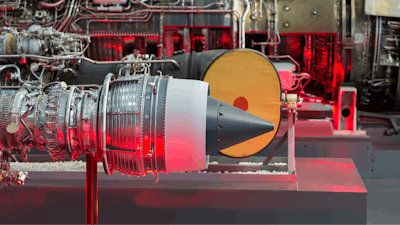
In discrete aerospace and defense manufacturing (A&D), where precision, efficiency and product quality are paramount, artificial intelligence has the potential to revolutionize every aspect of production, from production processes and quality control to predictive maintenance and supply chain optimization.
Although security-focused markets such as A&D have been relatively slow to adopt AI into manufacturing floor operations, the applications for this market offer impressive efficiency and revenue gains.
According to a recent survey by Microsoft and MIT Technology Review Insights, manufacturers that have invested in AI tend to be large companies bringing in $10 billion or more in annual revenue. Of the select few companies that fell into that category, 77% shared that they are already deploying AI.
However, in the A&D sector, that number drops to 30%. Yet, the benefits of adopting AI in this space are extensive. I estimate that even a 5% increase in efficiency could lead to millions of dollars in increased revenue, far surpassing the initial investment needed.
The AI Advantage in A&D Manufacturing
A vast majority of the current use cases revolve around automating cumbersome processes and finding efficiencies that can increase production and improve quality, saving both time and money.
The top four benefits that stand out for A&D manufacturing companies are:
1. Optimized production processes
The production process in the A&D industry is notoriously time-consuming, and the level of complexity often leads to extended timelines, causing delays in production, increased costs and strained customer relationships.
AI can fine-tune manufacturing processes, which is especially important in industries that need to quickly adapt to changing customer needs. By analyzing operational data in the MES, AI can identify bottlenecks and streamline operations to speed production planning and delivery.
Human-caused delays are common in long production processes. Automation and AI can manage repetitive tasks such as generating work instructions and process documentation. This enables employees to focus their attention on more valuable tasks. By empowering workers with AI-driven tools and insights, A&D manufacturing companies can realize significant productivity gains, reduce the burden of repetitive tasks and reclaim time for other revenue-generating tasks.
Additionally, AI-driven production scheduling and resource allocation can optimize workflow streams to minimize production inefficiencies and downtime and shorten production schedules. The result is a more flexible and scalable manufacturing environment and happier employees and customers.
2. Improved quality control
In the A&D industry, lives are on the line, and manufacturing requires absolute precision with no room for error. Even a highly trained human eye can only see so much. Computers do not blink, look away or get distracted.
Through AI-powered computer vision systems in an enterprise quality management system (EQMS), manufacturers can visually detect defects that might go unnoticed by human inspectors. Machine learning algorithms can flag inconsistencies and alert staff, ensuring products meet quality standards every time while reducing the time, cost and labor needed for manual inspections.
Additionally, AI advancements in supplier quality management technology enable real-time supply chain monitoring, as well as anomaly detection and automated supplier performance analytics. These tools can help companies better assess which suppliers are consistently causing problems and which are enabling success.
3. Enablement of predictive maintenance
Unplanned downtime is costly, sometimes to the magnitude of millions of dollars lost. AI-powered predictive analytics in the maintenance, repair and overhaul system can monitor and analyze equipment health through sensor data and predict when machinery is likely to fail. This allows manufacturers to perform predictive and proactive maintenance, prevent unexpected breakdowns and keep operations running smoothly.
4. Refined Supply Chain Management
Managing inventory levels is critical to delivering quality products on time. Supply chain issues that began with the pandemic continue to slow production and delivery timelines. The U.S. A&D market relies on raw materials and minerals from other countries, where geopolitical events and trade barriers can impact timely production and exportation.
AI provides a solution using predictive analytics for demand forecasting. By analyzing current inventory levels and upcoming project material needs, companies can stay ahead of shortages and deliver projects on time, resulting in lower costs and improved customer satisfaction.
All these AI benefits are transformative and can add significant value to manufacturing businesses, but they depend on one critical factor: data.
Getting Data-Ready for Your AI Launch
The most crucial element to getting data-ready for your AI launch is to ensure the digital infrastructure is in place.
To leverage the true potential of AI-driven technology, the shop floor must be digitized through the proper use of a manufacturing execution system (MES), such as Solumina. The MES enables context-aware data aggregation between information technologies and operational technologies (IT/OT).
Additionally, only a purpose-built MES for A&D can provide real-time monitoring of production processes, inventory levels and machine performance, making it an integral component of an AI-ready digital infrastructure. The MES should integrate with ERP and PLM for the closed-loop manufacturing capability while providing in-built enterprise quality management capabilities so that the shop floor personnel can act upon process deficiencies and product defects to trigger engineering changes.
Having these systems in place will help ensure the data across the organization, from shop floor to top floor, is suitable for AI, meaning it is comprehensive, accurate, up-to-date and easily accessible by AI. In addition, that data needs safe and efficient storage processes.
The Countdown to AI Launch has Started
AI offers immense opportunities for A&D companies to optimize processes, reduce costs and improve quality. However, to take advantage of AI's capabilities, manufacturers must first ensure their digital infrastructure is in place and their data is ready for AI.
By building a robust digital infrastructure with interoperable systems and smart, connected machines and equipment, A&D manufacturers can ensure real-time data is available so that AI solutions can do their best work. It’s not a quick or always easy journey, but the rewards, improved efficiency, reduced downtime and better-quality products, can lead to even bigger rewards in the form of improved customer satisfaction and increased revenue.
As AI is just beginning to enter manufacturing facilities, companies prioritizing data readiness today will be seen as leaders in the manufacturing revolution of tomorrow, with “all systems go” for their AI takeoff.
---
Sung is a technology architect and a published computer scientist with over 20 years of experience. At iBase-t, Sung has played a role in enhancing Solumina’s technology and exploring architecture experiments for future product directions. As the CTO, Sung leads iBase-t’s long-term technology vision and is responsible for the overall product architecture and infrastructure deployment profiles, focusing on open standards and integration technologies. Sung also facilitates the technical community within iBase-t.