means clear communication among the trades and the general contractor as well as effective job site coordination.
Effective Doors are a Worthwhile Investment
Even though VSLs have been the leveler of choice for most cold storage facility loading docks for nearly three decades now, one of the most overlooked pieces of equipment is the dock door.
A lot of effort and investment is typically expended on specialized cooling systems and VSLs, only for cold storage facilities to settle on traditional sectional doors for their dock openings which can be a big mistake.
Standard insulated sectional doors simply don’t provide important features such as a comprehensive sealing system around the door’s perimeter and the benefit of minimizing thermal breaks.
With vertical rise freezer doors a highly effective but also extremely expensive consideration for cold storage facility loading docks, the best solution between that option and standard insulated sectional doors is a specially designed sectional door that’s designed to work with VSLs.
Key features for this type of door include extra high four-foot tall sections along with four-inch thick insulation that provides a high R-value (R-23). The tall door sections mean 50% fewer panel joints (compared to an industry-standard 24-inch high panel) to prevent conditioned air loss. And because the door is designed to work with VSLs, it doesn't require an impact-resistant design since the VSL itself helps to prevent door damage.
Sealing In the Cold Air
For cold storage facility loading docks, the primary key to sealing in conditioned air once the dock door is open for trailer access is to eliminate any gaps or areas where light penetration is visible between the dock opening and the trailer.
Not only will the right dock seal prevent unwanted transfer of air and wasted energy costs, it can also help to prevent what otherwise might become a very dangerous working condition for facility employees.
Much like condensation will form on a cold beverage in a glass bottle that's exposed to high humidity, so too will any cold metal surface on the loading dock that's subject to humid air infiltration. As the humid air condenses on metal surfaces, such as the VSL, the moisture can easily become frozen if the inside air temperature is cold enough. The result is a very slippery working surface that can lead to injured workers or even worse.
The right kind of dock shelter for cold storage facility loading dock applications will also ensure that all four corners of where a trailer meets the dock position opening are closed tight, thus eliminating any gaps once a trailer’s doors are open and the VSL is in its lowered position.
Investing for the Long Term
Just as a cold storage warehouse or DC needs to invest in a highly efficient cooling system that will maximize energy cost savings over the long term, the same holds for investing in the correct loading dock equipment. That means installing the right levelers, doors, and seals/shelters for their specific applications.
A cold storage facility’s loading dock equipment needs to work as a complete system. That involves a lot of specialized engineering from a vendor that is highly experienced and has a long track record in the industry. In addition, selecting a vendor that offers loading dock product features designed specifically for cold storage applications along with in-bed design expertise means that the general contractor will end up with the best possible outcome.
When taking into consideration that a dock position involves a few thousand pounds of steel, it’s reassuring to know what it’s hanging on, that it’s been thoroughly tested and vetted, is backed by solid engineering, and that it will perform to the highest standards as an integrated and proven system.