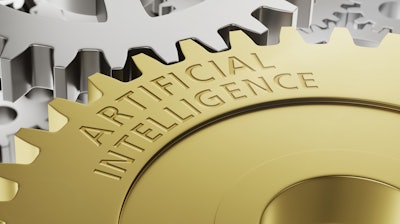
While Artificial Intelligence (AI) has been prevalent in industries such as the financial sector, where algorithms and decision trees have long been used in approving or denying loan requests and insurance claims, the manufacturing industry is at the beginning of its AI journey. Manufacturers have started to recognize the benefits of embedding AI into business operations—marrying the latest techniques with existing, widely used automation systems to enhance productivity.
A recent international IFS study polling 600 respondents, working with technology including Enterprise Resource Planning (ERP), Enterprise Asset Management (EAM), and Field Service Management (FSM), found more than 90 percent of manufacturers are planning AI investments. Combined with other technologies such as 5G and the Internet of Things (IoT), AI will allow manufacturers to create new production rhythms and methodologies. Real-time communication between enterprise systems and automated equipment will enable companies to automate more challenging business models than ever before, including engineer-to-order or even custom manufacturing.
Despite the productivity, cost-savings and revenue gains, the industry is now seeing the first raft of ethical questions come to the fore. Here are the three main ethical considerations companies must weigh-up when making AI investments.
1. How Will AI Impact Your Workforce?
At first, AI in manufacturing may conjure up visions of fully automated smart factories and warehouses, but the recent pandemic highlighted how AI can play a strategic role in the back-office, mapping different operational scenarios and aiding recovery planning from a finance standpoint. Scenario planning will become increasingly important. This is relevant as governments around the world start lifting lockdown restrictions and businesses plan ‘back to work’ strategies. Those simulations require a lot of data but will be driven by optimization, data analysis and AI.
And of course, it is still relevant to use AI/Machine Learning to forecast cash. Cash is king in business right now. So, there will be an emphasis on working out cashflows, bringing in predictive techniques and scenario planning. Businesses will start to prepare ways to know cashflow with more certainty should the next pandemic or crisis occur.
For example, earlier in the year the conversation centered on the ‘just-in-time’ scenarios, but now the focus is firmly on ‘what-if’ planning at the macro supply chain level:
- What if I were to switch my manufacturing from China?
- What if we experience supply chain disruption from a natural disaster in a certain county?
- There may be a price impact generated by one scenario, but what if I did a 70/30 split? What would that do to my margin and cashflow?
Another example is how you can use a Machine Learning service and internal knowledge base to facilitate Intelligent Process Automation allowing recommendations and predictions to be incorporated into business workflows, as well as AI-driven feedback on how business processes themselves can be improved or automated.
The closure of manufacturing organizations and reduction in operations due to depleting workforces highlight AI technology in the front-office isn’t perhaps as readily available as desired, and that progress needs to be made before it can truly provide a level of operational support similar to humans.
Optimists suggest AI may replace some types of labor, with efficiency gains outweighing transition costs. They believe the technology will come to market at first as a guide-on-the-side for human workers, helping them make better decisions and enhancing their productivity, while having the potential to upskill existing employees and increase employment in business functions or industries that are not in direct competition with AI.
Indeed, recent IFS research points to an encouraging future for a harmonized AI and human workforce in manufacturing. The IFS AI study revealed that respondents saw AI as a route to create, rather than cull, jobs. Around 45 percent of respondents stated they expect AI to increase headcount, while 24 percent believe it won’t impact workforce figures.
The pandemic has demonstrated AI hasn’t developed enough to help manufacturers maintain digital-only operations during unforeseen circumstances, and decision makers will be hoping it can play a greater role to mitigate extreme situations in the future.
2. Are You Honestly Assessing Potential Productivity and Profitability Gains?
It is easy for organizations to say they are digitally transforming. They have bought into the buzzwords, read the research, consulted the analysts, and seen the figures about the potential cost savings and revenue growth.
But digital transformation is no small change. It is a complete shift in how you select, implement and leverage technology, and it occurs company-wide. A critical first step to successful digital transformation is to ensure that you have the appropriate stakeholders involved from the very beginning. This means manufacturing executives must be transparent when assessing and communicating the productivity and profitability gains of AI against the cost of transformative business changes to significantly increase margin.
When businesses first invested in IT, they had to invent new metrics that were tied to benefits like faster process completion or inventory turns and higher order completion rates. But manufacturing is a complex territory. A combination of entrenched processes, stretched supply chains, depreciating assets and growing global pressures makes planning for improved outcomes alongside day-to-day requirements a challenging prospect. Executives and their software vendors must go through a rigorous and careful process to identify earned value opportunities.
Implementing new business strategies will require capital spending and investments in process change, which will need to be sold to stakeholders. As such, executives must avoid the temptation of overpromising. They must distinguish between the incremental results they can expect from implementing AI in a narrow or defined process as opposed to a systemic approach across their organization.
3. Take Ownership of AI Outcomes – Good and Bad
There can be intended or unintended consequences of AI-based outcomes, but organizations and decision makers must understand they will be held responsible for both. We have to look no further than tragedies from self-driving car accidents and the subsequent struggles that followed as liability is assigned not on the basis of the algorithm or the inputs to AI, but ultimately the underlying motivations and decisions made by humans.
Executives therefore cannot afford to underestimate the liability risks AI presents. This applies in terms of whether the algorithm aligns with or accounts for the true outcomes of the organization, and the impact on its employees, vendors, customers and society as a whole. This is all while preventing manipulation of the algorithm or data feeding into AI that would impact decisions in ways that are unethical, either intentionally or unintentionally.
Margot Kaminski, associate professor at the University of Colorado Law School, raised the issue of ‘automation bias’—the notion that humans trust decisions made by machines more than decisions made by other humans. She argues the problem with this mindset is that when people use AI to facilitate decisions or make decisions, they are relying on a tool constructed by other humans, but often they do not have the technical capacity, or practical capacity, to determine if they should be relying on those tools in the first place.
This is where ‘explainable AI’ will be critical—AI which creates an audit path so both before and after the fact, there is a clear representation of the outcomes the algorithm is designed to achieve and the nature of the data sources it is working form. Kaminski asserts explainable AI decisions must be rigorously documented to satisfy different stakeholders—from attorneys to data scientists through to middle managers.
Manufacturers will soon move past the point of trying to duplicate human intelligence using machines, and towards a world where machines behave in ways that the human mind is just not capable. While this will reduce production costs and increase the value organizations are able to return, this shift will also change the way people contribute to the industry, the role of labor, and civil liability law.
There will be ethical challenges to overcome, but those organizations who strike the right balance between embracing AI and being realistic about its potential benefits – alongside keeping workers happy will usurp and take over. Will you be one of them?