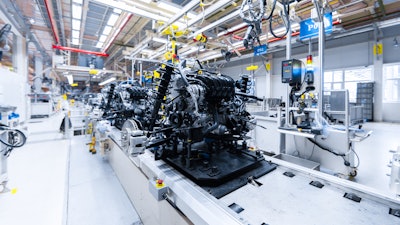
Nabil Nasr is the associate provost and director of the Golisano Institute for Sustainability at Rochester Institute of Technology. He is also the CEO of the Remade Institute, which was established by the U.S. government to conduct early-stage R&D to accelerate the transition to circular economy, which is a sustainable industrial model for improved resource efficiency and decreased systemic energy, emissions and waste generation. Below are highlights from an interview with The Conversation. Here, Nasr explains some of the ideas behind sustainable manufacturing and why they matter. Answers have been edited for brevity and clarity.
How would you explain sustainable manufacturing? What does the average person not know or understand about sustainable manufacturing?
When we talk about sustainable manufacturing, we mean cleaner and more efficient systems with less resource consumption, less waste and emissions. It is to simply minimize any negative impact on the environment while we are still meeting demand, but in much more efficient and sustainable ways. One example of sustainable manufacturing is an automotive factory carrying out its production capacity with 10% of its typical emission due to advanced and efficient processing technology, reducing its production waste to near zero by figuring out how to switch its shipping containers of supplied parts from single use to reusable ones, accept more recycled materials in production, and through innovation make their products more efficient and last longer.
Sustainability is about the proper balance in a system. In our industrial system, it means we are taking into account the impact of what we do and also making sure we understand the impact on the supply side of natural resources that we use. It is understanding environmental impacts and making sure we’re not causing negative impacts unnecessarily. It’s being able to ensure that we are able to satisfy our demands now and in the future without facing any environmental challenges.
Early on at the beginning of the Industrial Revolution, emissions, waste and natural resource consumption were low. A lot of the manufacturing impacts on the environment were not taken into account because the volumes that we were generating were much, much lower than we have today. The methods and approaches in manufacturing we use today are really built on a lot of those approaches that we developed back then.
The reality is that the situation today has drastically changed, but our approaches have not. There is plenty of industrialization going on around the globe. And, there is plenty of pollution and waste generated. In addition, a lot of materials we use in manufacturing are nonrenewable resources.
So it sounds like countries that are industrialized now picked up a lot of bad habits. And we know that growth is coming from these developing nations and we don’t want them to repeat those bad habits. But we want to raise their standard of living just without the consequences that we brought to the environment.
Yeah, absolutely. So there was an article I read a long time ago that said China and India either will destroy the world or save it. And I think the rationale was that if China and India copy the model and technologies used in the West to building its industrial system, the world will see drastic negative impact on the environment. The key factor here is the significantly high scale of activities needed to support their very large populations. However, if they are much more innovative and come up with much more efficient and cleaner methods better than used in the West to build up industrial enterprises, they would save the world because the scale of what they do is significant.
In talking about how these two countries could either ruin or save the world, do you remain an optimist?
Absolutely. I serve on the the United Nations Environment Program’s International Resource Panel. One of the IRP’s roles is to inform policy through validated independent scientific studies. One of the panel’s reports is called the Global Resources Outlook. The last report was published in 2019.
The experts are saying that if business as usual continues, we’re probably going to increase greenhouse gas emission by 43% by 2060. However, if we employ effective sustainability measures across the globe, we can reduce greenhouse gas emissions by a significant percentage, even by as much as 90%. A 2018 study I led for the IRP found that applying remanufacturing alongside other resource recovery methods like comprehensive refurbishment, repair and reuse could cut greenhouse gas emissions of those products by 79%–99% across manufacturing supply chains.
So there is optimism if we employ many sustainability measures. However, I’ve been around long enough to know that it’s always disappointing to see that the indicators are there; the approaches to address some of those issues are identified, but the will to actually employ them isn’t. Despite this, I’m still optimistic because we know enough about the right path forward and it is still not too late to move in the right direction.
Were there any lessons we’ve learned during the COVID-19 pandemic that we can apply to challenges we’re facing?
We learned a lot from the COVID crisis. When the risk became known, even though not all agreed, people around the globe took significant measures and actions to address the challenge. We accepted changes to the way we live and interact, we marshaled all of our resources to develop vaccines and address the medical supply shortages. The bottom line is that we rose to the occasion and we, in most part, took actions to deal with the risk in a significant way.
The environmental challenges we face today, like climate change, are serious global challenges as well. However, they have been occurring over a long time and, unfortunately, mostly have not been taken as seriously as they should have been. We certainly have learned that when we have the will to address serious challenges, we can meet them.
Final question. Give me the elevator pitch on remanufacturing.
Remanufacturing is a process by which we bring a product that has been used back to a like-new-or-better condition. Through a rigorous industrial process, we disassemble the product to the component level. We clean, inspect and restore it, qualifying every part. We then reassemble the product similar to what happened when it was built the first time. The reality is that by doing so, you’re using anywhere from 70% to 90% of the materials recovered from the use phase. This has significantly far lower impacts on the environment when compared to making new products from raw materials.
You don’t mine virgin material for that. You’re saving the energy that made those parts; you’re saving the capital equipment that made those parts; you’re saving the labor cost. So the savings are significant. The overall savings are about 50%. For example, a remanufactured vehicle part in the United States requires less than 10% of the energy needed to make a new one, and less than 5% of new materials. That means lower costs for the producer while providing the consumer with a very high-quality product. Examples of commonly remanufactured products are construction equipment, automotive engines and transmissions, medical equipment and aircraft parts. Those products are similar to brand-new products, and companies like Xerox, Caterpillar and GE all have made remanufacturing an important part of their overall operations.
This article is republished from The Conversation under a Creative Commons license. Read the original article here: https://theconversation.com/how-sustainable-manufacturing-could-help-reduce-the-environmental-impact-of-industry-185672.