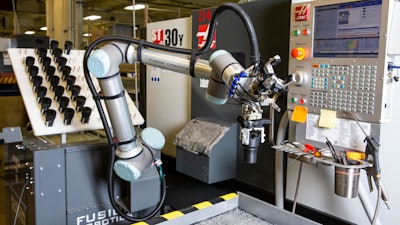
Cobots. Industrial Internet of Things. Machine vision and 3D printing. These technologies are part of the Industry 4.0 lexicon. But these smart technologies become much more than words when you consider adding them to your factory floor to increase productivity, competitiveness and profitability. As more manufacturers adopt Industry 4.0 technologies, best practices emerge for successful technology deployments.
In its ”Manufacturing Readiness Grants Program: 2022 Impact Report,” Conexus Indiana, a nonprofit focused on supporting the continued growth of Indiana’s advanced manufacturing industry, analyzed technology trends and use cases at 170 small to mid-sized manufacturers that have participated in the State of Indiana’s Manufacturing Readiness Grants program, which awards matching grants to qualifying manufacturers.
Through May 2023, 425 grants totaling $45 million have been awarded, stimulating private-sector project investments of $628 million. Additionally, Conexus Indiana has published nearly 50 case studies detailing these technology projects.
A workcell at Metro Plastics in Indiana.Conexus Indiana
In addition to painting a picture of Indiana’s Industry 4.0 landscape, the cases point to lessons learned. Here are four insights that may benefit companies preparing to make the Industry 4.0 leap.
- Assign an accountable leader: To be successful in the Fourth Industrial Revolution, companies must appoint an internal champion or project team and provide them with resources. A project lead should feel empowered to make swift project management decisions, compel collaboration and bring about technological change to a company’s operations.
- Take time to identify strategic business objectives and pair them with use cases: With more than a dozen technologies associated with Industry 4.0, the array of choices can complicate selection. For example, cobots are often deployed for machine tending or the assembly of low-volume, high-mix applications where manufacturing flexibility is required. Robots, on the other hand, are more commonly deployed for high-volume, low-mix welding and material handling applications where speed is essential, and production runs are extended. Selecting the right strategic business objective and matching it to an appropriate technology use case is critical.
- Engage the ecosystem of technology integrators: Many companies have benefited from working with the right technology integrator or automation solution provider. These trusted partners have specific expertise in delivering and deploying Industry 4.0 solutions into production environments, and they often assist through the full lifecycle of planning, implementation and workforce training.
- Invest in your workforce: The existing workforce is ready to learn digital skills and operate Industry 4.0 job functions. Emphasizing workforce development alongside the procurement of technology is the best way to maximize productivity. A spectrum of training options is available to accomplish this, including formal education, certificate programs and equipment OEM courses.
When Conexus first started studying Industry 4.0 technology adoption trends in Indiana, lack of clear return on investment (ROI) and internal skill presented two major barriers to widespread adoption at small to mid-sized companies. Enter 2023: Companies are acutely aware of the benefits and business impact of Industry 4.0 tech investments, and they know their workforce is up to the challenge.
Companies are stepping into more complex projects like machine learning, artificial intelligence, big data and analytics and autonomous mobile robots. Undoubtedly, the most successful companies will be those that keep these four insights in mind.
Ryan Henderson is director of Innovation and Digital Transformation at Conexus Indiana.Conexus Indiana