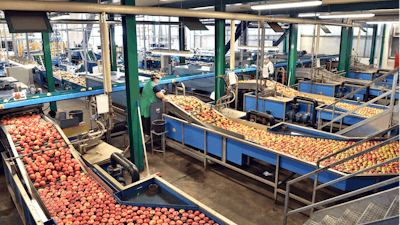
Headlines endlessly blast the beginnings and ends of supply chains with little thought given to the center distribution network. From the manufacturing of baby formula, to low stock on store shelves, not much thought is given to the middle of the supply chain where warehouses and distribution centers (DCs) tend to live and operate.
Implementing automation into your food warehouse operations has tremendous benefits to your overall supply chain functionality, from adhering to food safety regulations to increasing throughput and overall customer satisfaction.
Partnering with a strong and experienced automation partner to implement smart storage solutions like an automated storage and retrieval system (AS/RS) offers customers the adaptability to quickly react to sudden or various changes in the supply chain. Pairing an AS/RS with a robust warehouse execution system (WES), a software technology that marries warehouse control and warehouse management functionalities into a single software suite, greatly simplifies management of inventory and the fulfillment of orders.
Here are some other ways that warehouse automation is a smart investment as an intelligent supply chain tool:
Integration Capabilities
A WES possesses the flexibility of dealing with individual business processes, as well as the ability to integrate with other ERP software. This seamless integration with already established host systems offers real-time communication to relay information throughout the entire chain. A WES further controls the automation itself, allowing companies to forecast business needs more accurately while simultaneously communicating with other systems, preventing siloed data and contributing to organized, actionable data lakes.
Traceability
Perhaps one of the biggest benefits to those who store food and other perishable products is the value of real-time insights and dramatically improved traceability compared to undigitized storage facilities. A properly managed WES will provide traceability regardless of product location within the warehouse. Thanks to the absolute traceability provided by a WES and the excellent data tracking and record keeping, the ability to quickly utilize information for recalls is integrated in the flexible design. On the fulfillment side, the tools provided by a WES can be used to fulfill the business rules more closely for the end customer.
Multiple Deep Systems and FEFO
If your warehouse stores inventory with high lot quantities per item, odds are you will be best suited by implementing a multiple-deep AS/RS. Unlike a single- or double-deep system where inventory is accessible almost immediately, intelligent storage is vital with a multiple-deep system, especially when it comes to the standard of first expired first out (FEFO) in the food industry. A WES that was born out of deep storage automation controls the storage environment through a firm grasp on inventory algorithms and business rules, helping the AS/RS store products more intelligently than ever.
Admittedly, there are some situations and business partnerships where traditional FEFO rules become complicated, such as when dealing with big box stores that demand the newest products without exception. Luckily, a WES helps manage those inventory demands, as well, especially when backed by an automation company that has mastered complex inventory management through years of experience.
Reduced Touches
An AS/RS's rack structure is typically not readily accessible by humans–resulting in significantly less manual product touches in an automated warehouse as compared to a conventional one. In fact, product is typically only touched twice with an AS/RS, once when the product is received into the system, and once when it is being loaded at the docks for shipment.
The reduced touches are a huge benefit in food warehouses with food safety concerns due to human error. Unfortunately, pallet quality is usually low in the industry, so the reduced touches decreases risk of pallet stability problems. An additional benefit of the locked down inventory stored in an AS/RS is the elimination of pilferage, a big issue in the handling of high value products like wine and spirits.
Additional Advice: Build Big Enough
Undoubtedly, there will be required cost justification in the boardroom when it comes to deciding whether or not to automate your warehouse. However, it is crucial to think of an automation investment as a long term, strategic business objective that is worth the upfront cost for future payback, usually seen within five years.
Though the price of steel has increased along with other building materials, the steel rack is the cheapest part of an AS/RS. In fact, the automation itself, including the maintenance to achieve its 25 year lifecycle, is the portion that is the most costly investment, so build bigger if you can.
Holding more inventory provides security, safety, and higher customer service due to not being as reliant on potential supply chain disruptors. It is important not to assume that the vendor is always going to be reliable, so make sure to build a system that has the capability to hold reserve stock. It is also important to focus on building up your vendor and supplier networks to be able to source from multiple locations, just in case.
With a fine balance between managing order intake and how to supply products, be smarter about order management. Afterall, well managed companies will find ways to turn inventory in smarter and better ways and use the extra capacity to grow their business, not exclusively build inventory.
The consequences of not building big enough far outweigh the upfront investment cost of a bigger automated system. To not do so will resort to using outside additional warehousing, which is much more costly with extra transportation costs and skyrocketing fuel prices on top of the outside storage costs themselves.
Spending the extra money upfront and building a system that is adequate for future growth, seasonal peaks, or even evolving market behavior is much more cost effective than spending significant dollars on outside storage annually, for example.
Ultimately, the middle of the distribution network is massively underrated. There is enough evidence to show that if its efficiency is compromised, everything else slows down in a fragile domino effect. Warehouse automation is a key supply chain tool to ensure smooth operations from beginning to middle to end.
---
Dan Labell is President, Westfalia Technologies, Inc. Dave Williams is Vice President of Technology Solutions, Westfalia Technologies. For more information, visit westfaliausa.com.