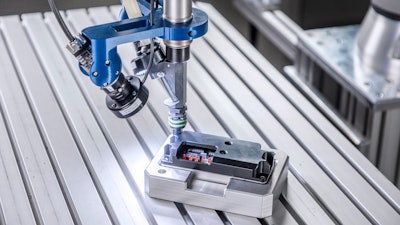
The AI experts at Micropsi Industries recently partnered with Deprag, an international industrial tool supplier, to create an automated screwdriving solution. It seems simple, but automating screwdriving assembly processes has proved elusive despite advances in industrial robotics.
Micropsi developed Mirai, an AI-powered robot control system that works with any industrial robot or cobot (collaborative robot). The system uses cameras and sensors to react in real time in dynamic workspaces.
Industrial Equipment News (IEN) recently had the opportunity to interview Matt Jones, general manager at Micropsi. In this interview, Jones discusses how his team solved automated screwdriving, why it’s more cost-effective than traditional solutions, and the seemingly limitless options that lie ahead.
IEN: How did you come up with the idea to create the automated screwdriving cell?
Matt Jones, general manager at Micropsi Industries.Micropsi Industries
In reality, varying shapes/orientations, inconsistent parts and other unforeseen variables cause all kinds of issues. A simple vision solution can work sometimes, but we had also been told those were often difficult due to highly reflective targets, like those found on metal screws, and varying angles. Therefore, a solution combining our AI technology with vision felt like a natural market need.
Most Read on IEN:
- Welding Company Scolded for Trying to Pay $23,500 Settlement in Coins
- Podcast: Tesla's Cybertruck Grave; Robots Make Human Slackers; $1.4M Bottle of Whisky
- Man With Second Pig Heart Transplant Dies
- Anheuser-Busch Is Still Struggling to Sell Bud Light in North America
IEN: How long was it in development?
Jones: Mirai has been in development for more than five years, but we did our first screwdriving application about three years ago. It happened naturally when a customer came to us with a failing robot solution. The customer made lighting fixtures, which are highly reflective. Plus, the tolerance their suppliers provided meant many broken parts.
As you can imagine, driving a screw into a lighting fixture can quickly make a mess on the manufacturing floor if you don’t line it up with the pilot hole. This customer was able to keep their existing robot cell and simply add Mirai to the setup in a matter of a couple hours. A few hours of training later, they had a working solution, no matter how much their suppliers’ parts varied.
IEN: Is this a more cost-effective solution than traditional automation?
Jones: Of course, adding an additional solution isn’t free, but it’s a lot cheaper than making bad parts. While Mirai can also help with labor costs, our customers consistently say that the value is largely in making “good parts.” One of the best parts of my job is to hear from customers that they never thought they could automate their tasks with such consistent precision but have now adjusted their stance after seeing Mirai at work.
IEN: Can it adjust to variances autonomously and on the fly?
Jones: Mirai is trained by showing our cameras different variances it may come across. Those variations can include things like position, shape, orientation, form and color. Our engineering team works directly with the customer to plan for as many variances we can predict as possible. We then process this data into our proprietary machine learning algorithms, and Mirai can then tackle variances that we didn’t even account for.
Occasionally, an unforeseen variance pops up, like if a supplier’s part becomes a different shade of color than it was previously. Often, Mirai will handle this flawlessly, but sometimes, additional training may be required. This is usually done in less than an hour, allowing minimal downtime. With the additional data, Mirai will become even more robust.
With that said, we have chosen to use a type of machine learning that only “learns” when we are in the training mode (imitation learning instead of reinforcement learning). This is important in manufacturing, as we don’t want the Mirai-enabled robot to start picking up on bad habits. Our customers need a consistent and controlled outcome.
IEN: What industries do you think stand to benefit the most?
Jones: Regarding screwdriving applications, the industries vary greatly. Naturally, automotive is most common, as that market tends to be the largest robot user base. Nevertheless, we’ve also solved applications in appliance manufacturing, electronic assembly, aerospace and more. Any industry that has screwdriving processes in their factories can benefit from the precision that Mirai offers.
IEN: Can human workers now be reliably repurposed from screwdriving assembly applications?
Jones: Absolutely. Not only can screwdriving work on an assembly line be dull and repetitive, there are also ergonomic concerns. Many of our customers are using large torque drivers, which deliver a lot of torque to the bolt. That counterforce has to go somewhere, and many of our customers agree to pass that onto robots instead of humans.
IEN: Any plans to attack other fastening or assembly applications in the future?
Jones: We’re always on the lookout for potential screwdriving, nut running and bolt driving applications. Whether it’s on a small electronic component or a large airplane wing, Mirai can handle the precision and consistency that customers require. The options seem to be limitless, and we feel we’re just getting started.
Screwdriving was one of the early robot applications many end users tried to tackle. However, many current solutions weren’t cutting it.Micropsi Industries