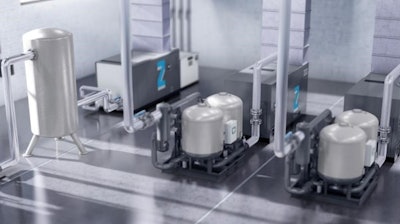
Compressed air is used in various applications, but while air compressors are vital equipment for automotive manufacturing, they can hurt your energy bill. Therefore, it’s important to design the smartest compressed air system to save energy and make the system more reliable.
Nearly 80 percent of the air compressor’s lifecycle cost comes from energy consumption. Reducing that consumption as little as one percent can yield yearly savings of thousands of dollars. Energy savings don’t happen without effort. They require analysis, planning and strategy, but the end result is worth it. By examining their demand-flow pattern, auto manufacturers can create smart systems that save air and money.
Typical Demand-Flow Pattern
Here’s an example of the typical demand fluctuation in an auto manufacturer over a 24-hour period:
Now that we know what a typical demand flow looks like, let’s compare two options for compressed air systems to see how automakers can best increase energy efficiency and reliability.
Option 1: Two 3,000 cfm centrifugal compressors
What’s happening?
With varying demand throughout the day, a fair amount of energy is wasted due to limited turndown range and blow-off of compressed air.
Why is this happening?
The flow and pressure of centrifugal compressors is controlled by an inlet device (IGV or throttle valve and blow-off valve). When the IGV position reaches the surge control point, the blow-off valve will open and exhaust the extra compressed air to keep the compressor operation away from the surge zone.
The surge condition is an aerodynamic instability observed in dynamic compressors like centrifugal compressors. Due to the aerodynamic instability, the compression stage cannot increase the pressure head any further due to its design. This leads to stoppage of flow initially and then the reversal of flow.
A surge condition leads to unstable operation due to the inducement of high-level stress to the compressor’s rotating components. To avoid potential damage, the compressor needs to be kept out of such surge occurrence.
Option 2: One 3,000 cfm centrifugal compressor + 1 variable speed drive (VSD) oil-free screw compressor
What’s happening?
The centrifugal compressor takes care of the baseload while the variable speed keeps up with flow variation to avoid blow-off, which saves up to 25 percent of energy consumption.
For example: 940 Kw for 4000 hours at 10 cents/KwH = 940 kW x 4000 hr x $0.10 kWh = $376,000. By reducing kW 25 percent (940 Kw x .25 = 235), you are using 235 Kw less, thereby saving $94,000 per year (235 Kw x 4000 hr x $0.10 KwH = $94,000)
How can I take full advantage of my smart compressor system? The recommended smart compressor system for auto-industry applications includes:
- Centrifugal compressor
- VSD oil-free screw compressor
- Heat of Compression dryer
- Central controller
A compression dryer and central controller can optimize your applications by further reducing your system’s electricity consumption with proper demand flow and minimum blow-off.
What are Heat of Compression Dryers and How do They Work?
Heat of compression dryers use heat from the compressor to regenerate the desiccant. Because the energy is coming from the compression process, users can save more electricity compared to other types of desiccant dryers.
Compression dryers are characterized by:
- No loss of compressed air.
- Zero purge by design.
- Low pressure drop.
- No filtration requirements.
An economical heat of compression option is the rotary drum type absorption dryer. Because heat from compression is used for regenerating the dryer rotor, less energy is required to reach very low dew points. The rotor recovers its original performance after being regenerated, so the dryer offers years of trouble-free, full-time operation at minimum costs. The dryer also has a very low pressure drop, which enables the compressor to operate at a lower discharge pressure.
What is a Central Controller and How Does It Work?
A central controller optimizes the compressed air system by selecting the right compressor to match the application’s demand flow. When using a central controller, the VSD compressors are kept at an optimal level and blow-off is minimized, and sometimes even eliminated.
Benefits of a central controller:
- Regulation of system pressure within a pre-defined and narrow pressure band to optimize energy efficiency.
- Prioritized use of newer, more economic machines over older, less effective versions for reduced downtime.
- Continuous use of VSD machines for variable loads and energy efficiency.
- Assurance that VSD and/or turbo compressors are operating efficiently when working together.
- Scheduled shutdowns that reduce costs during non-working hours.
- Optimized pressure stability, which reduces problems with air-operated equipment.
- Workload equalization to avoid overloads on individual machines.
What’s the best option for my facility?
It’s important to consult a compressed air expert when creating a smart, optimized compressor system. An expert can perform an audit at your facility to calculate specific benefits based on the applications you use and help identify cost-saving solutions. A hybrid compressed air system with a heat of compression dryer and energy-saving controller is the best solution when it comes to solving for fluctuating demand applications, reducing carbon footprint and saving energy.
Deepak Vetal is a product marketing manager of oil-free screw and centrifugal compressors at Atlas Copco Compressors LLC in Rock Hill, S.C.